- Выбираем электроинструмент для «сверления»: правила осознанной покупки
- Ударные дрели
- Перфораторы
- Шуроповерты
- На фото: шуруповерт 505 TBS / 505 TBS Set компании Kress.
- При покупке любого электроинструмента нужно обращать внимание на его вес. С одной стороны, тяжесть — это неудобство в работе. Но с другой — свидетельство надежности агрегата, который изготовлен из прочных материалов. В статье использованы изображения: bosch-professional. com, skil.ru, kress-tools.com (adsbygoogle = window.adsbygoogle || []).push({}); (adsbygoogle = window.adsbygoogle || []).push({}); 4-ка лучших направляющих для дрели Механика сверления отверстий на первый взгляд кажется достаточно простой. Вращается сверло, вы прилагаете усилие вдоль оси инструмента, и углубляетесь в заготовку. При этом на сверло действуют различные векторы силы, от которых напрямую зависит точность и качество сверления. Вращение вокруг своей оси, да еще и с усиленным трением на кромке, стремится увести сверло в сторону. Особенно это заметно при начале работ, когда наконечник еще не заглублен в заготовку. Если поверхность имеет обратный радиус закругления (например, труба), начать сверление практически невозможно: кончик будет все время соскальзывать. При работе с металлами, можно применять кернение: создание небольшого углубления в нужной точке. Однако такой способ не всегда возможен. А если вы работаете с пластиком или керамикой – он неприемлем вовсе. Уже в процессе углубления в материал (речь идет о глубоких отверстиях, где длина намного превосходит диаметр), паразитный вектор силы стремится увести сверло от прямолинейного движения вдоль оси. if ( rtbW >= 960 ){ var rtbBlockID = "R-A-744045-3"; } else { var rtbBlockID = "R-A-744045-5"; } window.yaContextCb.push(()=>{Ya.Context.AdvManager.render({renderTo: "yandex_rtb_2",blockId: rtbBlockID,pageNumber: 2,onError: (data) => { var g = document.createElement("ins"); g.className = "adsbygoogle"; g.style.display = "inline"; if (rtbW >= 960){ g.style.width = "580px"; g.style.height = "400px"; g.setAttribute("data-ad-slot", "9935184599"); }else{ g.style.width = "300px"; g.style.height = "600px"; g.setAttribute("data-ad-slot", "9935184599"); } g.setAttribute("data-ad-client", "ca-pub-1812626643144578"); g.setAttribute("data-alternate-ad-url", stroke2); document.getElementById("yandex_rtb_2").appendChild(g); (adsbygoogle = window.adsbygoogle || []).push({}); }})}); window.addEventListener("load", () => { var ins = document.getElementById("yandex_rtb_2"); if (ins.clientHeight == "0") { ins.innerHTML = stroke3; } }, true); Это происходит по причине неравномерного трения о боковые стенки отверстия. Точный угол сверления относительно поверхности заготовки выдержать крайне сложно, тем более на глубоких отверстиях. Выполнить такую работу вручную практически нереально, особенно если задано значение, отличное от 90°. Если вы сверлите отверстия большого диаметра (например, углубление под выключатель в стене), начать работу, и выдержать направление еще сложнее. Да, существуют сверлильные станки. Но они позволяют работать лишь с заготовками небольшого диаметра. К тому же, громоздкое оборудования занимает место в квартире. Кроме того, работа на стене с помощью станка не выполняется. Для облегчения пользования дрелью производители предлагают специальные направляющие. Это приспособления, позволяющие сохранить правильное позиционирование инструмента относительно заготовки как перед началом работ, так и в процессе заглубления в материал. Главное преимущество этих устройств – мобильность и ценовая доступность (относительно сверлильных станков). (adsbygoogle = window.adsbygoogle || []).push({}); Виды направляющих для дрели Кондуктор
- Сверла для глубокого сверления. Пушечное сверло.
- Сверление трением — Centerdrill сверла трения, термосверла, метчики с накаткой резьбы и инструкция к применению. Статьи компании «Инструмент
- Практическое руководство по процессу формовки отверстий трением Centerdrill
- Преимущества процесса формовки трением
- Подробнее о процессе формовки отверстий трением
- Обрабатываемые материалы
- Примеры применения различных пуансонов Centerdrill
- Специальные конструкции инструментов
- Требования к процессу формовки и сверления трением — необходимое механическое оборудование (станки)
- Условия осуществления процесса и параметры:
- ЧПУ программирование для процесса формовки трением
- Инструмент для сверления и обработки отверстий — Студопедия
- Что такое бурение глубоких отверстий
- Осмотр бурового инструмента для забойных скважин на нефтяной скважине
- BTA Станки для глубокого сверления отверстий
Выбираем электроинструмент для «сверления»: правила осознанной покупки
Что выбрать — ударную дрель, перфоратор или шуруповерт? Функции, особенности и основные характеристики каждого электроинструмента.
На фото:
Ударные дрели
Основные функции. Предназначены для сверления с высокой точностью отверстий в древесине, металле, пластике. Кроме того, сочетание вращательного движения сверла с поступательным движением удара позволяет сверлить бетон и строительную керамику. Дрелью с дополнительной оснасткой закручивают и выкручивают винты и шурупы, фрезеруют, шлифуют, полируют, удаляют ржавчину, а также смешивают краску, клей и растворы.
На что обратить внимание
Мощность. Для выполнения небольших отверстий диаметром 6-15 мм достаточно дрели мощностью 400-650 Вт, для крупных (а также для смешивания красок и растворов) понадобится минимум 700 Вт.
Максимальный диаметр.
Полезные опции. Чем больше дополнительных опций, тем дороже электроинструмент. С другой стороны, многие из них делают работу с дрелью безопаснее и комфортнее. Так, муфта сцепления разрывает соединение инструмента с патроном при превышении допустимой нагрузки (например, при заклинивании сверла), резиновая накладка на рукоятку гасит вибрацию инструмента, встроенный уровень помогает держать дрель горизонтально, а лазерный уровень позволяет сделать точную разметку отверстий.
Перфораторы
На фото: перфоратор 1780 MA компании Skil.
Основные функции. Перфоратор — это тяжелое оборудование для выполнения отверстий большого диаметра в очень твердых материалах. Кроме того, этот электроинструмент прекрасно подходит для удаления старой штукатурки и облицовки стен и пола из керамической плитки.
На что обратить внимание
Типы ударного механизма. Перфораторы с электропневматическим ударом мощнее и дороже электромеханических.
Функция долбления. Все перфораторы применимы для сверления, а вот долбить отверстия может только электроинструмент с функцией удара без вращения.
Максимальный диаметр отверстия. Этот показатель определяет, в том числе, и оптимальный размер сверла.
Крутящий момент. Чем выше крутящий момент (Н·м), тем лучше. Большой крутящий момент помогает сверлу преодолевать значительное сопротивление материала.
