Состав бетона — БЕТОНКОМПЛЕКТ
Состав бетона — БЕТОНКОМПЛЕКТОбратный звонок
Оставьте свои контактные данные и мы свяжемся с Вами
Нажимая на кнопку, Вы даете согласие на обработку своих персональных данных. Условия политики конфиденциальности.
+7 (342) 201-95-95
Товарный бетон (приготовленная в заводских условиях бетонная смесь) состоит из 4 главных компонентов. Это цемент, песок, щебень и вода, которые замешивают, придерживаясь определенной пропорциональности. Без щебня смесь получится совершенно другой и будет называться цементным раствором или пескобетоном с той лишь оговоркой, что в пескобетоне используется песок большего модуля крупности.
Чтобы получить бетон, компоненты для его приготовления применяют в следующем весовом соотношении:
- цемент — 1 доля;
- песок — 2 доли;
- щебень — 4 доли;
- вода — 0,5 доли.
Например, с 330 кг цемента используется 600 кг песка, 1,25 т щебня и 180 л воды. Цифры неточные, так как на практике большое значение имеет требуемая марка бетона, свойства используемых песка и щебня, марка цемента, использование или неиспользование пластификаторов, иных добавок и многие другие факторы. Условно говоря, если использовать цемент марки М-400, бетон получится соответствующим марке М-250, а с цементом М-500 марка бетона тоже повысится — до М-350. Вот почему при изготовлении бетонной смеси на заводе в расчет берут несколько десятков параметров.
Цемент и вода
Вода и цемент — основные компоненты бетона, которые выполняют главную функцию: связывают все составляющие смеси в единую цельную структуру. Одна из главных задач при производстве бетона — добиться правильного водоцементного соотношения. Причем речь идет не просто о количестве этих компонентов, а об учете таких характеристик, как влажность применяемого щебня и песка, степень их влагопоглощения и других подобных.
В процессе гидратации (контактирования с водой) цемент может схватываться и твердеть, в результате образуется цементный камень. Многие потребители сталкиваются с этим явлением в быту, когда, например, открывают мешок цемента, пролежавший длительное время в условиях сырости. Казалось бы, камень и так самодостаточен, для чего в этом случае вводить в смесь и другие компоненты? Дело в том, что цементный камень склонен к деформациям. Его объемная усадка может доходить до 2 мм/м. Несмотря на невысокий показатель, усадочные процессы приводят к внутренним напряжениям и образованию микротрещин, которые не видны, но отрицательно сказываются на прочности и длительности службы цементного камня. Уменьшить такие деформации позволяет введение в состав готовящейся смеси заполнителей.
Щебень и песок
Щебень используется в качестве крупного заполнителя, песок — мелкого. Роль этих компонентов в составе бетонной смеси — создать структурный каркас, противостоящий усадочным напряжениям. Благодаря добавлению заполнителей готовый бетон характеризуется меньшей усадкой.
Прочность щебня подбирается исходя из расчетной марки бетона: щебень должен быть прочнее примерно в 2 раза. Объясняется эта закономерность тем обстоятельством, что проектная марка бетона всегда ниже реальных прочностных характеристик, которые он набирает спустя полгода-год. Тогда как прочность щебня со временем остается прежней. Поэтому на практике разницу между прочностными показателями стараются свести к минимуму, хотя делается это в виде нерегламентированного проектными нормативами запаса прочности.
При использовании щебня важно учитывать еще много других нюансов, в том числе лещадность, процентное количество зерен слабых пород. Большое внимание уделяется видам щебня, основные из которых следующие:
- Известняковый.
Марка по прочности — 500-600. Отдельные виды наполнителя из известняка (до 800) подходят для производства бетона до марки по прочности М-350. Но из-за низкой морозостойкости известняк обычно не применяется при изготовлении высоких марок бетона. Его используют для получения марок от М-100 до М-300.
- Гравийный. Прочностных показателей основных видов гравия, как правило, достаточно для производства бетона до М-450. Это самый часто используемый вид наполнителя. Ему присущи все качества, нужные для получения разных типов бетонных смесей. Бетон на гравии получается в меру прочным и недорогим, что актуально для индивидуального строительства. К тому же радиационный фон такого материала меньше, чем гранитного.
