- Прижимное устройство для строгального станка своими руками – прижим для фуганка
- Приспособления к фуганку
- Как сделать рейсмус своими руками: чертежи самодельного строгального станка
- Прижимы для циркулярки и фрезера. Отвечаю на Вопросы Телезрителей. Перезалив.
- Доработка советского циркулярно фуговального станка — Самодельные станки
- 5 простых способов избежать травм на круглопильном станке
- Мини фуганок из электрорубанка — Master4dom.ru
- Превратите вашу настольную пилу в фуганок: 6 шагов (с изображениями)
- DIY Фуганок от электрического рубанка
- 11 Фрезерных станков для настольной пилы, которые можно легко сделать своими руками
- Как построить кондуктор
- Основы изготовления ящиков типа «ласточкин хвост»
- Введение
- Уровень сложности
- Чистовая
- Время до завершения
- Рекомендуемые инструменты
- Необходимые материалы
- Обрежьте стороны по длине
- Обрезка «ласточкин хвост» и штифтов
- Вырежьте канавки для нижней части ящика
- Начало сборки ящиков
- Присоедините штифты к хвостовикам
- Вставьте нижнюю часть ящика
- Присоедините четвертую сторону ящика с ящиком
- Зажмите ящик
- Отшлифуйте сборку и прикрепите переднюю часть ящика
- Building A 12-дюймовый фуганок
- КАК СОЗДАТЬ ТАБЛИЦУ: Уловки, чтобы сделать это действительно, действительно правильно
Прижимное устройство для строгального станка своими руками – прижим для фуганка
Прижимное устройство для строгального станка своими руками
Виды строгальных станков
Строгальный станок по дереву
Конструкция прижимного механизма напрямую зависит от модели оборудования. Поэтому предварительно необходимо тщательно изучить техническую документацию, особенности элементов станка, их характеристики.
Наиболее распространенный вариант представляет собой силовую установку (электродвигатель), которая приводит в движение цилиндрическую ножевую головку. Ее верхняя часть находится выше уровня опорного стола. Последний может смещаться относительно режущей части в вертикальном направлении. Таким образом регулируется глубина обработки деревянной заготовки. Подобную модель можно сделать своими руками.
Кроме вышеописанного деревообрабатывающего станка для массового производства применяют следующие виды оборудования:
- рейсмусовые с одной режущей головкой;
- циклевальные.
Устанавливаются на линиях по сборке мебели, дверных и оконных конструкций;
- двух, трех и четырехгранные. Обработка происходит сразу в нескольких плоскостях, что повышает производительность;
- модели с несколькими ножами.
Практически все современное оборудование имеет прижимы. Исключение составляют станки, сделанные своими руками или старые модели.
При выборе конструкции фиксатора следует обращать внимание на конфигурацию оборудования. После ее монтажа эксплуатационные и технические качества не должны ухудшиться.
Назначение прижимного устройства для станка
Заводское прижимное устройство
На первый взгляд модификация деревообрабатывающего станка необходима только для фиксации заготовки. Однако при правильном выборе схемы изготовления установленная часть может выполнять ряд других, не менее важных функций.
Во время обработки деревянных изделий можно отрегулировать их фиксацию вручную. В итоге это сказывается на качестве поверхности.
- плавная регулировка уровня фиксации. Осуществляется путем равномерного давления на деталь;
- качество обработки не должно зависеть от длины изделия;
- во время работы элементы оборудования не повреждают деревянную поверхность;
- безопасность. Эксплуатационные качества механизма должны отвечать современным требованиям безопасности труда.
Перед началом проектирования рекомендуется ознакомиться с аналогичными заводскими моделями. Для изготовления прижимного механизма своими руками будут применяться подручные материалы. Поэтому при выборе оптимальной конструкции необходимо руководствоваться принципом целесообразности.
Для фуговального станка специалисты не рекомендуют устанавливать устройство для фиксации. Это может отразиться на качестве изделий.
Самодельный прижим: вариант №1
Самодельное прижимное устройство
Чаще всего для изготовления вышеописанной конструкции за основу берут деталь от старой стиральной машины, а в частности — валики для выжимания влаги. В некоторых случаях после небольшой модификации дополнение можно установить на оборудование.
Рама состоит из четырех опорных лап, которые соединяются между собой П-образным профилем. На нем устанавливаются фиксирующиеся валы. Профили не фиксируются на основании, а свободно передвигаются по ним. В верхней части конструкции находится фиксирующая планка, соединенная с регулировочной ручкой червячной передачей. Для амортизации можно установить пружины, которые будут частично компенсировать сильное давление при обработке неровных поверхностей.
Чертеж прижимного устройства
В составе конструкции следующие компоненты.
- Винт.
- Пластина для соединения.
- Пластина, обеспечивающая надежную фиксацию.
- Опорная стойка.
Для комплектации потребуется 4 штуки.
- Два валика.
- Две боковых опоры для валиков.
- Компенсационные пружины — 2 шт.
- Гайка.
- Фиксирующие оси для валиков.
С помощью верхней ручки происходит регулирование степени прижима. Недостатком подобной модели является большая массивность. Она может подойти не для всех типов станков.
Для уменьшения трудоемкости изготовления механизма для строгального станка можно использовать валики стиральной машины. Предварительно их нужно обрезать.
Самодельный прижим: вариант №2
Альтернативное прижимное устройство
Альтернативным вариантом изготовления прижима для станка своими руками является небольшая модификация оборудования. Она заключается в монтаже по бокам станины двух реек. В основной рабочий вал устанавливаются два подшипника, которые проходит фиксирующая ось.
Сложность может заключаться в конфигурации станины. Все модели имеют ровные края, обеспечивающие монтаж проушин. Регулировка степени зажима осуществляется с помощью пружины. Она смещается по рейкам, тем самым изменяя давление на заготовку.
Элементы конструкции.
- Основной рабочий вал.
- Подшипники.
- Ось с резьбой.
- Гайка.
- Пластины.
- Тяга.
- Пружины.
- Фиксация для пружин.
- Ось эллипса.
- Две пластины.
- Стопор.
- Эллипс.
- Рукоятка.
- Ось.
- Две проушины.
- Уголок.
- Болт для крепления.
Преимуществом этой системы является увеличение производительности труда. При подаче заготовки ее торцевая часть будет упираться в вал, приподнимая его. Это позволит обрабатывать несколько деталей без предварительной регулировки самодельного прижима.
В видеоролике показан пример еще одной конструкции фиксирующего механизма:
Приспособления к фуганку
Работая фуганком, у меня часто были неудачи. Основная из них заключалась в том, как по всей длине доски получить прямую линию. В моем расположении есть новый фуганок. Много времени было потрачено на тщательную настройку ножей, но и это не помогло. Продолжить чтение →
Почему, когда стругает рейсмус, на краях заготовок в конце строгания, получаются поперечные желобки. Причиной этому могут быть погрешности в настройках станка. Большой износ деталей, многие неточности при настройке режущих элементов и зажимных приспособлений. Плохая связка в системе: станок — деталь и другие многочисленные ошибки. Продолжить чтение →
Фуговальные станки по дереву большинство своих проблем могут устранять в основных настройках. Но в некоторых случаях, вы можете столкнуться с проблемой, когда строгальный станок требует более быстрого и кардинального решения. Такое решение параллельные столы. Для того чтобы фуганок работал должным образом, выполняется настройка Продолжить чтение →
Теперь, когда у вас уже есть кусочки доски нарезанные по размеру, следующие шаги, помогают привести грубые, не струганные заготовки до окончательного размера. Для этого будет использовано три инструмента — фуганок, рейсмусный станок и стол с циркулярной пилой. Первый шаг, как правило, Продолжить чтение →
Метки: доска обрезная строганная, доска строганная, обработка деревянной доскиВ каждом большом и красивом проекте обработка древесины начинается с правильного выбора материала из отложенных запасов, а затем путем не хитрых операций и с помощью соответствующих инструментов превращается этот материал в точные детали проекта. Когда речь идет об изделия своими руками, все первичные работы в мастерской начинаются с Продолжить чтение →
Метки: детали, доски, древесины, технология обработки древесиныКак видно из рисунка такое приспособление — фрезер, как фуганок, имеет не так много деталей, чтобы надежно закрепить фрезер и создать работоспособный стол для фуганка.