Емкость аккумулятора. Продолжительность работы инструмента на одной зарядке литиево-ионных аккумуляторов дольше. Снижение мощности инструмента заметно, когда аккумулятор уже почти разрядился. Никелево-кадмиевые перфораторы теряют заряд постепенно.
Особенности. В отличие от дрели, на перфоратор нельзя давить во время сверления. Пневматический ударный механизм сам создает необходимое усилие. Перфоратор не лучший инструмент для долбления. Если долбление займет более 30% от общего времени сверления, электроинструмент просто не справится с нагрузкой.
Полезные опции. Учтите, что дополнительные опции (уровень для удобной установки сверла, датчики износа контактных щеток, датчик перегрузки двигателя и т.д.) увеличивают стоимость перфоратора.
Шуроповерты
На фото: шуруповерт 505 TBS / 505 TBS Set компании Kress.
Основные функции. Дрели-шуруповерты легче обычных. Они предназначены для вкручивания и выкручивания шурупов (при помощи специальной оснастки — «биты»), а также для сверления отверстий в не очень твердых материалах: древесине, металле и пластике. Как правило, работают шуруповерты на аккумуляторах (в комплект часто входит сменный).
На что обратить внимание
Оптимальная емкость аккумулятора. Указывается в ампер-часах (1,3 — 2 А·ч) и определяет время работы инструмента до разрядки аккумулятора. От одной зарядки аккумулятора емкостью 1,3 А·ч можно закрутить около 200 шурупов. Кстати, никель-кадмиевый аккумулятор, в отличие от литиево-ионного, нельзя заряжать, пока уровень его зарядки ещё позволяет использовать инструмент для работы.
Тип зарядного устройства. В комплект могут входить обычные или импульсные зарядные устройства. Чем короче время зарядки аккумулятора, тем лучше. У обычных зарядных устройств длительность зарядки аккумулятора — от 3 до 18 часов. Большинство импульсных устройств заряжает аккумулятор за 1 час. Есть устройства для срочной подзарядки: за первые 5 минут они обеспечат зарядку 15% емкости аккумулятора.
Тип фиксации оснастки. Ключевые патроны удерживают сверло прочнее, но устанавливать сверла в самозажимные патроны быстрее и проще.
Максимальный диаметр. Относительная величина: вдревесине дрель-шуруповерт может сделать отверстие диаметром 20-30 мм, а в металле 10-16 мм.
Крутящий момент. Для дрелей-шуруповертов с аккумуляторным питанием особенно важна величина крутящего момента: она должна быть не менее 50 Н·м.
Полезные опции. Механический удар для отверстий в кирпиче и бетоне, индикатор уровня зарядки аккумулятора, встроенный уровень, автоматический тормоз, электронное управление зарядкой — все это облегчает работу, но повышает цену покупки.
Важно! Существуют электроинструменты, похожие на дрели-шуруповерты, но совершенно не рассчитанные на сверление отверстий. Бывают и универсальные дрели-шуруповерты с двумя сменными патронами: один для сверления, второй — для вкручивания шурупов. Некоторые производители предлагают дрели-шуруповерты, аккумулятор которых пригоден для зарядки других электроинструментов, например, компрессора или фонаря.
Аккумулятор достигает номинальной емкости только после 3-5 зарядок.
При покупке любого электроинструмента нужно обращать внимание на его вес. С одной стороны, тяжесть — это неудобство в работе. Но с другой — свидетельство надежности агрегата, который изготовлен из прочных материалов.
В статье использованы изображения: bosch-professional. com, skil.ru, kress-tools.com
4-ка лучших направляющих для дрели
Механика сверления отверстий на первый взгляд кажется достаточно простой. Вращается сверло, вы прилагаете усилие вдоль оси инструмента, и углубляетесь в заготовку. При этом на сверло действуют различные векторы силы, от которых напрямую зависит точность и качество сверления.
- Вращение вокруг своей оси, да еще и с усиленным трением на кромке, стремится увести сверло в сторону. Особенно это заметно при начале работ, когда наконечник еще не заглублен в заготовку. Если поверхность имеет обратный радиус закругления (например, труба), начать сверление практически невозможно: кончик будет все время соскальзывать. При работе с металлами, можно применять кернение: создание небольшого углубления в нужной точке. Однако такой способ не всегда возможен. А если вы работаете с пластиком или керамикой – он неприемлем вовсе.
- Уже в процессе углубления в материал (речь идет о глубоких отверстиях, где длина намного превосходит диаметр), паразитный вектор силы стремится увести сверло от прямолинейного движения вдоль оси.
Это происходит по причине неравномерного трения о боковые стенки отверстия.
- Точный угол сверления относительно поверхности заготовки выдержать крайне сложно, тем более на глубоких отверстиях. Выполнить такую работу вручную практически нереально, особенно если задано значение, отличное от 90°.
- Если вы сверлите отверстия большого диаметра (например, углубление под выключатель в стене), начать работу, и выдержать направление еще сложнее.
Да, существуют сверлильные станки. Но они позволяют работать лишь с заготовками небольшого диаметра. К тому же, громоздкое оборудования занимает место в квартире. Кроме того, работа на стене с помощью станка не выполняется.
Для облегчения пользования дрелью производители предлагают специальные направляющие. Это приспособления, позволяющие сохранить правильное позиционирование инструмента относительно заготовки как перед началом работ, так и в процессе заглубления в материал. Главное преимущество этих устройств – мобильность и ценовая доступность (относительно сверлильных станков).
Виды направляющих для дрели
Кондуктор
Устройство представляет собой корпус из пластика, в котором жестко закреплены направляющие втулки под различные диаметры сверл. Благодаря ограничению отклонения, можно выполнять сверление с приемлемой точностью, причем на различных материалах.
Кондуктор удерживается одной рукой, а вторая держит дрель. Нет необходимости постоянно контролировать угол «увода». Кроме того, приспособление позволяет точно начать сверление в заданной точке. Кернение не потребуется.
Практически все направляющие с углом 90°, позволяют работать на закругленных поверхностях (трубах). Для этого на нижней опорной пятке предусмотрен специальный паз.
Существуют и более простые конструкции (если обойма под несколько диаметров неудобна в применении). Например, оправка, в которую м
Сверла для глубокого сверления. Пушечное сверло.
В машиностроении повсеместно применяются детали со значительной длиной и глубокими внутренними отверстиями. Такими деталями являются валы различного функционального назначения, оси, шпиндели. Для получения таких отверстий применяют глубокое сверление отверстий в металле.
Отметим, что в технологии металлообработки глубоким называют сверление, при котором длина отверстия составляет пять и более его диаметров.
Глубокое сверление может выполняться для получения как сквозных, так и глухих отверстий.
Технология глубокого сверления является довольно сложным процессом, поскольку приходится преодолевать одновременно несколько трудностей:
- Во-первых, возникают сложности с отведением от обрабатываемой детали металлической стружки, а также с подачей смазывающе-охлаждающей жидкости.
- Во-вторых, довольно сложно обеспечить подачу и центровку сверлильного инструмента с достаточной точностью.