- Гранитный. Относится к самым прочным среди других видов щебня. Отличается также более высокими показателями морозостойкости и низким водопоглощением. Поэтому используется в наиболее ответственных конструкциях, например, обязателен к применению (и не может быть заменен на другой в соответствии с ГОСТ) при строительстве дорог.
Процесс приготовления бетонной смеси
Если перевести весовые доли, указанные в начале статьи, в объемные, то получится, что для приготовления 1 м3 бетона требуется следующее количество материала:
- цемент при средней насыпной плотности 1300 кг/м3 — 0,25 м3;
- вода — 0,18 м3;
- щебень при плотности 1350 кг/м3 — 0,9 м3;
- песок при плотности 1400 кг/м3 — 0,43 м3.
При сложении показателей общий объем оказывается равным 1,76 м3. Как такой объем помещается в 1 м3 бетона, можно понять, рассмотрев простой пример. Если взять обычную литровую банку и заполнить щебенкой, то между зернами останется много межзерновой пустотности, т. е. свободного места. Эту пустотность можно засыпать, потряхивая и помешивая, двумя стаканами песка, стаканом цемента и залить стаканом воды. В результате всё вмещается и получается плотная консистенция. После этого бетон быстро начинает твердеть. Снова придать приготовленной смеси пластичности помогает вибрирование и перемешивание.
Готовая бетонная смесь имеет определенный буквенно-цифровой индекс и описывается с обязательным указанием марки (М) и класса (В) по прочности, подвижности (П), водонепроницаемости (W) и стойкости к морозу (F).
2022 Бетонкомплект
Отправить резюме
Состав бетона и смесей
Главная » Общие сведения о бетоне » Состав бетона
Срок службы и максимально допустимая нагрузка для изделий из бетона определяются соотношением компонентов цементной смеси. Несомненную роль играют степень уплотнения бетона, качества материалов и условий выдерживания бетона, но дозировка материалов на замес бетономешалки также играет первостепенное значение.
При производстве бетона в заводских условиях, составлением рецептуры бетона занимается специальная лаборатория. При этом проводится тщательное изучение всех компонентов. Песок может иметь различный удельный вес, пустотность, объемную массу, зерновой состав и модуль крупности, процент содержания глинистых частиц и органических примесей. Характеристиками щебня являются прочность, объемная масса, загрязненность, объем пустот, содержание пластинчатых и игловатых зерен. Для цемента определяющими факторами являются удельная поверхность и удельный вес, сроки начала и окончания схватывания, а также активность. Вода определяется по своему химическому составу, жёсткости, наличию органических примесей. Характеристиками бетонной смеси являются объемная масса, прочность, подвижность, водонепроницаемость и водоотделение.
Если есть такая возможность, готовый бетон лучше всего заказывать на заводе, откуда продукция доставляется на строительную площадку в специальных автобетоносмесителях. Таким образом, можно получить идеально подобранный для данных условий состав бетона, исключая попадение в состав осадков и посторонних компонентов, расслоения состава на фракции.
Соотношение компонентов бетона
(цемент марки М 500, песок, щебень)
Марка бетона | Масса компонентов, Ц:П:Щ, (кг) | Объём компонентов на 10 л раствора, П:Щ, (л) | Объём бетона из 10 л.![]() |
100 | 1 : 5,8 : 8,1 | 53 : 71 | 90 |
150 | 1 : 4,5 : 6,6 | 40 : 58 | |
200 | 1 : 3,5 : 5,6 | 32 : 49 | 62 |
250 | 1 : 2,6 : 4,5 | 24 : 39 | 50 |
300 | 1 : 2,4 : 4,3 | 22 : 37 | 47 |
400 | 1 : 1,6 : 3,2 | 14 : 28 | 36 |
450 | 1 : 1,4 : 2,9 | 12 : 25 | 32 |
Составление точной рецептуры «на глаз» невозможно. При строительстве небольшого масштаба, технических или сельскохозяйственных построек изготовление бетонной смеси допустимо, но для возведения жилых помещений, при залитии фундамента и для других технологических операций лучше использовать бетонную смесь, составленную специалистами.
Бетон и цемент: в чем разница?
Бетон и цемент: в чем разница?
Люди часто используют термины «цемент» и «бетон» взаимозаменяемо.
Это похоже на использование слов «мука» и «торт» взаимозаменяемо.
Это не одно и то же.
Цемент, как и мука, является ингредиентом.