Стол для ручного фуганка, наверное каждый у кого есть в хозяйстве ручной фуганок, думал, как бы разместить его, для удобства в работе, на небольшом столе. Стол обезопасит приемы работы и более легко поможет остругать деревянный брусок. Лично для меня очень трудно сделать ручным фуганком квадратную рейку, не имея фуговального стола. На самом деле, с приспособлением предложенным ниже я получаю двойной выигрыш потому, что могу использовать его и в качестве рубанка с Продолжить чтение →
Метки: приспособление, стол, упор, Фуганок Одна из первых задач в создании успешного проекта, сделать ровную плоскую и квадратную заготовку.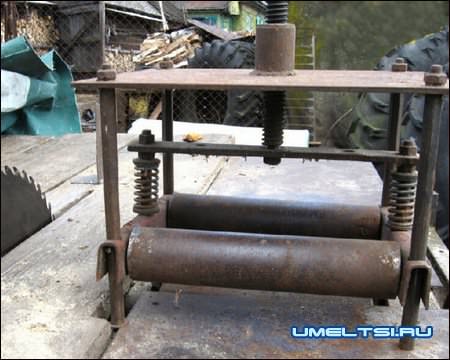
Как делается линейка поверочная ровная и точная. Когда речь идет об инструментах (как и для многих других инструментов в мастерской), точная линейка большая ценность. Приобретение поверочной линейки длиной в 1000-1500 мм, является дорогим предложением. Продолжить чтение →
Метки: измерительная линейка, линейка, поверочная линейка, поверочные линейки, точная линейка, ФуганокВ этой небольшой статье рассмотрим один из важных вопросов установка ножей на фуганок, как с помощью не сложного магнитного приспособления можно точно установить ножи на фуганке. Вам не нужно покупать дорогой прибор и думать потом, как закрепить его на фуговальном станке. Продолжить чтение →
Использую фуганок для выравнивания доски, в конечном итоге, у меня часто получается поверхность шероховатой и появляются сколы. Это занимает много времени в подготовке изделия к отделке. Продолжить чтение →
Как сделать конусный срез фуганком. Суть такого способа в том, чтобы начать строгать определенную часть заготовки. На снимке Продолжить чтение →
Метки: головки, конус, режущей, Строгать, фуганкеСтругаем сужение, другими словами допустим стол, который вы делаете, имеет коническую ногу, то есть она должна сужаться к низу. Я предлагаю делать такого рода работы фуганком. Сначала определяем размер нижней части ноги и наносим разметку, Продолжить чтение →
Метки: доска строганная, коническую, ногу, стол, струганные доски, стругать, фуганкомХорошую способность имеет фуганок, он дает возможность выровнять изогнутую и искривленную древесину. Вот пример крученой и немного кривой деревянной заготовки Продолжить чтение →
Метки: деревянной, древесины, заготовки, кривой, строгании
Существуют разные приспособления и способы остругать деревянные заготовки, которые шире, чем ножи фуганка. Вот один из способов:
Продолжить чтение →
Как сделать рейсмус своими руками: чертежи самодельного строгального станка
В деревообрабатывающем производстве трудно обойтись без современного столярного оборудования, с помощью которого осуществляют обработку бруса, досок, придавая их сторонам идеально ровную поверхность. Для этих целей предназначен строгальный станок, способный справится с большими по площади изделиями.
Изготовленный своими руками рейсмус отличается малым весом, поэтому его легко установить или, убрав за ненадобностью, перевезти в другое место. Он имеет несложную регулировку, прост в эксплуатации и обеспечивает высокое качество обработки поверхностей.
1 Основные моменты изготовления деревообрабатывающего оборудования
На этапе проектирования рейсмусового станка определяют конфигурацию будущего оборудования. В заводских моделях подачу осуществляют верхние ролики, требующие правильной настройки скорости вращения, что проделать в домашних условиях сложно. Самодельные конструкции, напротив, должны быть предельно простыми. Чтобы облегчить процесс их изготовления, отказываются от автоматической подачи заготовки для ее обработки и берут за основу фуганок – еще один вид деревообрабатывающего инструмента.
Кроме этого, следует предусмотреть следующие характеристики будущего строгального станка:
- Возможность изменения положения опорного стола, что необходимо для регулировки его высоты относительно режущего вала.
- Выбор обрабатывающего инструмента. Лучшее решение использовать запчасти от старой фабричной модели, которые обладают требуемыми техническими параметрами.
- Наличие устойчивой рамы. Во время работы оборудования неизбежно появляется вибрация, поэтому для увеличения качества обработки нужно снизить ее воздействие на обрабатываемые заготовки.
Для реализации поставленных задач составляют правильную схему, взяв за основу чертежи заводских моделей, готовые технические решения. Обязательно учитывают опыт изготовления самодельных рейсмусовых станков, а также размеры, толщину, породу древесины обрабатываемых заготовок.
2 Изготовление станины и установка деталей
При наличии необходимого инструмента и материалов сборка рейсмусового оборудования по дереву не займет много времени. Потребуются:
- токарный станок для изготовления валиков, шкивов;
- сверлильный станок или дрель, для проделывания отверстий в крепежных элементах;
- сварочный аппарат для сборки подающего стола, станины;
- болгарка для отрезки, подгонки деталей конструкции под требуемый размер.
Существует много вариантов, как сделать рейсмус своими руками, но оптимальные габариты для самодельного устройства не должны превышать 1х1 метра. Эти параметры позволяют обрабатывать заготовки любых размеров, при этом изделие получается мобильным и его будет удобно переставить, перевезти на другое место. Оборудование располагают таким образом, чтобы обеспечить доступ со всех сторон.
Если планируется стационарное использование, то чтобы исключить в будущем проявление излишней вибрации каркас бетонируют, закрепляют при помощи анкерных болтов.
Первым делом по предварительно составленным чертежам осуществляют сборку станины. Для придания конструкции необходимой жесткости берут железный уголок 50х50 мм, при его отсутствии профильную квадратную трубу 40х40 мм.
Размеченные элементы станины нарезают при помощи болгарки с абразивным кругом. Уложив на ровном месте, их собирают согласно схеме и производят сварку каркаса. Намечают отверстия крепления съемных частей и, используя дрель, просверливают их.
Завершив сварочные работы, приступают к установке валов: ножевого, прижимных, подающего. Для получения изделий высокого качества лучше приобрести ножевой вал целиком в сборе или готовые ножи для рейсмуса. Если есть возможность, прижимные валы делают из ручных выжимателей белья от старых стиральных машинок, прорезиненная поверхность которых мягко, но крепко удержит заготовки на рабочем столе.
Шкивы для мотора, валов предпочтительнее устанавливать шестеренчатые, что позволит использовать цепную передачу, отличающуюся большой степенью надежности. В качестве двигателя выбирают асинхронный электромотор мощностью 4–5 кВт. Принципиальная схема расположения деталей показана на рисунке:
1 – рабочий стол подачи, выдачи заготовки; 2 – древесная заготовка; 3 – предохранительное приспособление; 4 – подающий верхний валик с рифленой поверхностью; 5 – передний прижим; 6 – ножевой вал; 7 – задний прижим; 8 – подающий верхний валик с гладкой поверхностью; 9 – нижний гладкий вал
Основание стола состоит из задней и передней частей, которые закреплены на подготовленных регулировочных устройствах. С помощью них изменяют высоту стола и положение обрабатываемой заготовки. Перед началом работ обязательно проверяют расположение ножей, надежность крепления и правильность заточки.
3 Наладка оборудования
Настройку осуществляют следующим образом. Опорные ролики (8) опускают ниже уровня стола (10), а саму столешницу настолько, чтобы уложенный на нее предварительно обработанный деревянный брусок свободно проходил под ножевым валом. Медленно приподнимают стол, одновременно прокручивая вал, до касания им поверхности бруска. В момент прикосновения верхней гранью ножевого вала фиксируют положения стола.
Опустив рабочую поверхность на 0,3 мм, брусок перемещают под задний прижим (3), который регулируют винтами (2), стараясь получить касание шаблона. Дополнительно опускают на 0,7 мм (итого на 1 мм от начального уровня) и мерный штамп помещают под передний прижим (5), высота которого до момента касания бруска выставляется регулировочными винтами (6).
Опустив рабочую поверхность еще на 0,5 (1,5 мм от начального уровня), настраивают задний прижимной вал (1). Продолжая опускать на 0,5 мм, при помощи мерного шаблона изменяют высоту рифленого подающего вальца (7). Понизив еще на миллиметр, мерный шаблон устанавливают под когтевую защиту и регулируют высоту до момента касания. В завершении опорные ролики выставляют над поверхностью стола.
Обработка заготовки, которая не прижимается одновременно обоими валами, – запрещена!
В зависимости от модели деревообрабатывающего оборудования настроечные размеры могут отличаться. Приступая к обработке хвойных пород, разницу в высоте прижимных валов устанавливают в пределах 0,3 мм, для лиственных – 0,1 мм. Во время строгания заготовок важно соблюдать технику безопасности, поэтому нельзя:
- располагать руки вблизи движущихся и вращающихся механизмов;
- производить чистку во время работы;
- ремонтировать детали, находящиеся под напряжением.
Чтобы предупредить возможность повреждения током оборудование обязательно заземляют. Перед включением обязательно проверяют исправность всех механизмов.
4 Деревообрабатывающий инструмент из электрорубанка
Именно такой вариант изготовления рейсмусового станка в домашних условиях во многих случаях предпочитают умельцы при наличии электрорубанка. Затраты на доработку с сохранением принципа работы будут минимальными, но результат не хуже, чем при использовании дорогостоящего оборудования. Вместо стола устанавливают ровную мощную доску, по ее сторонам ограничители ширины, на которые производят крепление основного узла. Электрический рубанок крепят на основании с изменяющейся высотой.
Заднюю опорную металлическую пластину на рубанке меняют на изготовленную самостоятельно из ОСП, фанеры больших размеров. Толщину выбирают таким образом, чтобы получить одинаковый уровень относительно передней пластины, регулирующей зазор для снятия стружки в 1-3 мм. Ширина рабочего стола и опорной пластины должны быть равными друг другу.
Сбоку пластины прикручивают рейки крепления ножек нужной высоты. Поскольку стандарт ширины ножей 8,2 см, то толщина рубанка обрабатываемых заготовок, например бруса, не должна превышать 10 см, а межосевое расстояние крепления ножек 11–12 см. Следовательно, их длина составит 14–16 см, ширина выше 3,5 см, а толщина – 1 см. Их крепят на одном расстоянии от края пластины.
Предварительно собранное прижимное устройство с электрорубанком устанавливают на рабочем основании, располагая точки крепления строго по уровню. Это нужно для параллельного перемещения относительно рабочей поверхности и гарантирует необходимую точность обработки самодельным станком. Если требуется обеспечить прижим рабочего инструмента, то используют пружинные стяжки, резиновый жгут.
Это самый доступный вариант изготовления рейсмусового станка. Конечно, такой инструмент трудно считать полноценным, но принцип работы и конечный результат делают его пригодным для выполнения несложных операций в домашних условиях.
Прижимы для циркулярки и фрезера. Отвечаю на Вопросы Телезрителей. Перезалив.