Для выполнения работ по получению глубоких отверстий применяется специализированный инструмент для сверления отверстий. Одним из типов такого инструмента является пушечное сверло.
Что такое, и для чего предназначено пушечное сверло
Пушечное сверло — это режущий инструмент преимущественно цилиндрической формы с переменным по длине сечением. Оно является инструментом однорезцового вида.
Для отведения отработанной стружки от обрабатываемой детали на поверхности такого сверла имеется выемка с сечением в форме буквы V. Данная проточка выполнена по внешней поверхности сверла.
В общем случае, при помощи пушечного сверла возможно получить отверстия с диаметром в диапазоне от 0,5 миллиметров до 10 сантиметров. Специальное отверстие для подвода смазывающе-охлаждающей жидкости обычно отсутствует. Сверление производят на малой частоте вращения металлообрабатывающего агрегата.
В рабочей части пушечное сверло имеет форму полукруга. Плоская поверхность полукруглого стержня является передней поверхностью сверла. Под прямым углом к оси сверла на торце стержня образуется режущая кромка. Задний торец инструмента имеет плоскую наклонную под углом 10-20 градусов форму.
Для обеспечения более точного направления опорная поверхность пушечного сверла имеет цилиндрическую форму. На опорной поверхности выполняются лыски под 35-40 градусов, а также обратный конус 0,04-0,05 миллиметров на 10 сантиметров длины. Эти мероприятия способствуют уменьшению трения инструмента о внутренние стенки обрабатываемой детали.
Для удаления стружки, образовавшейся в процессе резания, приходится регулярно выводить сверло из детали. Геометрия сверла способствует тяжелым условиям работы инструмента, что уменьшает его долговечность и снижает точность процесса резания.
Отметим, что в современной металлообработке есть более точные и производительные способы получения глубоких отверстий. Обработка детали пушечным сверлом считается устаревшим и малоэффективным методом глубокого сверления.
Виды сверл для глубоко сверления
В сегодняшней технологии металлообработки применяют несколько типов сверл для глубокого сверления деталей.
Рассмотрим основные их типы:
- Пушечные сверла. Характеристики данного типа сверл были рассмотрены выше. В последнее время выпускается инструмент с несколько измененной формой по отношению к традиционной. Это позволяет повысить производительность процесса и качество обрабатываемых деталей. Есть смысл применять пушечные сверла при обработке отверстий небольшого диаметра. Длина отверстий обычно не более 40 диаметров. Точность по IT9, а чистота поверхности составляет 0,09 – 3,5 мкм.
- Ружейное сверло, выполненное как единое целое. Их еще называют монолитные сверла, поскольку они выполнены цельно из твердосплавного материала. Для подвода смазывающе-охлаждающей жидкости внутри сверла имеется специальный проход. Стружка и СОЖ отводятся от детали через наружную винтовую канавку. Их применяют для сверления отверстий до 100 миллиметров. Глубина – до 100хD. Инструмент получил такое название, поскольку раньше его применяли для обработки стволов огнестрельных орудий.
- Ружейное сверло, выполненные по технологии фиксации режущих пластин из твердого сплава методом пайки. Как и другие сверла этого типа обеспечивают высокую точность размеров с минимальным отклонением оси сверления.
- Ружейное сверло, имеющее дополнительные режущие пластины. Такие сверла делают процесс резания более производительным.
- Спиральные сверла с цилиндрическим хвостовиком. Производятся согласно требованиям ГОСТ 886-77. Они имеют удлиненную режущую часть, которая может быть выполнена цельно из быстрорежущей стали либо иметь твердосплавные пластины. Подвод СОЖ может быть как изнутри, так и снаружи. Хвостовик может также иметь цилиндрическую форму.
- Перовые сверла. Их используют для сверления неглубоких отверстий ступенчатой формы.
- Эжекторные сверла. Используют для сверления глубоких отверстий в металлообрабатывающих аппаратах с размещением режущего инструмента в горизонтальной плоскости.
Важные особенности сверления глубоких отверстий
Глубокое сверление отверстий в металле является специфическим процессом металлообработки и требует соответствующего подхода. Эту операцию следует выполнять на специально предназначенных для этого станках для глубокого сверления.Важной особенностью процесса является точная центровка инструмента и исключение отклонения сверла по оси. Необходимо исключить биение инструмента. Чтобы получить отверстие с точными размерами и качественной поверхностью важно обеспечить место обработки достаточным количеством СОЖ.
Канавки для отвода стружки должны быть гладкими, чтобы обеспечить своевременный отвод стружки из зоны обработки.
Сверление глухих отверстий отличается в сторону усложнения тем, что в процессе работы нужно постоянно контролировать глубину отверстия. Для глубоких отверстий это вызывает некоторую сложность.
Выбор инструмента для глубокого отверстия
В первую очередь инструмент для глубокого резания должен соответствовать агрегату, на котором вы собираетесь производить операции резания. Хвостовик должен соответствовать патрону станка или автомата. Причем сверла для глубокого сверления должны обязательно устанавливаться на специально предназначенные для этих операций агрегаты.
Если при обработке нужно жестко исключить отклонение оси при сохранении высокой точности, лучше использовать цельное твердосплавное ружейное сверло.
Если обрабатываемый материал при обработке распускается на длинную стружку, следует применять инструмент со стружечными канавками с высокой чистотой поверхности. При работе с алюминиевыми сплавами используйте инструмент с одним лезвием и заточкой режущей кромки под 180 градусов.
В остальном следует выбирать инструмент в зависимости от длины и диаметра необходимого отверстия.
Расчёт длины однолезвийного сверла
Основные этапы сверления глубоких отверстий
Сверление глубоких отверстий в металле обычно выполняют в такой последовательности:
- Производится сверление в детали подготовительного отверстия с немного меньшим диаметром с допуском Н8.
- Основной обрабатывающий инструмент запускают на низких оборотах и медленно перемещают к торцу детали.
- Постепенно выводят инструмент на необходимые по технологии обороты и начинают подвод смазывающе-охлаждающей жидкости.
- Производят сверление детали на необходимую глубину. При этом инструмент не уводят из отверстия.
- Если по технологии используется инструмент значительной длины, то первую четверть реза выполняют на сниженной частоте вращения. Остальную часть отверстия вырезают на номинальной частоте вращения.
- При достижении необходимого значения глубины прекращают подачу смазочно-
- охлаждающей жидкости к инструменту.
- Затем сверло быстро отводят из зоны сверления и останавливают работу агрегата.
Данная технология является стандартной и может отличаться в зависимости от применяемого инструмента и металлообрабатывающих аппаратов.
Сверление трением — Centerdrill сверла трения, термосверла, метчики с накаткой резьбы и инструкция к применению.