Для изготовления бетона смесь портландцемента (10-15%) и вода (15-20%) делают пасту. Затем эту пасту смешивают с заполнителями (65-75%) , такими как песок и гравий или щебень. Когда цемент и вода смешиваются, они затвердевают и связывают заполнители в непроницаемую каменную массу.
Следовательно:
Примечание. Портландцемент — это общий термин для типа цемента, используемого почти во всех видах бетона.
Именно бетон ассоциируется у нас с прочным, долговечным конструкционным строительным материалом, который широко используется в строительстве от мостов до зданий и тротуаров.
Основным связующим компонентом является цемент.
Итак, из чего сделан цемент?
Как мы знаем, цемент является основным ингредиентом, используемым для производства бетона.
Но цемент не является каким-то природным органическим материалом. Он производится путем химической комбинации 8 основных ингредиентов в процессе производства цемента.
8 основных «ингредиентов», присутствующих в цементе:
Известь (оксид кальция или гидроксид кальция) 60-65%, кремний (диоксид кремния) 17-25%, глинозем (оксид алюминия) 3-8 %, магнезия (оксид магния) 1-3%, оксид железа 0,5-6%, сульфат кальция 0,1-0,5%, триоксид серы 1-3%, щелочь 0-1%.
Эти ингредиенты обычно извлекаются из известняка, глины, мергеля, сланца, мела, песка, боксита и железной руды.
Как производится цемент?
Мы познакомим вас с каждым этапом процесса производства цемента, от полезных ископаемых в земле до цементного порошка, который помогает производить бетон.
1. Добыча сырья
Сырье, в основном известняк и глина, добывается из карьеров взрывными работами или бурением с использованием тяжелой горнодобывающей техники.
Сырье перемещается после извлечения, а затем транспортируется к дробилкам самосвалами.
Дробилки способны обрабатывать куски карьерной породы размером с бочку для нефтепродуктов.
Известняковая порода измельчается в первой дробилке, чтобы уменьшить размер породы до максимального размера около 6 дюймов.
Затем он подается во вторую дробилку со смесью глин для уменьшения размера частиц менее 3 дюймов.
Выгруженная сырьевая смесь (известняк 70%, глина 30%) направляется в бункер сырьевой мельницы для последующего измельчения.
Другое сырье, используемое в производстве цемента, называемое добавками, также хранится в отдельных бункерах.
3. Сушка и измельчение
Сырьевая смесь и необходимые добавки подаются из бункеров в сырьевую мельницу через воздуходувки для сушки и измельчения.
Сырьевая мельница состоит из двух камер — камеры сушки и камеры измельчения.
Горячие газы, поступающие из системы подогревателя/печи, поступают в мельницу и высушивают сырьевые материалы перед тем, как они попадут в следующую камеру, которая является камерой измельчения.
Камера измельчения содержит определенное количество шаров различных размеров от 30 мм до 90 мм, которые используются для измельчения материала.
Затем он поступает в сепаратор, который разделяет мелкий и крупный продукт. Последний, называемый браком, направляется на вход мельницы для доизмельчения.
Затем горячий газ и мелкие частицы поступают в многоступенчатый «циклон». Это необходимо для отделения тонкоизмельченных материалов от газов.
Полученная сырьевая мука, состоящая только из очень тонкого сырья, транспортируется в бетонный бункер.
Оттуда извлекаемая из силоса сырьевая мука, которая теперь называется сырьем для печи, подается в верхнюю часть печи подогревателя для спекания.
Система печи предварительного нагрева состоит из многоступенчатого циклонного предварительного нагревателя, камеры сгорания, вертикального канала, вращающейся печи и колосникового охладителя.
В подогревателе сырье для печи подогревается горячим газом, поступающим из камеры сгорания и вращающейся печи. Затем он частично прокаливается в камере сгорания и стояке.
Сырье затем перемещается во вращающуюся печь, где оно перегревается примерно до 1400 C для образования клинкерных компонентов посредством процесса, называемого спеканием.
Тепло вырабатывается при сжигании топлива во вращающейся печи с главной горелкой и в камере сгорания с помощью вытяжных вентиляторов подогревателя или внутрипечных вентиляторов. Для сжигания часто используют уголь, природный газ, мазут и нефтяной кокс.
Агломерация – это когда химические связи сырьевой муки разрушаются под действием тепла, рекомбинируя в новые соединения, образующие вещество, называемое клинкером.