Снова отвечаю на вопросы телезрителей.
Краткая предыстория.
Недавно мой коллега Юрий Примаченко выложил видео о использовании веерных (гребенчатых) прижимов на фрезерном станке :
Я, как обычно 🙂 — написал свой комментарий, на который мне задали несколько вопросов:
Приведу всю переписку, чтобы было понятно:
AlfFisher Правильная и полезная тема. Нужно уделять внимание этой теме — постоянно 🙂 Втыкну и свои 5 копеек: гребенка может быть 2х типов — прижимная и противостоящая обратному удару. В первом случае угол больше (45 — 60°) — соответственно ламели имеют больший ход и работают мягче, но почти не предотвращают обратный удар. Во втором случае угол тупее 60 — 75° — ламели прижимают посредственно, из-за малого хода и бОльшей жесткости, но хорошо фиксируют деталь при обратном ударе. И еще один момент: чтобы гребенка не затирала о поверхность, перед тем как прорезать ламели, нужно на фуганке снять 0,5 — 1 мм, с обоих сторон, на длину ламелей.
Свернуть
Ответить · 6
Скрыть ответы
Andrei Molodoi 2 дня назад (изменено)
+AlfFisher Марк, огромная просьба (думаю будет не только моей), сделайте видео про все шаги описанные вами в данном комментарии. Спасибо 😉
Ответить · 2
Sergey Ost 11 часов назад
+AlfFisher Марк, а можно поподробнее? Видео есть?
Я уже размещал несколько видео на данную тему:
В этом я показываю плоские прижимы. Преимущество таких прижимов в малой высоте и мягкости хода. Посмотрите видео, я подробно в нем рассказал обо всех нюансах.
Следующий вариант — веерный (гребенчатый) прижим, установленный на переходной пластине линейки и на столе пилы.
https://www.youtube.com/watch?v=zlwuuO2MjtY
Еще один вариант плоского прижима. Но в этом случае он сделан из металла. Для кронштейна использован металлический уголок 35 х 35, с прорезанным пазом под болт М10.
Вертикальная полка уголка уменьшена по высоте, чтобы сделать кронштейн более компактным и легким.
В качестве пружины в обоих прижимах использована полоса из ленточной пилы толщиной 1,1 мм и шириной 22 и 16 мм соответственно.
Пружина закреплена на 2 заклепки, Ф 3 мм к пластине, приваренной к кронштейну. На краях пружины сделаны 2 отверстия (одно из них — овальное, чтобы край пружины мог двигаться относительно нажимного бруска) Нажимной брусок привинчен к пружине на 2 шурупа.
Нажимной брусок сделан из бука и пропитан расплавленным парафином для уменьшения трения.
Паз в кронштейне под зажимной болт — прорезан отрезным диском (на проход), далее в паз вставлен кусок пластины толщиной 4 мм и паз — замкнут (заварен).
А в этом видео я показываю самодельные болты, которые использую для крепления прижимов и другой оснастки в Т — образных пазах стола циркулярной пилы.
Ну вот, видео я думаю уже посмотрели, а теперь более подробно о гребенчатом прижиме.
Прижимы для своих станков я обычно делаю из прямослойной сосновой, не смолистой доски, толщиной 15 — 25 мм. Ширина доски — в зависимости от задач, колеблется в пределах 50 — 100 мм.
Длина подбирается так, чтобы прижим можно было уверенно зафиксировать на столе или линейке станка.
Поскольку прижимами редко прижимают детали толще 40 и шире 100 мм, соответственно если прижим фиксируется одним болтом — то длина паза под болт составляет 100 — 120 мм.
Как я уже упоминал в своем комментарии выше, от угла, под которым срезана рабочая сторона прижима — зависит то, как он будет работать.
Прижим с острым углом 45°-60° — работает более мягко, и имеет бОльший ход, но плохо противостоит «обратному удару» (когда фреза или пила выбивает заготовку назад).
Прижим с более тупым углом 60°-75° — имеет малый ход (1-2 мм), хорошо противостоит обратному удару, но оказывает большое сопротивление движению детали.
Длина пропилов (ламелей) обычно делается в пределах 50 — 70 мм.
Толщину ламели и ширину пропила следует подбирать так, чтобы ламели легко отклонялись при нажиме пальцем, но не гнулись при нажатии в торец ламели.
Рис. 1 Размеры прижима.
Пропилы можно делать как при помощи лобзика или ленточной пилы, так и на дисковой пиле. Причем если станок позволяет наклонять диск, то проще сделать это на торцовочной каретке, наклонив диск в сторону.
Для этого на каретке укрепляется доска (панель) с направляющей, равной по толщине — пропилу пилы.
Рис.2 Прорезание пазов на каретке.
Но даже если пила не позволяет делать наклонные пропилы, можно обойтись обычной пилой с диском, установленным перпендикулярно столу.
В этом случае длина пропилов с верхней и нижней стороны прижима будет разной, но это практически не оказывает влияния на его работу.
Первую (по ходу детали) ламель можно укоротить на 5 мм, чтобы при обратном ударе деталь ее не сломала. Она не будет участвовать в работе, а будет служить ограничителем хода для второй ламели.
Для того, чтобы прижим работал четко, без заеданий, следует сделать так, чтобы ламели при работе не касались поверхности стола, иначе они будут затирать, и плохо возвращаться назад, после прохода детали.
Это можно сделать 2 способами: либо наклеить на готовый прижим кусок плотного картона или ДВП толщиной 2,5 — 3 мм,
либо перед тем, как нарезать пазы, снять с той стороны, которая будет прилегать к столу или линейке 1 — 2 мм, используя для этого пилу или фуганок.
Можно снять материал с обоих сторон, тогда прижим станет универсальным и его можно будет ставить и на стол и на линейку.
Рис. 2 Занижение профиля ламелей (накладкой из ДВП или снятием материала)
Думаю «тема раскрыта» 🙂
Если остались вопросы — пишите, постараюсь доходчиво объяснить 🙂
На этом на сегодня — все. Подписывайтесь на обновления блога, пишите комментарии и делитесь в соцсетях :).
Доработка советского циркулярно фуговального станка — Самодельные станки
Витя, автор сказал в 1 посте что нужно «для мебели и игрушек»
Во-первых, сильно подозреваю, рейками не ограничится…
А в главных, рейсмус с ручной подачей — это при любых калибрах плохая идея.
Фуганок, в случае чего, просто отбрасывает заготовку вверх и назад.
Рейсмус, в случае того же чего, разгоняет ту рейку на всю длину и превращает в стрелу баллисты…
Противооткаты, конечно, хорошо, но не панацея.
Впрочем, ему решать.
Практика показывает, что убеждать слишком долго бесперспективно.
Мне просто интересен ход мысли что 1 мм съема при условии что строжет с двух сторон это цинично.
Почему с двух?
Речь шла о 1-3мм с одной стороны.
Может, и есть рейсмусы с такими съемами, но бытовые явно не из той категории.
Да и смысла нет, как я писал, рейсмус — получистовой станок.
Шкуркой тоже не надо.
Если нужно снять 1мм, то 0,8 — рубанком/фуганком, хоть ручным, хоть механическим , остальное — в зависимости от нужного результата. можно и шкуркой.
Поскольку у меня есть рейсмус, но нет фуганка, я снимал примерно по 0,5мм за проход до нужной толщины.
Узкие стороны — ручным рубанком.
При необходимости доводил шлифмашинкой и вручную шкурками.
Я понимаю, что удовольствие недешевое, но экономить с риском остаться в лучшем случае без рук… хотя, как ни цинично звучит, возможно, это не лучший случай по нашим временам…
Есть еще всякие авиты и аналоги — поискать б/у и привести в порядок — результат будет в любом случае лучше и безопаснее.
5 простых способов избежать травм на круглопильном станке
Самые распространенные травмы при работе на круглопильном станке возникают в результате «обратного вылета» заготовки. Сейчас мы расскажем о том, как это происходит и как избежать возникновения подобных ситуаций.
«Береги руку, Сеня!» (с) Геннадий Петрович Козодоев
В большинстве столярных цехов круглопильный станок занимает одно из центральных мест. Круглопильные станки или, как их часто называют, циркулярки — это то без чего не обойдется ни один деревообработчик выполняя свои проекты. Но в то же время это один самых опасных станков в цеху. Зачастую циркулярки эксплуатируются с нарушением норм техники безопасности: отсутствие кожуха защиты пильного диска, проталкивание заготовок без использования автоподатчиков и специальных толкателей, должным образом не настроенный пильный узел и параллельные упоры. В следствии этого периодически происходит обратный вылет заготовки. Не редко можно услышать от бывалых и новоиспеченных столяров: «Выбило заготовку, чуть не убило. Просвистела как пуля возле виска. Пролетела через весь цех!»
Обратный вылет заготовки — это тот случай, когда заготовка внезапно вылетает в сторону оператора на высокой скорости. При этом возникают два самых распространенных типа травм:
- Поражение грудной клетки или головы летящей заготовкой. Хорошо если удастся отделаться легким ушибом или синяком
- Травмы кисти или фаланг пальцев из за попадания в зону вращения режущего инструмента. Человек не успевает среагировать на отдачу и конечность по инерции попадает на пильный диск. Рваные раны, раздробление костей, отрезанные фаланги — вот печальный итог преступной беспечности
Печальный итог преступной беспечности
Рваные раны, раздробление костей, отрезанные фаланги. Оно вам надо?
Еще три есть. Жить можно
Предупрежден, значит вооружен
Вылет заготовки происходит в нескольких случаях. Во-первых, когда недостаточно усилие прижима заготовки к параллельному упору. Во-вторых когда заготовка изменяет положение относительно пильного диска. В обоих случаях часть заготовки попадает на заднюю часть пилы и стремительно вылетает в сторону вращения диска, то есть именно в вашу сторону.