Статьи компании «Инструмент
Практическое руководство по процессу формовки отверстий трением Centerdrill
Термосверление — сверла сухого трения, технология формовки отверстий и этапы процесса
ZECHA Tungsten Carbide Tools Manufacturing GmbH
С 1964 года компания ZECHA Tungsten Carbide Tools Manufacturing GmbH производит стандартные и специального назначения твердосплавные инструменты. Кроме разработки и производства пуансонов для формовки отверстий трением компания также производит режущий инструмент, инструмент для тиснения и формовки. Сталкиваясь с различными технологическими задачами, мы разрабатываем и производим специальный инструмент для их решения. Сейчас около 70 % нашей продукции применяется в качестве индивидуально разработанных инструментов в различных сферах производства. В настоящее время в компании работает около 75 сотрудников, площадь рабочих мощностей около 2600 м². Как пользоваться Руководством Формовка отверстий трением Centerdrill – это процесс, в результате которого получаются упрочненные втулки или небольшие отверстия в тонкостенном металле без применения резки. При этом используется трение и давление подачи для разогрева и формовки металла. Это Руководство содержит подробную информацию и технические данные по процессу формовки трением и разработано для того, чтобы помочь вам правильно использовать эту технологию для ваших нужд. Если у вас есть какие-либо вопросы, наши специалисты будут рады вам помочь.
Формовка отверстий трением Centerdrill – процесс
Благодаря процессу формовки трением могут быть произведены втулки и небольшие отверстия в тонкостенном металле (например, в стальном листе, в цветных металлах, в нержавеющих сталях) толщиной до 12 мм без использования резки. Высота получаемой втулки может превышать толщину материала в 4 раза при диаметрах от 1.8 до 32 мм. Процесс формовки основывается на разогреве материала под действием трения,
возникающего в результате действия комбинации осевой силы подачи и относительно высокой скоростью вращения пуансона. Разогретый металл становится пластичным, что позволяет получать отверстия.
Эта операция используется для получения:
• Резьбовых втулок
• Подшипниковых втулок
• Втулок под пайку
• Сквозных отверстий
• Сквозных отверстий с уплотненной кромкой для круглых профилей
Так как материал сжимается в процессе формовки, рéзьбы, формируемые после, имеют повышенную прочность и могут выдерживать больший момент затягивания. Благодаря Centerdrill дополнительные процессы, такие как упрочняющая сварка, использование заклепок или приваривание винтовой гайки к отверстию, теперь в прошлом. Специальная геометрия Centerdrill и использование твердого сплава обеспечивают высокую стойкость инструмента – до нескольких тысяч операций.
Преимущества процесса формовки трением
Практические преимущества:
• Высокая точность и повторяемость
• Меньший расход материала и более легкий вес деталей благодаря использованию только тонкого материала детали
• Не требуется смежный инструмент (например, матрица для пуансона), благодаря чему можно обрабатывать даже профили с труднодоступной внутренней поверхностью
• Формовка трением в наклонном положении
• Повышенный момент затягивания для резьбы (за счет наклепа при пластической деформации)
• Повышение жесткости конструкций (например, за счет меньшего использования многократных соединений)
• Использование только одного основного материала, что позволяет избежать электрохимической коррозии
• Высокая допустимая нагрузка подшипниковых втулок
• Упрочнение материала
• Простая в изучении и доступная для начала работы новая технология
Экономические преимущества:
• Бесстружечный процесс формовки
• Не требуются соединительные элементы
• Процесс может быть автоматизирован
• Достаточно вертикально-сверлильного станка – не требуется покупать дополнительного оборудования
• Минимальное время установки
Экологические преимущества:
• Высокопрочные соединения могут быть произведены с помощью Centerdrill без использования дополнительных материалов. Основной материал остается без примесей и может быть легко использован повторно. Не требуется стружкоудаление.
• Соединения Centerdrill – разъемные. Это дает существенные преимущества для последующего демонтажа в сравнении с другими процессами.
Варианты применения
Рисунок 1
Формовка отверстия трением ипоследующая формовка резьбы
в стальном листе.
Рисунок 2
Формовка отверстий трениемв круглой трубе.
Рисунок 3
Формовка отверстий трениемв прямоугольной трубе.
Подробнее о процессе формовки отверстий трением
Подготовка к сверлению трением
Вначале пуансонCenterdrill
располагается так,
чтобы он слегка
касался
поверхности
материала, затем к
нему прилагается
высокое осевое
усилие.
Плавное вхождение
За счет давленияподачи и скорости
вращения
пуансона
возникает нагрев
металла до
температуры
достаточной для
придания
материалу
пластичности.

(порядка 600˚ С)
После чего
Centerdrill
проникает в
материал за
считанные
секунды.
Сверление с вытеснением металла
Centerdrillвытесняет металл
в горизонтальном
и вертикальном
направлениях,
преимущественно
вниз, формируя
втулку.
Постепенно
давление подачи
уменьшается, а
скорость подачи
увеличивается по
мере
проникновения в
металл.
Результат сухого термосверления
В итогеполучается
законченная
втулка. Материал,
вытесненный
против
направления
подачи,
преобразуется в
обрамляющий
бортик в форме
кольца. Это
кольцо может
быть срезано в
процессе
аналогичной
операции
формовки
отверстия в
случае
использования
специального
торцующего
пуансона
Centerdrill,
который имеет
режущую
площадку на
пояске.
Вхождение метчика и нарезание резьбы
Втулка готова дляформовки резьбы
при помощи
бесстружечного
метчика
Centertap.
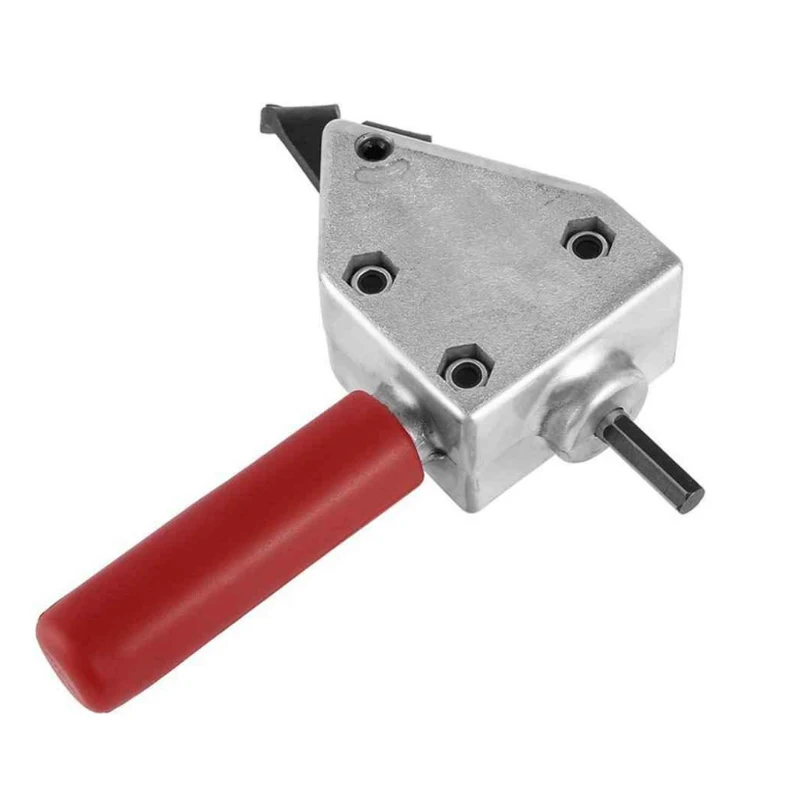
Формируемая при
помощи холодной
деформации
резьба повышает
твердость
материала за счет
наклепа.