Клинкер выходит из печи в виде очень горячих маленьких темно-серых узелков размером от 1 мм до 25 мм.
Капает на колосниковый охладитель для охлаждения примерно с 1350-1450 C до примерно 120 C за счет использования различных охлаждающих вентиляторов.
Часть горячего воздуха, отбираемого из охладителя, используется в качестве вторичного и третичного воздуха для сжигания во вращающейся печи и камере сгорания соответственно.
Охлажденный клинкер выгружается из охладителя на тарельчатый конвейер и транспортируется на склад клинкера, готовый к транспортировке на цементные мельницы с помощью вентиляторов внутреннего диаметра цементной мельницы.
На цементных заводах клинкер смешивают с другими добавками, необходимыми для производства конкретного вида цемента. Гипс для OPC, известняк для известнякового цемента и шлак для шлакового цемента.
Затем шаровая мельница измельчает корм до мелкого порошка.
Мелкий порошок затем направляется в сепаратор, который разделяет мелкий и крупный продукт. Последняя направляется на вход мельницы на доизмельчение.
Конечный продукт хранится в бетонных силосах как цемент.
Цемент настолько мелкий, что 1 фунт цемента содержит 150 миллиардов зерен.
Цемент готов к транспортировке производителям товарных бетонных смесей для использования в различных строительных проектах.
Наша технология бронированных вентиляторов обеспечивает сверхнадежную работу в процессах подачи цемента при перемещении, перемешивании, нагревании и охлаждении.
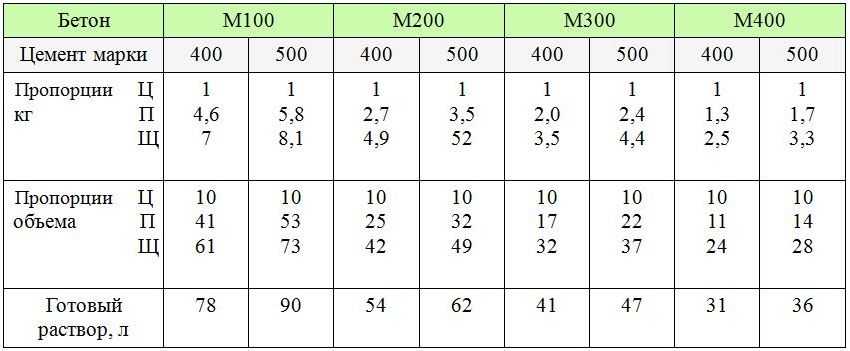
Узнайте, как мы можем повысить энергоэффективность и контролировать выбросы твердых частиц на вашем цементном заводе. Свяжитесь с нами сегодня по телефону
. Если вам понравилась эта статья, воспользуйтесь нашими новыми кнопками социальных сетей, чтобы поделиться ею, и оставьте комментарий ниже.
бетон | Определение, состав, использование, типы и факты
бетон
Все СМИ
- Похожие темы:
- набрызг-бетон железобетон сборный железобетон бетонная оболочка монолитный бетон
Просмотреть весь связанный контент →
Популярные вопросы
Из чего сделан бетон?
Бетон состоит из твердого и химически инертного зернистого вещества, называемого заполнителем (обычно песок и гравий), связанных между собой цементом и водой.
Кто изобрел вяжущее вещество, наиболее часто используемое в современном производстве бетона?
В 1824 году английский изобретатель Джозеф Аспдин сжег и измельчил смесь известняка и глины. Эта смесь, называемая портландцементом, остается доминирующим вяжущим веществом, используемым в производстве бетона.
Какие факторы влияют на прочность бетона?
На прочность бетона влияют факторы окружающей среды, особенно температура и влажность. Если он высохнет преждевременно, он может быть не в состоянии противостоять неравным растягивающим напряжениям. Низкие температуры также могут оказать неблагоприятное воздействие.
Сводка
Прочтите краткий обзор этой темы
бетон , в строительстве, конструкционный материал, состоящий из твердого, химически инертного зернистого вещества, известного как заполнитель (обычно песок и гравий), который связан цементом и водой.