Давайте рассмотри несколько простых способов избежать выбивания заготовки и закончить рабочий день целым и невредимым.
1. Используйте расклинивающий нож
Расклинивающий нож — это металлическая пластина, установленная в плоскости пильного диска с целью предотвращения заклинивания задней части пильного диска в распиливаемом материале в следствии внутренних напряжений древесины или при смещении заготовки от оси пильного диска. Как правильно толщина расклинивающего ножа равна толщине зубьев дисковой пилы или незначительно больше.
Расклинивающий нож
2. Используйте вставку-разделитель
Обязательно используйте вставку из фанеры, дерева или пластика. Она устанавливает на одном уровне с рабочим столом круглопильного станка и служит для минимизации расстояния от тела пильного диска. Таким образом ни заготовка, ни обрезки не будут затянуты пилой ниже уровня стола и не произойдет выброса детали в сторону оператора
Вкладка из мягкого пластика
3.
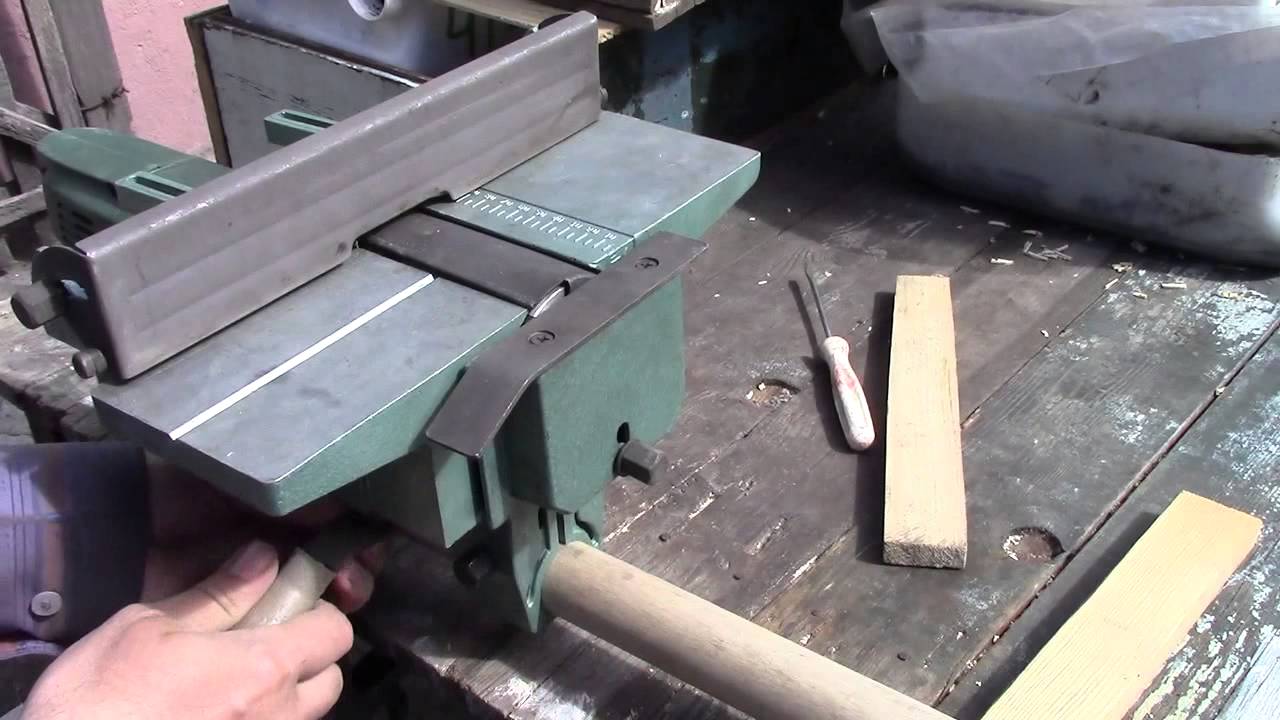
Еще один способ избежать обратного вылета заготовки — это использование приспособлений для поперечного реза или торцовочных кареток. Это позволит вам зафиксировать заготовку прижимами при необходимости. Также ваши руки будут на безопасном расстоянии от пильного диска. Ну и последний бонус это всегда качественный и ровный пропил без риска смещения заготовки относительно оси пилы. Вы легко можете сами изготовить это приспособление. а большинство станков оснащено столами с «Т» пазами для направляющих
Потратьте всего 2 часа на изготовление каретки
4. Не начинайте работать без толкателя
Вы просто обязаны использовать толкатель для осуществления резов. Это недорогое и простое приспособление уменьшит риск возникновения неприятных ситуаций во время работы.
Что может быть проще?
5. Установите на своем станке кожух ограждения пильного диска
Вы будете удивлены, но защитный кожух это не лишняя деталь, которая непонятным образом оказалось в комплекте поставки вашего станка. Прямо сейчас вспомните куда вы его выкинули, найдите и установите на свой станок! Использование этой «Ненужной штуки» позволит вам в дальнейшем играть на гитаре и на пианино, а так же набивать комменты к этому посту всеми пальцами))
Надеемся, вы возьмете на вооружение эти не хитрые советы. А впрочем, вы и так все это знали, но боялись использовать на практике.
Делитесь этим постом с друзьями в социальных сетях!
Мини фуганок из электрорубанка — Master4dom.ru
Операции по строганию или фугованию деревянных заготовок одни из самых частых и трудозатратных операций, отнимающих много времени и сил. Конечно имея соответствующий бюджет можно приобрести профессиональные станки, но как быть начинающему мастеру с ограниченным бюджетом. Не строгать же всё вручную. Выходом из этой ситуации может послужить мини фуганок, сделанный своими руками из электрорубанка. Ширина строгания получится не особо большой – около 80 мм, но для начала вполне неплохо.
Основную часть деталей для мини фуганка я сделал из фанеры толщиной 18 мм. Чтобы облегчить себе работу и не сооружать основание решил закрепить мини фуганок на торце распиловочного стола.
Для начала распилил фанеру на четыре заготовки как на рисунке ниже. Размеры деталей выбирал исходя из размеров электрорубанка и стола на который все это будет крепиться.
На двух прямоугольных заготовках выпилил профиль для установки электрорубанка так, чтобы ножи доставали до края столешницы. После этого зашлифовал поверхности и снял фаску с углов. Собрал всю конструкцию на конфирматы. Для защиты от влаги покрыл маслом для садовой мебели
Для того, чтобы кнопка включения электрорубанка была всегда нажата и сам электрорубанок был надежнее прижат к столу выпилил из бруска вкладыш под ручку.
После того, как масло высохло закрепил конструкцию на торце распиловочного стола так, чтобы она являлась продолжением стола.
Для фиксации самого рубака пришлось изготовить еще дополнительно две детали. Одна устанавливается на основание для компенсации зазора между ручкой и основанием, вторая устанавливается сверху ручки и прижимает электрорубанок к основанию.
После установки электрорубанка с вкладышем и двумя выше описанными деталями на основание просверлил отверстие 8 мм через детали,вкладыш и основание затем стянул все детали болтом М8.
При таком стягивании деталей невозможно добиться угла 900 между поверхностью стола и ножами электрорубанка, поэтому я просверлил отверстие 6 мм в основании напротив ручки электрорубанка забил в это отверстие мебельную забивную гайку и закрутил в нее болт М6 уперев его в ручку электрорубанка и с его помощью отрегулировал угол. Снизу закрутил контргайку для того, чтобы угол оставался постоянным во время работы.
Следующий этап — это изготовление прижима и защиты на ножи электрорубанка. Для прижима взял две рейки и закрепил между ними два отрезка пластиковой канализационной трубы. Сам прижим закрепил на параллельном упоре распиловочного стола.
Защиту на ножи электрорубанка изготовил из той же фанеры. Выпилил прямоугольную деталь, скруглил угол с приемной стороны и закрепил ее на электрорубанке через мебельный уголок и пружину на стационарное место крепления ограничителя глубины.
Мини фуганок готов к работе!
Превратите вашу настольную пилу в фуганок: 6 шагов (с изображениями)
Есть некоторые инструменты, которые трудно найти, либо они слишком дороги, их трудно найти, либо они просто не так распространены для домашних мастеров. Я обнаружил, что фуганки входят в число таких инструментов.
К счастью, есть простой способ превратить вашу столовую пилу в фуганок (шириной всего 2,75 дюйма, но тем не менее: фуганок). Это включает в себя изготовление приспособления, которое зажимается на неровной доске, обеспечивая при этом хороший прямой край проехать к забору и произвести на доске единственную прямую кромку.Потом; Вы можете использовать столовую пилу, как обычно, для изготовления доски с 2 или 4 квадратными кромками.
Он также работает как зажимное приспособление для конуса; хотя это не особенно точно, если вы пытаетесь повторить конус на нескольких частях.
Это приспособление основано на широко распространенном / доступном приспособлении, но самая большая разница между моим приспособлением и другими — это использование регулируемых зажимов для стержней. Зажимы, используемые в других приспособлениях, не обладают большой гибкостью по высоте, менее дорогие не регулируются самостоятельно и, независимо от типа, по-прежнему дороги.Посмотрите джигу Стива Рэмси на сайте Woodworking For Mere Mortals, чтобы посмотреть хорошее видео с этим типом приспособления.
НЕОБХОДИМЫЙ ИНСТРУМЕНТ:
- Столовая пила
- Сверлильный пресс и насадки
- Отвертка
- Ключи (2)
- Зажимы
- Зенковка
- Ножовка по металлу
НЕОБХОДИМЫЕ МАТЕРИАЛЫ:
- Зажим на 2 прутка Максимум 12 дюймов в длину (Найдите несколько дешевых: мои стоили всего 7 долларов каждая.