Вкручивание в готовое отверстие с резьбой
В результатеимеем резьбовое
соединение,
способное
выдерживать
большой момент
затягивания без
сверления и
последующего
приваривания
винтовой гайки.
Обрабатываемые материалы
При помощи формовки трением можно обрабатывать практически все тонкостенные металлы (кроме олова и цинка).
В качестве примеров можно привести
• Стали, подвергаемые сварке
• Нержавеющая сталь
• Алюминий
• Медь
• Латунь
• Бронза
• Магнитные материалы
• Специальные сплавы
Форма фасонного пуансона Centerdrill
Пуансон Centerdrill состоит из цилиндрического хвостовика (cylindrical shank), фланца (collar), цилиндрической рабочей части (cylindrical part), конической рабочей части (conical part). Для различных целей разработано несколько стандартных фасонных пуансонов, основанных на этой конструкции. В основном они различаются по длине цилиндрической части и конструкции фланца.
Стандартный фасонный пуансон
Стандартные фасонные пуансоны Centerdrill бывают с короткой и удлиненной цилиндрической частью L5. При этом угол конической части у них одинаковый. При использовании этих версий пуансонов, материал, перемещаемый против направления подачи, остается на поверхности рабочей детали и образует обрамляющее кольцо. Существуют также короткие и удлиненные торцующие пуансоны. Отличие заключается в конструкции фланца, который имеет специальную часть для срезания обрамляющего кольца после завершения формирования отверстия. Она позволяет сразу получать плоскую поверхность за одну операцию формовки.
Оставляем снаружи дополнительную поверхность для резьбы за счет вышедшей массы металла
Короткий и удлиненный пуансон
Снимаем вышедшую на поверхность массу за счет юбки сверла
Короткий и удлиненный торцующий пуансон
Примеры применения различных пуансонов Centerdrill
Отверстия для резьбы — Короткий пуансон:
*Отверстие с обрамляющим кольцом.
Например, если нужно произвести резьбу M8 в стальной пластине (Ст.3) толщиной 2 мм, мы рекомендуем использовать короткий пунсон диаметром ø 7.3 мм. Он имеет такую длину цилиндрической части, чтобы сформировать втулку правильно.
Отверстия для резьбы — Удлиненный пуансон:
*Отверстие без обрамляющего кольца, сформированное торцующим пуансоном Centerdrill.
Для той же цели в случае толщины пластины 3 мм рекомендуется использовать длинный пуансон Centerdrill, так как модель с короткой цилиндрической частью сформирует коническую втулку, не пригодную для формирования резьбы.
Сквозное отверстие
Для получения сквозных отверстий мы в основном рекомендуем использовать длинные модели пуансонов Centerdrill, потому что удлиненная цилиндрическая часть полностью формует цилиндрическую втулку.
Специальные конструкции инструментов
Если наши стандартные продукты по каким-либо причинам не могут быть использованы или не отвечают Вашим специфическим потребностям, мы также производим специальные фасонные пуансоны по чертежам. Мы готовы обсудить требования Вашего технического задания. Ниже приведены примеры подобных специфических моделей.
конусной частью
С заостренным углом конусной части
С закругленной
конусной частью
Без фланца С увеличенной рабочей длиной цилиндрической части
Без рабочей цилиндрической части
Со сверлообразным наконечником
С витками
Требования к процессу формовки и сверления трением — необходимое механическое оборудование (станки)
Любой вертикально-сверлильный станок с достаточной мощностью или обрабатывающий центр с ЧПУ с требуемой скоростью и выходной мощностью обычно применимы для выполнения процесса формовки трением.
Зажимной патрон с охлаждающим кольцом Благодаря высоким температурным колебаниям и радиальной нагрузке, надежное крепление рабочей детали и фасонного пуансона имеют критическое значение.
Тепло выделяемое во время процесса не должно передаваться на шпиндель. Для этого, специально для процесса формовки трением Centerdrill, разработан специальный цанговый патрон с охлаждающим кольцом, которое рассеивает тепло и обеспечивает безопасное крепление. Цанговый патрон MC2 – стандартный для пуансонов диаметрами до 14 мм. Для больших диаметров рекомендуется использовать MC3. Для обрабатывающих центров с ЧПУ могут быть также использованы зажимные устройства HSK.
Цанги
Для оптимальной жесткости и надежного крепления фасонных пуансонов Centerdrill используются специальные цанги.
Разделительная паста
Для того чтобы продлить время службы пуансона Centerdrill, необходимо смазывать его специальной устойчивой к высокой температуре пастой, соответствующей обрабатываемому материалу. Паста может наноситься вручную или специальным распыляющим устройством.
Условия осуществления процесса и параметры:
Разогрев под действием трения и давление подачи производят деформацию и перемещение материала. Нагрев происходит благодаря высокой скорости вращения, соответствующей осевой силе и скорости подачи. Это означает, что независимо от размера отверстия, используемый сверлильный станок должен иметь скорость вращения до 4000 об/мин, выходную мощность до 5 кВт и скорость подачи до 1000 мм/мин. Правильная комбинация скорости подачи и скорости вращения зависит от марки (нержавеющая сталь, сталь или цветные металлы) и толщины стенки материала. Для достижения оптимальных результатов, материал должен поддерживать нужную температуру в процессе формовки и не остывать слишком быстро. Данные, приведенные ниже в этом документе, следует рассматривать только как ссылочные, они могут сильно меняться для различных материалов и толщин.
*Осевая сила и крутящий момент в процессе формовки трением
Осевая сила:
Как показано рисунке выше, требуемая осевая сила в начале процесса формовки трением очень велика и уменьшается к концу процесса, когда отверстие полностью сформировано. При обработке тонких материалов может понадобиться подкладка, чтобы избежать прогиба.
Крутящий момент:
Как показано на рисунке выше, увеличение вращательного момента обратно осевой силе до окончания процесса формовки отверстия. Таким образом, максимальный вращательный момент требуется на стадии преобразования втулки из конической в цилиндрическую форму. В этой точке требуется максимальное приложение силы (давления).
Скорость вращения об/мин:
Нормальная скорость (см. табл.) для маленьких диаметров отверстий относительновысока, приблизительно 3000 об/мин, и может достигать 4500 об/мин для цветных 12металлов. Для больших диаметров отверстия, таких как M20, требуемая скорость приблизительно 1000 об/мин. Нержавеющая сталь, теплопроводность которой меньше, может обрабатываться со скоростями до 20% меньшими.