У древних ассирийцев и вавилонян в качестве связующего вещества чаще всего использовалась глина. Египтяне разработали вещество, более похожее на современный бетон, используя в качестве связующих известь и гипс. Известь (оксид кальция), получаемая из известняка, мела или (где это было доступно) раковин устриц, оставалась основным пуццолановым или цементообразующим веществом до начала 1800-х годов. В 1824 году английский изобретатель Джозеф Аспдин сжег и измельчил смесь известняка и глины. Эта смесь, называемая портландцементом, остается доминирующим вяжущим веществом, используемым в производстве бетона.
Викторина «Британника»
Строительные блоки предметов повседневного обихода
Из чего сделаны сигары? К какому материалу относится стекло? Посмотрите, на что вы действительно способны, ответив на вопросы этого теста.
Заполнители обычно классифицируются как мелкие (размером от 0,025 до 6,5 мм [0,001–0,25 дюйма]) или крупные (от 6,5 до 38 мм [0,25–1,5 дюйма] или более). Все заполнители должны быть чистыми и не содержать примесей мягких частиц или растительных веществ, поскольку даже небольшое количество органических соединений почвы приводит к химическим реакциям, серьезно влияющим на прочность бетона.
Бетон характеризуется типом используемого заполнителя или цемента, особыми качествами, которые он проявляет, или методами, используемыми для его производства. В обычном конструкционном бетоне характер бетона во многом определяется водоцементным отношением. Чем ниже содержание воды, при прочих равных условиях, тем прочнее бетон. В смеси должно быть столько воды, чтобы каждая частица заполнителя была полностью окружена цементным тестом, чтобы пространство между заполнителями было заполнено, а бетон был достаточно жидким, чтобы его можно было заливать и эффективно распределять. Еще одним фактором долговечности является количество цемента по отношению к заполнителю (выраженное в виде трехчастного соотношения — цемента к мелкому заполнителю и к крупному заполнителю). Там, где требуется особенно прочный бетон, заполнителя будет относительно меньше.
Прочность бетона измеряется в фунтах на квадратный дюйм или килограммах на квадратный сантиметр силы, необходимой для разрушения образца заданного возраста или твердости. На прочность бетона влияют факторы окружающей среды, особенно температура и влажность. Если дать ему высохнуть преждевременно, он может испытывать неравные растягивающие напряжения, которым в несовершенно затвердевшем состоянии противостоять невозможно. В процессе, известном как отверждение, бетон остается влажным в течение некоторого времени после заливки, чтобы замедлить усадку, возникающую по мере его затвердевания. Низкие температуры также негативно сказываются на его прочности. Чтобы компенсировать это, к цементу примешивают такую добавку, как хлорид кальция. Это ускоряет процесс схватывания, что, в свою очередь, приводит к выделению тепла, достаточного для противодействия умеренно низким температурам. Большие бетонные формы, которые не могут быть надлежащим образом покрыты, не заливают при отрицательных температурах.
Бетон, затвердевший на закладном металле (обычно стали), называется железобетоном или железобетоном. Его изобретение обычно приписывают Жозефу Монье, парижскому садовнику, который делал садовые горшки и кадки из бетона, армированного железной сеткой; он получил патент в 1867 году. Арматурная сталь, которая может иметь форму стержней, стержней или сетки, обеспечивает прочность на растяжение. Обычный бетон плохо выдерживает нагрузки, такие как воздействие ветра, землетрясения, вибрации и другие силы изгиба, и поэтому не подходит для многих конструкционных применений. В железобетоне прочность стали на растяжение и прочность бетона на сжатие делают элемент способным выдерживать тяжелые напряжения всех видов на значительных пролетах. Текучесть бетонной смеси позволяет расположить сталь в точке или вблизи точки, где ожидается наибольшее напряжение.
Оформите подписку Britannica Premium и получите доступ к эксклюзивному контенту. Подпишитесь сейчас
Узнайте, как гидрофобные свойства этого пористого бетона предотвращают его очистку
Посмотреть все видео к этой статье Еще одна инновация в каменном строительстве — использование предварительно напряженного бетона. Это достигается за счет процессов предварительного или постнатяжения. При предварительном натяжении отрезки стальной проволоки, тросов или тросов укладываются в пустую форму, а затем натягиваются и закрепляются. После заливки бетона и его схватывания анкеры освобождаются, и, поскольку сталь стремится вернуться к своей первоначальной длине, она сжимает бетон. В процессе предварительного натяжения сталь пропускается через каналы, сформированные в бетоне.