Я искал несколько длинных 6 дюймов, но 12 дюймов были такими же короткими, как и они.)
- Разное. Винты
- Клей для дерева
- Кусок фанеры с заводской кромкой, длиной не менее 24 дюймов
- Кусок более тонкой, но прочной фанеры; 3/8 дюйма (На фотографиях я использовал ДВП, но он был слишком гибким; поэтому я заменил он со слоем 3/8 дюйма.
- 2 блока из твердой древесины (я использовал клен). У меня примерно 3x3x2 дюйма, но размер будет зависеть от размера зажимов для стержня.
- 2 болта, гайки, стопорные шайбы и 4 обычные шайбы
DIY Фуганок от электрического рубанка
Эта сборка ожила, потому что я не использовал электрический рубанок, который у меня лежал, и мне было полезно иметь фуганок.Оказывается, я должен был проверить машину перед тем, как начать…
Дизайн
Вдохновение пришло из нескольких сборок, которые я видел в прошлом на YouTube, за которыми я следую. Вот один из каналов «Дарбин Орвар», который похож на то, что я создал:
youtube.com/embed/u4QIaEqfUgE?feature=oembed» frameborder=»0″ allow=»accelerometer; autoplay; encrypted-media; gyroscope; picture-in-picture» allowfullscreen=»»/>
Идея состоит в том, чтобы повернуть строгальный станок на 180 градусов и использовать его как фуганок, добавив к нему забор. В целях безопасности над лезвиями следует добавить крышку. Я так и не добрался до этой стадии с моей сборкой, потому что машина умерла во время сборки.
Также приятно иметь регулируемый упор и другие параметры точной настройки для точных резов. Если вы ищете что-то подобное, я предлагаю посмотреть видео из «Get Hands Dirty» Криса.
Сборка
База
Поскольку все машины разные, я не искал и не делал никаких планов / 3D-моделей для этой сборки. Я начал с лепки обрезка для поддержки ручки. Как только эта деталь могла удерживать ее в вертикальном положении, я мог зажать ее, прикрутив куски дерева с обеих сторон.Этот зажим достигается за счет того, что средняя часть немного уже ручки. Получив эти кусочки, я смог заполнить оставшийся промежуток между полосами сбоку.
Забор
После того, как у меня было основание, я начал работать над забором. Это деталь, которая образует угол 90 градусов с лезвиями и поддерживает вашу заготовку, когда вы проталкиваете ее поверх лезвий.Для этой детали я обвел часть сбоку машины и вырезал эту форму из одного куска фанеры. Таким образом, я мог надеть кусок фанеры на машину, чтобы сделать забор, а также для дальнейшей поддержки машины. Получив это, я добавил распорку к основанию и к верхней части забора, чтобы получился идеальный угол в 90 градусов. Для дополнительной поддержки забора я добавил к нему несколько металлических скоб.
После этого настало время для пробного запуска. Вначале все шло отлично, по дереву проблем не было, и результат выглядел довольно неплохо.Однако от второго куска дерева, который я попробовал, от машины исходил странный запах и соответствующий звук отказа. Машина умерла на мне. Не уверен, какая часть вышла из строя, но я знаю одно; он больше не работает. Поэтому, к сожалению, мне пришлось остановить сборку здесь.
Результат
Результат этой сборки неутешителен из-за того, что я не успел ее закончить. Моя машина решила, что пришло время ее заменить, поэтому я, вероятно, просто собираюсь сэкономить на настольном фуганке, вместо того, чтобы пытаться построить еще один самодельный.Однако тестовый запуск прошел нормально, так что концепция этой сборки работает! Поэтому я решил закончить видео и написать эту статью. Надеюсь, это кому-нибудь поможет.
Окончательный результат проекта фуганка «Сделай сам»Ссылки
Если вы хотите получить больше вдохновения от моей сборки, ознакомьтесь с этими сообщениями.
Instagram 1 | 2
Надеюсь, этот пост вдохновил вас на что-нибудь!
И не забывайте следить за своим энтузиазмом.
11 Фрезерных станков для настольной пилы, которые можно легко сделать своими руками
Для большинства деревообрабатывающих задач нам требуются идеально ровные и однородные доски, но, к сожалению, доски в таком состоянии редко приходят прямо из магазина.
Если у вас есть деформированная или погнутая древесина, подходящим инструментом для ее исправления является фуганок. Тем не менее, для большинства мастеров по дереву на дому иметь такую непрактично, но это не проблема.
Если у вас есть настольная пила — от самой большой настольной пилы до более мобильной настольной пилы для стройплощадок — вы тоже можете использовать ее, так что вот 11 фуговальных приспособлений для настольной пилы, которые вы легко можете сделать своими руками.
Это история, с которой будут знакомы многие плотники: вы проводите много времени, рыясь через груды дерева, пытаясь найти нужный кусок инвентаря, но когда вы приносите его домой, вы обнаруживаете, что его все еще нет идеально ровный.
В этой ситуации идеально подошел бы фуганок, но эти громоздкие и дорогие станки часто недоступны для обычного домашнего пользователя. Если вы когда-либо сталкивались с подобным опытом, этот план по созданию приспособления, который позволит вам превратить вашу настольную пилу в импровизированный фуганок, может быть другим вариантом.
План довольно длинный и подробный, но все он очень хорошо объяснен, и есть несколько полезных фотографий, которые помогут вам сделать это правильно. Мы также ценим раздел с инструкциями в конце, в котором рассказывается, как его использовать после завершения сборки.
В целом, этот план — очень полезный ресурс, если вам нужен фуганок, но у вас нет денег или места для выделенного станка.
Когда дело доходит до планов DIY, которые вы можете попробовать дома, одним из наших любимых сайтов является Instructables. Там вы можете найти планы практически всего, что вы хотите собрать, — и именно здесь мы нашли этот отличный план фуганка для настольной пилы.
Следуя обычному формату Instructables, сначала вам дается введение в продукт, а затем список материалов, которые потребуются.После этого пошаговый план покажет вам, как построить приспособление, с четкими объяснениями и полезными фотографиями, чтобы проиллюстрировать, что вам следует делать.
Нам нравится, как этот план разбивает его на очень простую работу — для выполнения этого приспособления требуется всего шесть шагов. Если вам нужен фуговальный приспособление для настольной пилы, но вы беспокоитесь о чем-то слишком сложном, этот план должен вам понравиться.
Одна из причин, по которой вам нужна идеально ровная кромка на вашей ложи, заключается в том, что она делает все намного проще и точнее, когда дело доходит до пропускания через настольную пилу.Опять же, большинство обычных плотников не захотят тратить деньги, необходимые для покупки специального фуганка, а также могут не иметь места для его хранения — так что вот еще один план для настольной пилы.
В этом плане есть все, что вам нужно, включая некоторые подробные инструкции, а также несколько полезных изображений. Нам также нравится часть в конце о том, как увеличить масштаб, если вам нужно что-то большее. Еще один хорошо составленный план, который получает наше одобрение.
Хотя большинство домашних плотников, вероятно, не владеют фуганком, как объясняется в этом плане, даже если вам повезло, что он есть в вашей мастерской, бывают случаи, когда использование настольной пилы с фуговальным приспособлением все же предпочтительнее.Например, если вы не хотите слишком сильно нагружать свой фуговальный нож чем-то вроде фанеры, отличной альтернативой станет настольная пила.
Нам понравился этот план, потому что он сводит к минимуму многословные объяснения. Вместо этого у вас есть множество картинок, показывающих, что нужно делать, и только краткие инструкции, которые позволят вам следить за происходящим. Если вам нужен план для фуговального приспособления, от которого у вас не будет головной боли, пытаясь понять, как это сделать, это может быть именно то, что вам нужно.
5.Легко изготавливать фуговальный станок для настольной пилы
Как объясняет этот докладчик, наличие набора различных приспособлений действительно может добавить еще один уровень универсальности вашей настольной пиле, и простой фуганок, который он демонстрирует, является прекрасным примером. этого.
Хотя он признает, что он может не обеспечивать такое же качество работы, как настоящий фуганок, он все же может помочь в большом количестве деревообрабатывающих приложений. Он также идеально подходит при работе с вторичной древесиной, которая может в конечном итоге повредить ваше фуговальное полотно — поскольку полотна настольной пилы жестче, дешевле и их легче заменить.
Мы считаем, что это видео обеспечивает правильный баланс между объяснением и демонстрацией. Ведущий говорит вам то, что вам нужно знать, но когда вам легче показать, он просто справляется с этим. Хорошее видео, которое стоит посмотреть.
6. Сани для фуганка
Если вы хотите построить фуганок, но у вас нет времени на просмотр длинных видеороликов на YouTube продолжительностью менее шести минут, это краткое предложение может быть подходящим. из того, что вы предпочитаете.
Столяр на видео проведет вас через каждый шаг, демонстрируя, что вам нужно делать, и объясняя, почему вам нужно это делать, по ходу дела.
Нам очень понравилось смотреть участок, где он устанавливает зажимы в неправильном положении. По его словам, все делают ошибки, особенно когда они пытаются работать слишком быстро, но, по крайней мере, он честен и показывает вам, как это исправить.
Это хорошее видео, которое покажет вам, как сделать необходимое приспособление, но которое также может научить вас нескольким советам и приемам работы с деревом на этом пути.Это делает часы интересными.
Для тех, кто ищет способы соединения древесины без использования фуганка, этот план и видео предлагают два метода: один с помощью настольной пилы, а другой с помощью фрезерного станка. Поскольку нас здесь в основном интересуют настольные пилы, мы продолжим говорить об этом, но если у вас дома есть маршрутизатор, вам может быть интересно проверить и эту часть.