Метрическая резьба
Диаметр резьбы | centerdrill диаметр пуансона, мм | centerdrill скорость вращения* при формировании отверстия, об/мин | Выходная мощность станка, кВт | centertap скорость вращения* при формировании резьбы, об/мин | |
M3 | 2.![]() | 3000 | 0.7 | 1500 | |
M4 | 3.7 | 2600 | 0.8 | 1100 | |
M5 | 4.5 | 2500 | 0.9 | 900 | |
M6 | 5.4 | 2400 | 1.1 | 800 | |
M8 | 7.3 | 2100 | 1.5 | 600 | |
M10 | 9.2 | 1800 | 1.7 | 380 | |
M12 | 10.9 | 1500 | 1.9 | 300 | |
M16 | 14.8 | 1400 | 2.4 | 200 | |
M20 | 18.7 | 1200 | 3.0 | 160 |
Выходная мощность кВт:
Для того чтобы достичь требуемой осевой силы и вращающего момента, нужен станок с достаточной выходной мощностью (см. табл.). Для отверстий малых диаметров требуется меньшая осевая сила и выходная мощность, чем для больших диаметров.
Выходная мощность станка определяет оптимальную скорость процесса. Быстрая обработка металла является определяющим фактором качества отверстия и, в особенности, времени службы пуансона. Если станок для этого не достаточно приспособлен, пуансон будет проникать в металл очень медленно и оставаться слишком долго на одном месте, а инструмент сильнее изнашиваться на этапе преобразования втулки из конической в цилиндрическую форму. Вдобавок к этому, металл будет остывать, что будет вести к низкому качеству обрамляющего отверстие кольца, залипанию металла на инструмент. Скорость подачи мм/мин:
Быстрое выполнение процесса формовки трением критично для достижения желаемого качества выполняемого отверстия. Скорость подачи изменяется в диапазоне 13 100-150 мм/мин (+/- 20 %) для металла толщиной 1-3 мм. Это означает, что для того, чтобы проделать отверстие ø 7.3 мм в металле толщиной 2 мм, при скорости подачи 150 мм/мин требуется приблизительно 2 – 3 секунды от первого контакта пуансона с пластиной до возврата назад.
Скорость подачи может быть увеличена для отдельных этапов процесса, и, таким образом, повышена общая производительность процесса, в частности, при работе на ЧПУ станках. При работе с торцующими пуансонами, рекомендуется существенно увеличивать скорость подачи на последнем этапе процесса для того, чтобы материал, удаляемый при срезании кольца, успевал отделиться от инструмента.
*Примечание. Данные приведены для Стали 45, в случае использования технологии с другими материалами, необходимо следовать следующим рекомендациям:
- Нержавеющая сталь: — диаметр пуансона Centerdrill для резьб M8 и больше следует выбирать на 0.1 мм больше — скорость вращения шпинделя меньше на 10-20 %
- Цветные металлы: — скорость вращения шпинделя до 50 % больше — скорость подачи: 150 мм/мин
Шаг резьбы | centerdrill отверстие под резьбу Ø (мм) | Короткий (мм) | удлиненный (мм) | Короткий торцующий (мм) | Удлиненный торцующий (мм) | L1 короткий (мм) | L1 удлиненный (мм) | D2 Ø хвостовика (мм) |
M2 x 0.![]() | 1.8 | 1.3 | 2.2 | 1.7 | 2.7 | 5.8 | 7.8 | 6.0 |
M3 x 0.5 | 2.7 | 1.3 | 2.2 | 1.7 | 2.7 | 6.7 | 8.7 | 6.0 |
M4 x 0.7 | 3.7 | 1.3 | 2.3 | 1.7 | 2.7 | 8.1 | 10.3 | 6.0 |
M5 x 0.8 | 4.5 | 1.3 | 2.4 | 1.7 | 2.8 | 9.2 | 11.8 | 6.0 |
M6 x 1 | 5.4 | 1.3 | 2.7 | 1.7 | 3.0 | 10.5 | 13.5 | 8.0 |
M8 x 1.25 | 7.3 | 1.5 | 3.5 | 2.0 | 4.5 | 13.5 | 18.1 | 8.0 |
M10 x 1.5 | 9.0 | 2.0 | 4.3 | 2.5 | 5.2 | 16.8 | 22.5 | 10 |
M12 x 1.75 | 10.9 | 2.4 | 4.9 | 2.8 | 5.9 | 19.![]() | 26.4 | 12 |
M14 x 2 | 13.0 | 2.4 | 5.3 | 3.0 | 7.0 | 23.5 | 31.3 | 14 |
M16 x 2 | 14.8 | 3.0 | 6.4 | 3.5 | 7.5 | 26.9 | 35.4 | 16 |
M20 x 2,5 | 18.7 | 3.7 | 8.0 | 4.5 | 9.0 | 34.1 | 44.3 | 18 |
ЧПУ программирование для процесса формовки трением
Удлиненный пуансон. Ссылочные значения для материала Ст 2 пс, сп (S235JR) с толщиной стенки 3 мм:
centerdrill диаметр отверстия под резьбу Ø (мм) | Максимальная толщина стенки (мм) | Вращение шпинделя (об/мин) | Длина рабочей части L1 (мм | Перемещение** (мм) | Интервалы перемещения (мм) | Подача (мм/мин) |
M6 — Ø 5.![]() long (long-flat) | 2.7 (3.0) | 2400 | 13.5 | 12.0 13.5 | 0 — 2 2 — 4 4 — 6 6 — 11 11 – до конца | 150 250 350 550 200 (900) |
M8 — Ø 7.3 long (long-flat) | 3.5 (4.5) | 2100 | 18.1 | 16.1 (18.1) | 0 — 2 2 — 4 4 — 7 7 — 14 14 – до конца | 150 250 350 550 200 (900) |
Увеличение скорости подачи до 1000 мм/мин в конце процесса дает лучший результат при удалении обрамляющего кольца при использовании торцующего пуансона.
При регулировании скорости подачи:
• Должна быть оптимизирована скорость процесса • Можно воздействовать на качество формуемой втулки и обрамляющего
кольца
• Можно воздействовать на время службы пуансона
*Все остальные данные для ЧПУ могут быть предоставлены по запросу.
Часто задаваемые вопросы по Сenterdrill
1. Что требуется для начала работы?
Чтобы не возникло проблем с формовкой отверстий трением, пуансон должен бытьжестко закреплен и вращаться с минимально возможным биением. Поэтому его следует
закреплять в специальную цангу и цанговый патрон Сenterdrill с охлаждающим кольцом.Охлаждающее кольцо предохраняет шпиндель станка от перегревания. Нужно также использовать разделительную смазку.
2. Какое оборудование требуется для формовки отверстий трением?