Один из ключей к изготовлению фуговального станка для настольной пилы — это использование очень высококачественного продольного полотна, как объясняет ведущий.Чтобы сделать это приспособление, вам нужно будет смастерить сани, которые он использует — инструкции для этого тоже есть.
Как видите, это простое, но эффективное решение для соединения древесины — и у вас может возникнуть соблазн повторить его дома.
8. Шаблон для стыковки кромок на настольной пиле
В этом видео харизматичный ведущий объясняет, что вы можете сделать фуганок на фрезере или настольной пиле, но для особенно деформированных или неровных деталей из дерева, настольная пила, вероятно, будет лучшим вариантом.
Важным аргументом в пользу этого плана является то, что это чрезвычайно быстрое и простое решение. Видео длится немногим более двух минут, и в нем есть все, что вам нужно, чтобы собрать полезную и функциональную сборку. Никакой ерунды, просто приступим к работе!
Этот план начинается с небольшой предыстории о том, почему мы должны страдать от деформации древесины при покупке у поставщика, прежде чем говорить о том, почему инвестирование в настоящий фуганок не обязательно является лучшим решением.
Далее в плане объясняется, как сделать простой, но эффективный кондуктор для настольной пилы, чтобы вам больше не приходилось беспокоиться о покупке деформированных досок.
Нам нравится логическая структура этого плана вместе с методическими пошаговыми инструкциями. Это еще один план, который чрезвычайно легко понять и следовать, что делает его идеальным вариантом как для опытных мастеров по дереву, так и для новичков в домашних условиях.
Если вы хотите улучшить свои общие навыки деревообработки, а также научиться делать кондуктор, это должно вас заинтересовать. Здесь вам предложат пять различных методов создания плоских досок без использования фуганка.
Хорошо, на самом деле это не планы, и не все трюки используют настольные пилы, но мы хотели включить его в наш список, потому что мы сочли полезным изучить некоторые альтернативные способы производства однородных досок с использованием различных простых методов, которые большинство людей смогут трудоустроиться.
11. Приспособление для фрезерования настольной пилы своими руками
Изготовление этого приспособления может занять немного больше времени, чем некоторые другие — по крайней мере, пару часов, по оценке автора, — но результаты выглядят так они того стоят.
Большая часть плана представлена в виде видео с коротким письменным введением, что делает его идеальным вариантом для людей, которые не любят ломать голову над страницами текста.
Видео живое и не слишком длинное, что делает его еще одним отличным ресурсом, если вы хотите добавить возможность соединения древесины в свой репертуар настольной пилы.
Сэкономьте деньги и место на фуговальном станке, построив фуговальный станок для настольной пилы
Большинство настольных пил поставляются с упором для настольной пилы и угловым калибром для настольной пилы , чтобы начать работу — но как столяр в пункте 5, упомянутом в пункте 5, с правильными приспособлениями настольные пилы могут стать гораздо более универсальным инструментом.
Если вам нужен фуганок, но у вас нет денег или места для его установки, вы можете построить один из шаблонов по этим чертежам и запустить настольную пилу в эксплуатацию, чтобы создать идеально плоские и однородные доски, которые вам нужны.
Не забудьте закрепить!
Как построить кондуктор
Многие проекты прекрасной мебели требуют конических ножек. Несмотря на то, что существует множество методов, которые можно применить для создания этого классического дизайна, самый простой способ — это использовать для настольной пилы приспособление для сужения конуса.Конусное приспособление позволяет вам регулировать конические пропилы практически под любым углом до 15 градусов и дает вам возможность делать это постоянно. Кроме того, приспособление для сужения конуса — это очень быстрый и простой инструмент, который вы найдете полезным для множества проектов.
Материалы
- 6 подножие сосны, тополя или любой другой основной доски (1 на 3 дюйма или 1 на 4 дюйма)
- 1 шарнир (2 дюйма на 3/4 дюйма)
- 2 болты с квадратным подголовком (5 дюймов на 1/4 дюйма)
- 2 плоские шайбы (1/4 дюйма)
- 1 стопорная шайба (1/4 дюйма)
- 1 барашковая гайка (1/4 дюйма)
- 1 контргайка (1/4 дюйма)
- Винты деки (1 1/4 дюйма)
Вырежьте 2 куска дерева
Сначала отмерьте и отрежьте два одинаковых куска дерева, которые будут составлять две стороны приспособления для сужения.
Ель / Крис БейлорСтандартная длина каждой доски — 30 дюймов. Но вы можете отрегулировать длину, если хотите, чтобы приспособление было короче или длиннее для конкретного проекта. Просто убедитесь, что обе доски одинаковой длины.
Присоедините петлю
Сложите две обрезанные доски одна на другую. Затем прикрепите петлю к одному концу досок. Убедитесь, что петля параллельна доскам и отцентрирована прямо посередине двух из них.
Ель / Крис БейлорПросверливание отверстий под болты с квадратным подголовком
Просверлите отверстие в верхней части каждой боковой доски на противоположном конце от петли, как показано на изображении ниже.Отверстия должны быть на дюйм выше каждой боковой панели и быть достаточно большими, чтобы болты с квадратным подголовком диаметром 1/4 дюйма могли плотно пройти через них. Затем просверлите отверстия в нижней части каждой боковой панели. Убедитесь, что отверстия достаточно глубоки, чтобы головки кареточных болтов не выступали из нижней части приспособления.
Ель / Крис БейлорВставьте болты
Вставьте болты с квадратным подголовком в отверстия и вставьте их на место. Убедитесь, что головки болтов находятся ниже поверхности дерева.
Ель / Крис БейлорСборка кронштейна разбрасывателя
Конусное приспособление удерживается под соответствующим углом с помощью распорного кронштейна. Чтобы начать сборку этого кронштейна распределителя, отрежьте кусок дерева шириной 2 дюйма и длиной 8 дюймов. Скруглите края лобзиком, как показано на рисунке ниже.
Затем нарисуйте карандашом линию по длинной оси доски по центральной линии, которая должна быть на расстоянии 1 дюйма с каждой стороны. Затем с помощью дрели проделайте три отверстия диаметром 1/4 дюйма: одно отверстие на расстоянии 1/2 дюйма от каждого края на центральной линии и третье отверстие на расстоянии 1 дюйма от одного края также на центральной линии.
Ель / Крис БейлорВырежьте прорезь в кронштейне распределителя
Используя карандаш и линейку, проведите линию от верхнего края центрального отверстия в кронштейне расширителя до верхнего края наиболее удаленного отверстия (на противоположном крае кронштейна).
Затем проведите параллельную линию между нижними краями этих двух отверстий.
Затем с помощью лобзика вырежьте по этим двум линиям, чтобы создать прорезь в кронштейне сужающегося кондуктора.
Ель / Крис БейлорПрикрепите губку
Отрежьте кусок дерева шириной 2 дюйма.Используя дрель и пару шурупов, прикрепите эту деталь к левой стороне приспособления на расстоянии 1 дюйма от края доски. Эту деталь можно расположить ровно или встык напротив левого края (как показано на изображении ниже). Эта кромка фактически проталкивает суживаемую доску через полотно пилы.
Ель / Крис БейлорПрикрепите кронштейн
Чтобы завершить сборку зажимного приспособления, прикрепите кронштейн расширителя к зажимному приспособлению.
Расположите прорезь кронштейна расширителя над левым болтом с квадратным подголовком, а отверстие — над правым болтом с квадратным подголовком.Постучите по кронштейну, чтобы он встал на место.
Затем установите плоскую шайбу и стопорный болт на правый болт с квадратным подголовком. Затягивайте до тех пор, пока кронштейн не будет плотно прилегать, но не настолько, чтобы он не вращался на болте.
Теперь вы сможете продвигать левый болт через прорезь, расширяя и сужая зажимное приспособление. Если вас устраивает свобода перемещения зажимного приспособления, прикрепите плоскую шайбу к левому болту с квадратным подголовком, затем стопорную шайбу и затем барашковую гайку для фиксации.
Ель / Крис БейлорИспользуйте свой кондуктор
Чтобы использовать приспособление для сужения конуса, отрегулируйте угол приспособления и затяните барашковую гайку.Расположите доску, которая будет сужаться, плотно прилегая к левой стороне приспособления так, чтобы конец доски был напротив выступа на нижнем конце приспособления (как показано на изображении ниже).
Затем поместите правую сторону приспособления напротив упора настольной пилы. Отрегулируйте положение вашего забора так, чтобы вы срезали конус желаемой ширины.
Прижмите доску к приспособлению, а приспособление — к ограждению. Проденьте весь аппарат через пильный диск. У вас должна получиться ровная доска с чисто конусом.
Ель / Крис Бейлор
Основы изготовления ящиков типа «ласточкин хвост»
Введение
Один из самых фундаментальных навыков краснодеревщика или изящной мебели — создание ящиков типа «ласточкин хвост». Хорошо построенный ящик типа «ласточкин хвост» не только невероятно прочен и долговечен, но и красив с эстетической точки зрения. Один из способов определить уровень квалификации плотника — это проверить и увидеть, насколько хорошо они строят ящики типа «ласточкин хвост» в своих проектах.
В этой статье мы шаг за шагом проведем вас через процесс создания ящиков типа «ласточкин хвост».Как только вы поймете основы, вы сможете последовательно изготавливать красивые ящики типа «ласточкин хвост» для своих деревообрабатывающих проектов. Некоторые из тех же навыков можно использовать и для соединений типа «ласточкин хвост», используемых и в других областях.
Уровень сложности
Чистовая
- Краска или морилка и полиуретан
Время до завершения
Рекомендуемые инструменты
- Торцовочная пила или циркулярная пила
- Фрезерно-фрезерный стол с прямой фрезой 1/4 «
- Приставка и фреза «ласточкин хвост»
- Средства защиты глаз и органов слуха
Необходимые материалы
- Тополь или сосна 1 x 4 для боковин ящиков
- Фанера толщиной 1/4 «для дна ящика
- Приклад 1 x 6 для передней части ящика
- Ручки для ящиков
- Рулетка
- Карандаш
- Клей столярный
- Шурупы для дерева 1 дюйм
- Краска или морилка любого цвета по выбору
- Наждачная бумага
Обрежьте стороны по длине
Первый шаг — отрезать ящик с четырех сторон до нужной длины.Выдвижные ящики обычно изготавливаются из 1x запаса, но ширина может зависеть от высоты необходимого ящика.
- Распилите заготовку циркулярной пилой или настольной пилой до желаемой ширины.
- Затем отрежьте четыре стороны до готовой длины в соответствии с планом проекта. Две стороны ящика должны быть одинаковой длины, а передняя и задняя — одинаковой длины. Например, для ящика, который будет иметь размер готовой коробки 18 дюймов в ширину и 12 дюймов в глубину, вам нужно будет вырезать две части длиной 18 дюймов и две части 12 дюймов.
Обрезка «ласточкин хвост» и штифтов
Как только стороны ящика будут обрезаны до нужной длины, мы обратим наше внимание на обрезку ласточкин хвоста. В то время как традиционные «ласточкин хвост» обрезаются вручную пилой и долотом, мы собираемся использовать зажимное приспособление и фрезер.
- СОВЕТ: Обязательно следуйте пошаговым инструкциям, прилагаемым к вашему зажимному приспособлению «ласточкин хвост», чтобы идеально подогнать «ласточкин хвост», поскольку каждый зажим «ласточкин хвост» имеет свой набор шагов для отрезания хвостов и штифтов.
По этой причине следующие указания являются общими инструкциями; ваш фактический процесс будет немного отличаться в зависимости от вашего приспособления.
- Для достижения наилучших результатов всегда сначала обрезайте хвосты — центральную часть сустава, имеющую форму рыбьего хвоста. Намного легче снять с штифтов немного больше, чем отрегулировать хвосты. Установите приспособление «ласточкин хвост» для обрезки хвостов и поместите конец одной из двух боковых частей в приспособление. Отцентрируйте приспособление соответствующим образом и обрежьте хвосты, снова следуя инструкциям, прилагаемым к вашему приспособлению «ласточкин хвост»).
- После того, как первый хвост был отрезан, поверните приклад на 180 градусов и поместите противоположную сторону в приспособление. Убедитесь, что сторона доски, которая была обращена к вам, когда вы разрезали первый набор хвостов, совпадает с той стороной доски, которая обращена к вам сейчас.
- Когда вы закончите обрезать хвосты на обоих концах одной боковой детали, завершите противоположную боковую деталь таким же образом.
- Измените приспособление типа «ласточкин хвост» на конфигурацию штифта. Вам также, вероятно, придется заменить сверло на сверло для прямой резки.Совместите заднюю часть ящика с приспособлением в соответствующем месте и отрежьте штифты.
- Выньте деталь из зажимного приспособления и проверьте ее совместимость с одной из хвостовых досок. Если вас устраивает посадка, поверните приклад на 180 градусов и отрежьте противоположные штифты.
- Таким же образом прорежьте штифты в четвертой стороне коробки.
Вырежьте канавки для нижней части ящика
Когда штифты и хвосты правильно прорезаны с четырех сторон, мы обратим наше внимание на прорезание канавки в каждой из четырех частей ящика для размещения дна ящика.
- Начните с сухого соединения всех четырех сторон коробки. Сделайте небольшую отметку карандашом на внутренней нижней части каждой из четырех сторон, чтобы обозначить, на какой стороне каждой детали следует вырезать канавку.
- Установите фрезер и стол для фрезерования с помощью прямой режущей фрезы 1/4 дюйма и упора. Фрезу следует отрегулировать на высоте 3/8 дюйма над столом, с упором на 1/4 дюйма с задней стороны бит
- Затем проверьте толщину четырех частей ложи. Если вы использовали ложу 1x, толщина, скорее всего, составила бы 3/4 дюйма.
- Измерьте это расстояние от края сверла вдоль упора и сделайте карандашные отметки на упоре с каждой стороны сверла на этом расстоянии. Это будет обозначать начальную и конечную точки канавки.
- Надев соответствующие средства защиты глаз и слуха, включите маршрутизатор. Повернув режущую сторону ложи к столу, а нижний край — к упору, поместите торец (противоположный концу у долота) напротив стола, так чтобы передняя кромка находилась чуть выше насадки. Совместите конец доски с дальней отметкой карандаша и осторожно наклоните приклад на сверло.
- Сдвиньте приклад вперед, крепко удерживая его на столе и вплотную к упору, пока задний край не достигнет первой карандашной отметки.
Затем осторожно наклоните приклад и снимите задний край биты.
- Точно таким же образом прорежьте канавки на трех других заготовках.
- Обрежьте фанерное дно 1/4 дюйма по размеру. Размеры дна должны быть на 1/2 дюйма длиннее (в каждом направлении), чем внутренние размеры ящика ящика типа «ласточкин хвост». Например, у вышеупомянутой коробки 18 дюймов на 12 дюймов нижняя часть должна быть обрезана до размера 17 дюймов на 11 дюймов.Это позволит дну ящика плавать в канавках с небольшим люфтом.
Начало сборки ящиков
Прежде чем мы перейдем к окончательной сборке, неплохо было бы полностью подогнать всю коробку ящика типа «ласточкин хвост». Если потребуются какие-либо корректировки, их будет намного проще исправить до того, как на сборку будет нанесен клей.
- Установите «сухую» с одной из двух сторон передней и задней части ящика.Затем задвиньте дно ящика и установите четвертую сторону всухую. Когда вы уверены, что подгонка идеально подходит, разберите пять частей.
- Чтобы начать окончательную сборку, нанесите каплю клея для деревообработки на каждый из «ласточкин хвост», как показано на рисунке. Нанесите клей либо небольшой щетиной, либо тонким кусочком обрезков, который легко поместится в хвосты. Нанесите тонкий ровный слой клея на все три края каждого ласточкиного хвоста.
Присоедините штифты к хвостовикам
- При правильном приклеивании хвостовика вставьте соответствующую доску для штырей в этот ласточкин хвост и, если необходимо, постучите резиновым молотком, пока соединение не будет установлено должным образом.Немедленно сотрите излишки клея, которые могли выдавиться из стыка.
- Повторите эти шаги с противоположным хвостом на буфете и прикрепите доску к этому противоположному хвосту.
Вставьте нижнюю часть ящика
Собрав три из четырех сторон ящика, вставьте нижнюю часть ящика в пазы. Для крепления дна ящика не должно использоваться клея, так как дно должно свободно скользить в канавке, чтобы приспособиться к сезонным колебаниям ложи.
Просто установите край ящика типа «ласточкин хвост» на деревообрабатывающий стол так, чтобы две доски для булавок выступали вертикально, и задвиньте дно ящика в пазы на досках для иголок. Вставьте нижний край дна ящика в паз откидного борта внизу.
Присоедините четвертую сторону ящика с ящиком
- Вставив нижнюю часть ящика «ласточкин хвост» в канавки, нанесите клей на хвостовики на каждом конце второго откидного борта и наденьте хвостовики на штифты доск, чтобы закончить ящик ящика.
- Вставьте нижнюю часть ящика в паз и постучите по боковой стороне ящика резиновым молотком.
- Немедленно сотрите излишки клея, которые могли выдавиться из стыков.
Зажмите ящик
- С четырьмя сторонами на месте, скрепите задние доски вместе с помощью нескольких длинных зажимов для труб или стержневых зажимов, чтобы удерживать устройство, пока клей высохнет. Обязательно выполните перекрестные измерения, чтобы проверить устройство на квадратность, прежде чем отложить его для просушки.
Отрегулируйте ящик ящика типа «ласточкин хвост», если он не квадратный, и снова зажать.
- Отложите сборку для просушки.
СОВЕТ: Всегда зажимайте ящик парой зажимов снизу и хотя бы одним зажимом сверху. Проверьте четыре соединения, чтобы убедиться, что они правильно сидят. При необходимости постучите по стыку резиновым молотком, чтобы затянуть его. Также рекомендуется использовать пару кусков обрезков между губками зажимов и задними панелями, чтобы предотвратить образование рубцов от зажимов.
Отшлифуйте сборку и прикрепите переднюю часть ящика
Как только клей в стыках ящика высохнет, мы подготовимся к завершению ящика.
- Начните с шлифования коробки и стыков «ласточкин хвост» с помощью все более мелкой наждачной бумаги, пока стыки и коробка ящика не станут гладкими. Отложите коробку в сторону.
- Отмерьте и обрежьте переднюю часть ящика в соответствии с чертежами проекта, который вы строите, и при необходимости нанесите декоративную кромку с помощью соответствующей фрезы.
Отшлифуйте переднюю часть ящика, снова используя наждачную бумагу все более мелкой зернистостью.
- Поместите декоративную переднюю часть ящика на переднюю часть ящика и поместите ее в нужное место.Зажмите переднюю часть ящика на месте и прикрепите к ящику ящика типа «ласточкин хвост» с помощью нескольких шурупов с потайной головкой.
- После того, как будет нанесена соответствующая отделка, прикрепите тяги ящиков на свои места. Обязательно просверлите отверстия для тяги ящика.
Building A 12-дюймовый фуганок
Я начал этот проект еще в октябре прошлого года с идеей, что я мог бы работать, когда у меня будет время, между другими проектами. Я только что закончил его создавать, поэтому решил, что собрал эту статью, чтобы систематизировать сделанные мною видео, освещающие прогресс.