Любой сверлильный станок с достаточной выходной мощностью, который может обеспечивать нужную скорость вращения. Обычно это вертикально-сверлильный станок или обрабатывающий центр с ЧПУ. Для производства отверстий под резьбу M8 в металле толщиной 2 мм, требуется станок с минимальной скоростью около 2100 об/мин и выходной мощностью 1,5 кВт.
3. Можно ли использовать ручную дрель?
Обычно нет. Как было указано выше, минимальная скорость и требуемая выходная мощность слишком велики для ручной дрели. Так же требуется очень высокая осевая сила, чтобы перевести металл в пластическое состояние. Кроме того, при креплении инструмента в дрели возникает биение.
4. Можно ли использовать сверлильный патрон?
Нет, из-за опасности сломать пуансон и перегревания шпинделя. В случае использования сверлильного патрона гарантия не действует.
5. Нужно ли пользоваться смазкой?
Нужно обязательно использовать разделительную смазку. Разделительная паста Сenterdrill предохраняет пуансон от налипания металла и предотвращает его от застывания в материале. В зависимости от типа и толщины металла, пуансон следует смазывать каждые 5-50 операций формовки. Слишком большое количество пасты может слишком охладить пуансон и, таким образом, неблагоприятно повлиять на качество
формируемого отверстия и обрамляющего кольца.
6. Какие металлы можно обрабатывать при помощи процесса формовки трением?
Практически все тонкостенные металлы (кроме олова и цинка), например:
• Стали, которые могут подвергаться сварке
• Нержавеющие стали
• Алюминий
• Медь
• Латунь
• Бронза
• Магнитные материалы
• Специальные сплавы
7. Можно ли обрабатывать оцинкованные материалы?
Только в некоторых случаях. То, что температура плавления цинка не совпадает с температурой плавления для стандартных сталей, оказывает очень неблагоприятное воздействие на качество формуемого отверстия. Влияние этого эффекта зависит от толщины цинкового покрытия. Так же при формовке возможны случаи выгорания цинкового покрытия, что препятствует образования буртика в стали.
8. Какая последовательность процесса рекомендуется, чтобы произвести формовку отверстия и резьбы в оцинкованном материале?
По причине, описанной выше, лучше всего производить оцинковку материала после формовки. Если это невозможно, цинковый слой, если он слишком толстый и неровный, следует удалить перед началом формовки.
9. Какая максимальная толщина материала, в котором может быть получено отверстие путем формовки трением?
Известны примеры использования формовки трением для материала толщиной 12 мм. По нашему опыту, в большинстве приложений толщина материала 1-3 мм. Более тонкий материал также может быть обработан, но следует использовать снизу рабочей детали подложку, т. к. есть риск прогиба металла. Формовка отверстий в твердых материалах невозможна (см. таблицу на стр. 13).
10. Длинный или короткий пуансон следует использовать?
Наконечник каждого пуансона состоит из цилиндрической и конической части. Цилиндрическая часть отвечает за формирование цилиндрического канала отверстия. Если после формовки отверстия будет производиться формовка резьбы, рекомендуется оставлять канал отверстия слегка коническим в конце. В этом случае резьба получается прочнее. В то же время, если нужно получить сформованное отверстие, которое будет использоваться без резьбы, цилиндрическая часть должна иметь соответствующую длину. Длина пуансона зависит от толщины материала, от желаемой формы отверстия, типа металла и требуемой поверхности (с обрамляющим кольцом или без). Ссылочные значения можно найти для трубных профилей рабочая длина пуансона не должна превышать внутренний диаметр профиля.
11. Примеры выбора пуансонов:
• Для создания отверстия в материале Ст 2 пс, сп (S235JR) толщиной 2 мм требуется станок со скоростью 2100 об/мин и выходной мощностью не менее 1.5 кВт. Рекомендуется короткий пуансон ø 7.3 мм, или, если поверхность должна быть гладкая, короткий/торцующий пуансон ø 7.3 мм.
• Для создания такого же отверстия, как описано выше, в металле толщиной 4 мм следует использовать удлиненный или удлиненный/торцующий пуансон. Если возникают проблемы при формовке резьбы, как например скрип метчика или чрезмерный его износ, цилиндрическую часть следует увеличить. Это означает, что должен быть изготовлен специальный пуансон с увеличенным размером цилиндрической части.
• Для создания отверстия как в первом примере, в металле толщиной 2 мм из нержавеющей стали, рекомендуется использовать такой же фасонный пуансон, но диаметром большим на 0. 1 мм, т. е. ø 7.4 мм.
12. Обрамляющее отверстие кольцо представляет проблему. Как можно получить ровную поверхность?
Для этого рекомендуется использовать торцующий пуансон Сenterdrill. В этом случае кольцо удаляется на последнем этапе операции формовки. Конечно, это используется только для заготовок с плоской поверхностью. Для круглой трубы материал остается с двух сторон и может быть удален механическим путем.
13. Резьба формуется за одну операцию вместе с формовкой отверстия?
Нет, если бы резьба производилась во время формовки отверстия, она бы разрушалась вновь при вытягивании пуансона большего диаметра. 22
14. Пуансон становится темно—красным во время формовки? Это опасно? Нет. Обычно пуансон разогревается до тем
Инструмент для сверления и обработки отверстий — Студопедия
Наиболее распространенный режущий инструмент при сверлении–спиральные сверла.
Спиральное сверло (рис. 2.1.2) состоит из рабочей части /, шейки /// и хвостовика IV. В рабочей части в свою очередь различают режущую II и направляющую или центрирующую части.
Рис. 2.1.2. Спиральное сверло
В направляющей части сверла (рис.2.1.3) расположены две канавки 1 и 6 для отвода стружки из просверливаемого отверстия, а также две ленточки 3 и 8 для обеспечения направления сверла при резании.
Режущая часть сверла имеет лве главные режущие кромки 2 и 7,
поперечную кромку 4 и две задние поверхности 5 и 9.
Угол при вершине сверла 2φ, образуемый режущими кромками, выбирают в зависимости от твердости и хрупкости обрабатываемого материала. Для обработки стали и чугуна средней твердости угол при вершине состав-
Рис.2.1.3. Спиральные сверла:
а) обычное, б) с отверстием для подвода охлаждающей жидкости
ляет 116–120°, для красной меди – 125°, для алюминия, мягкой бронзы, латуни – 130–140°.
Угол наклона винтовой канавки ε в зависимости от диаметра сверла принимают 18–30°.
Диаметр спиральных сверл с цилиндрическим и коническим хвостовиками изменяется в пределах 0,25–80 мм. При сверлении можно получить ∆3–∆5-й классы чистоты поверхности и 4–6-й классы точности.
Для дальнейшей обработки отверстий, полученных сверлением, литьем или штамповкой, применяют зенкерование и развертывание.
Зенкерование обеспечивает получение отверстий 3–7-го классов точности и ∆ 5–∆ 6-го классов чистоты; при развертывании получают отверстия 2–3-го классов точности и ∆5–∆9-го классов чистоты.
Рис.2.1.4. Зенкер
Режущим инструментом при зенкеровании и развертывании служат зенкеры и развертки.