В этом первом видео я обрабатываю конец фрезерной головки, которая пришла из моего старого строгального станка, чтобы принять V-шкив стандартного размера:
youtube.com/embed/KoMaEdpXLGg» allowfullscreen=»»/>После того, как вал стал нужного размера, мне пришлось сделать из куска стали ключ, чтобы закрепить шкив на конце режущей головки. Подшипник на конце был абсолютно сухим, поэтому я нагрел его и добавил немного масла, чтобы реактивировать (надеюсь) смазку, которая там была:
Следующая операция — изготовление опорных блоков для каждого конца фрезерной головки.Они были сделаны из плоской стали и твердого клена и будут прикреплены болтами к конструкции фуганка:
В этом я выбираю двигатель, который буду использовать для фуганка, глядя на два из самых больших, которые у меня есть. Я также начал строить фуганок, сделав две основные боковые планки из фанеры:
В этом видео я добавил шпильки с резьбой к боковым панелям, чтобы установить опорный блок. Я также показываю план, который я составил для фуговального станка к этому моменту, и перехожу к некоторым деталям:
С режущей головкой, временно установленной на боковые направляющие, я добавил внизу панель для крепления двигателя:
Режущая головка на этом видео установлена постоянно, а блоки из твердой древесины добавлены, чтобы зафиксировать их на боковых панелях.Затем я сделал разгрузочный стол и поставил его на место:
В этом я вырезал стальную крышку для разгрузочного стола. Я также добавляю регулировочные планки по бокам разгрузочного стола, чтобы точно расположить его:
Затем я строю подающий стол после добавления критических распорок к раме фуговального станка:
youtube.com/embed/Ee0a1w8ljpA» allowfullscreen=»»/>Сейчас четыре месяца спустя, и я говорю о проблемах, которые замедлили реализацию проекта, в частности, о стальных крышах и о том, что они недостаточно плоские.Также запускаю и впервые пользуюсь фуганком:
В этом видео финальной сборки я добавляю шнур питания, переключатель и защиту ремня. Так же делаю и устанавливаю забор:
Фуганок готов, но я могу внести в него некоторые улучшения в будущем и буду добавлять любые обновления в эту статью по мере их появления.
Если вам интересно, доступна модель SketchUp для моего оригинального дизайна:
Для просмотра модели на вашем компьютере должна быть установлена программа SketchUp.Обратите внимание, что это всего лишь модель, а не полный план.
КАК СОЗДАТЬ ТАБЛИЦУ: Уловки, чтобы сделать это действительно, действительно правильно
ОБНОВЛЕНО 19 июля 2019: Создание стола — один из самых обманчиво простых проектов по деревообработке. Что может быть проще, чем склеить несколько досок и нанести финиш? Но реальность часто удивляет, потому что создание стола — и особенно его столешницы — может пойти не так, как вы, возможно, не заметите, пока не станет слишком поздно.Вот мои любимые советы по построению стола, а также советы, как избежать неприятностей.
Первым серьезным проектом в области деревообработки, которым я занялся еще в начале 80-х, был стол. Получилось не так хорошо, как я надеялся, но с тех пор я кое-что узнал. Если после прочтения этой статьи у вас возникнут вопросы, напишите мне по адресу [адрес электронной почты защищен]. Мы вместе во всем разберемся.
Как построить таблицу Шаг № 1: Выбор размера и формы
Кусок фанеры 1/2 дюйма предлагает лучший подход для определения оптимального размера и формы вашей столешницы, потому что он позволяет вам тестировать и настраивать различные параметры в 3D. Отрежьте фанеру до максимального размера, который вам может понадобиться, установите ее на что-нибудь в том месте, где будет готовый стол, а затем поживите с ней некоторое время. Верх должен быть уже? Короче? Пришло время узнать. При необходимости отпилите немного фанерного макета, а затем продолжайте жить с новым размером, пока не найдете золотую середину.
Как собрать стол. Шаг № 2: Соединение досок и склейки
Четкие и плотные соединения являются ключом к любой отличной столешнице, и именно здесь на помощь приходит фуганок. Получите помощь, поддерживая доски длиннее полутора футов во время работы. Кроме того, если некоторые стыки не срастаются плотно, несмотря на все ваши усилия, попробуйте переместить доски в новое место, если позволяет структура волокон. Некоторые края просто естественно более плотно прилегают друг к другу, чем другие. У вас нет фуганка? Куски строганого бруса иногда прекрасно сочетаются друг с другом без стыков. Попробуйте разные доски в качестве соседей, чтобы увидеть, какие из них лучше всего подходят.
Даже небольшая столешница представляет собой проблему, если склеенные между собой доски имеют ступенчатые перекосы в местах пересечения из-за деформации . Да, вы можете отшлифовать их, но чем больше топографической шлифовки вам потребуется, тем менее плоской и ровной будет ваша готовая столешница. Чем ровнее и лучше выровнены ваши доски, когда они находятся в зажимах, тем счастливее вы будете позже. Здесь могут помочь концевые зажимы и клеящие соединения.
Когда все доски находятся в зажимах для основных труб и готовы соединиться под давлением, установите зажимы меньшего размера на каждом стыке на всех концах платы. Это позволяет идеально выровнять доски, по крайней мере, по концам.В зависимости от того, как ваши доски ведут себя по остальной длине, вам могут понадобиться или не потребоваться герметики. Эти изогнутые куски дерева зажимаются поперек склеивания, сверху и снизу, выравнивая доски по вертикали и сводя к минимуму шаги между ними. Я использую твердые породы дерева длиной 1 дюйм на 4 дюйма для герметиков, с одним изогнутым краем, таким образом, чтобы его концы имели ширину около 2 1/2 дюймов.
Зажмите изогнутые края герметика внутрь, чтобы они выровняли доски столешницы посередине, затем затяните основные зажимы, чтобы стянуть доски вместе. Если ширина досок, которую вы используете, позволяет, предварительно приклейте доски для столешницы на участках, достаточно узких, чтобы поместиться в строгальный станок. Пропустите их через строгальный станок, чтобы очистить и выровнять клеевые швы, затем вернитесь к зажимам для окончательного приклеивания. Подобная поэтапная работа сокращает количество клеевых швов, которые вам нужно отшлифовать, а затем выровнять.
Как построить стол Шаг № 3: Выравнивание и шлифование
Даже при самой тщательной работе по склеиванию будет хотя бы небольшое смещение между платами, когда столешница выйдет из зажимов. Здесь помогает шлифование с поперечным зерном. С абразивом зернистостью 80 в ленточной шлифовальной машине выровняйте столешницу, работая поперек волокон, а не параллельно им. Это быстрее удаляет древесину, что упрощает получение плоских результатов. Перейдите к шлифованию с параллельным зерном с помощью ленты с зернистостью 80, когда все стыки будут плоскими, затем переключитесь на ленты с зернистостью 120 и 180, также идущие параллельно волокнам.
Хотя заманчиво использовать случайную шлифовальную машинку для сглаживания поверхности стола на последних этапах, я никогда не делаю этого. Причина в качестве отделки. Шлифовальные машины со случайной орбитой часто оставляют после себя вихревые следы, которые не появляются до окончания обработки. Лучше всего шлифовать вручную, используя бумагу с зернистостью 180, затем 220 только в направлении волокон древесины. Отделка столешницы исследуется более внимательно, чем отделка деревом где-либо еще, поэтому вам нужно устранить все недостатки.
Оставьте столешницу дольше, чем необходимо, пока не закончите шлифование, а затем отрежьте до окончательной длины. Большинство столешниц слишком широки, чтобы их можно было обрезать на столовой пиле, даже с поперечными салазками, и именно здесь я использую ручную циркулярную пилу.Зажмите направляющую полосу так, чтобы она располагалась под прямым углом к одному краю, а затем следуйте по ней пилой. Повторите процесс с другим концом, затем осторожно с помощью ручной ленточной шлифовальной машины удалите все следы лезвия на краях. Звучит как грубый процесс, но так можно добиться отличных результатов.
Кромки столешницы сильно изнашиваются, а их закругление помогает продлить срок службы кромок. Даже если вы предпочитаете внешний вид столешницы с квадратными краями (как и я), округление с помощью скромной фрезы с радиусом 1/8 дюйма значительно продлит срок службы.
Как построить стол Шаг № 4: Завершение
Когда дело доходит до выбора отделки, есть два основных варианта. Типичный подход с использованием морилки и уретана создает гладкую, легко протираемую поверхность, но когда эта отделка в конечном итоге изнашивается, невозможно восстановить ее привлекательно. Шлифование и повторная шлифовка древесины — единственный способ вернуть ей респектабельность. С другой стороны, масляная и восковая отделка требует больше времени на первоначальное нанесение, но их легко ремонтировать и омолаживать, установив столешницу на место. Обычное повторное нанесение работает нормально.
Хотите увидеть, как нанести очень прочное, красивое и ремонтопригодное масляное покрытие на столешницу? Щелкните здесь, чтобы просмотреть подробный видеоурок.
Хотите, чтобы поверхность вашего стола была гладкой из уретана ? Нажмите здесь, чтобы посмотреть удивительный, малоизвестный трюк для полировки полиуретановых деревянных покрытий. Вы будете поражены гладкостью стекла, которого вы можете достичь. Это одно из самых популярных моих видео.
Как и любой другой успех деревообработки, создание столешницы зависит от правильного выполнения каждого шага перед тем, как двигаться дальше. Единственная разница в том, что столешницы — это, вероятно, самая очевидная и заметная работа по дереву, которую вы когда-либо делали. Еще одна причина, чтобы все исправить.
.