Зенкер (рис. 2.1.4) состоит нз рабочей части I, шейки IV, конического хвостовика V и лапки VI. В рабочей части различают режущую II (заборную) и калибрующую III (направляющую) части.
Режущая часть зенкера состоит из срезанной торцовой части – сердцевины 3 и трех или четырех режущих кромок 2. Каждая из них, как и в других инструментах, образована пересечением передней 1 и задней 4 поверхностями. Главный угол в плане φ выбирают в пределах 45–60°.
Калибрующий участок зенкера имеет три или четыре винтовые канавки и ленточки 5. Последние являются направляющими элементами зенкера; они обеспечивают большую точность обработки, препятствуя возможному отклонению инструмента в сторону. Угол наклона винтовых канавок ε – 10–30°.
По виду обрабатываемых отверстий зенкеры разделяют на цилиндрические, конические и комбинированные (многоступенчатые). Кроме цельных диаметром до 80 мм, применяют насадные зенкеры (цельные и со вставными ножами диаметром до 100 мм) и зенкеры с напаянными пластинками из твердых сплавов.
Развертка (рис. 2.1.5,а) имеет рабочую часть I, шейку II и хвостовик III. В рабочую часть входят направляющий конус или заборная часть IV, режущая часть V, калибрующий участок VI и обратный конус VII.
Рис.2.1.5. Развертка
Основную работу выполняет режущая часть, каждый зуб которой имеет главную режущую кромку), переднюю 2 и заднюю 3 поверхности (рис. 2.1.5,6). По передней поверхности сходит срезаемая стружка. Зуб развертки имеет передний угол γ и задний α(рис. 2.1.5,в).
Режущая часть для обработки сквозных отверстий имеет угол, равный для ручной развертки 0,5–1,5°, для машинной развертки при обработке стали 12–15° и чугуна – 3–5°. Главный угол в плане φ влияет на осевое усилие: чем он больше, тем больше потребное осевое усилие.
Развертки бывают цилиндрические и конические, ручные и машинные. У машинных разверток рабочая часть значительно короче, чем у ручных. По конструктивному выполнению развертки делят на хвостовые и насадные, цельные и со вставными ножами, оснащенные пластинками из твердых сплавов.
Спиральные сверла, зенкеры и развертки при небольших скоростях обработки изготовляют из углеродистых инструментальных сталей УЮА и У12А, хромистых и вольфрамовых инструментальных сталей 9ХС и В1, а при больших скоростях обработки – из быстрорежущей стали различных марок. Изготовляют также сверла, зенкеры и развертки, оснащенные пластинками из твердых сплавов марок ВК и ТК.
Монолитные спиральные твердосплавные сверла (из сплавов BK15M, В К 10М и др.) диаметром 1,5–5,5 мм предназначены для сверления труднообрабатываемых материалов. Стойкость таких сверл почти в 20 раз больше стойкости сверл из быстрорежущий стали.
Рис.2.1.6. Комбинированные режущие инструменты:
а) сверло-сверло, б) сверло-зенкер, в)сверло-развертка, г)зенкер-развертка, д)сверло-зенкер-развертка
Комбинированные режущие инструменты (рис. 2.1.6) применяют для повышения производительности при обработке отверстий в массовом производстве. Замена нескольких инструментов одним комбинированным значительно сокращает вспомогательное время (на смену инструмента), улучшает качество обработки, устраняет опасность несовпадения осей инструмента и отверстия и т. д.
Что такое бурение глубоких отверстий
- Английский
- Немецкий
- О UNISIG
- Как купить
- Запросить цену
- Дом
- Английский
- Немецкий
- Продукты и технологии
- Станки
- Все машины
- UNE6 Медицинские сверлильные станки
- UNE Станки для гнутого сверления
- Производственные машины UNI
- BTA серии B,
- BTA серии B, поворотный механизм> 800 мм
- Зачистка и обточка серии S
- Станки с выносным столом USK
- Цилиндрический станок со смещением от центра UNX
- USC-M Фрезерные и сверлильные центры
- Станки для больших столов USC
- Станки для изготовления трубных листов USC-TS
- Развертки UNR
- Нарезные станки серии R
- Машины на заказ
- Автоматизация
- Гибкая автоматизация
- Автоматизация машин
- Индивидуальная автоматизация
- Инструмент
- BTA Tools
- BTA Инструмент длительного пользования
- Бурильные трубы BTA
- Инструменты для гондольных сверл
- Прочная оснастка для перфоратора
- Принадлежности
- Масло для глубокого бурения
- Роторно-шлифовальный станок
- Станки
Осмотр бурового инструмента для забойных скважин на нефтяной скважине
Применение: Обнаружение трещин в поворотных блоках с буртиком (RSC) инструментов для забойного бурения.
Предпосылки: Глубина нефтяных и газовых скважин колеблется от 3500 до 30 000 футов (от 1175 до 10 000 метров) по вертикали. Оборудование для бурения нефтяных скважин подвергается экстремальным условиям, включая растяжение, коррозию и циклические нагрузки, при этом подвергается воздействию повышенных температур и повреждающих газов, захваченных в слоях земли. Из-за нагрузок и механизмов повреждения под воздействием окружающей среды выход из строя бурового инструмента для скважинного бурения (называемого буровой штангой) является обычным явлением.Отказ компонента буровой штанги обычно приводит к огромным расходам из-за суточной стоимости буровой установки, возможной потери компонентов буровой штанги и даже необходимости покинуть нефтяную скважину.
Компоненты бурильной колонны соединяются встык, образуя непрерывную колонну. Это соединение называется «поворотным плечевым соединением» (RSC). Отказ компонентов бурильной колонны обычно происходит в соединении в результате циклических нагрузок, приводящих к возникновению усталостных трещин в точке полного разделения и разделения бурильной колонны в нефтяной скважине.
Область бурильной колонны рядом с буровым долотом известна как «Узел низа бурильной колонны» (КНБК). Это наиболее частый случай сбоя подключения.
Оборудование: Дефектоскоп серии EPOCH (EPOCH 1000, EPOCH 600, EPOCH 650, EPOCH LTC)
Члены семейства OmniScan (OmniScan SX, OmniScan MX)
Контактный датчик V109-RM (5 МГц, диаметр 0,5 дюйма)
Процедура: Это испытание прямым лучом с использованием контактного преобразователя.Продольная волна вводится в конец соединения штифта и муфты, и оператор ищет эхо-сигналы трещин.
Штифтовые и муфтовые соединения изготавливаются с конической конструкцией. Обычные конусы — 2 дюйма и 3 дюйма на фут. При проведении ультразвукового испытания RSC внешний периметр ультразвукового луча используется для обнаружения трещины, распространяющейся от корня резьбы, как показано на рисунках ниже.
Напильник необходим для подготовки поверхности концов штифта и муфты, так как для хорошего контроля необходима гладкая чистая поверхность. Калибровку для этого теста можно выполнить на блоке IIW типа 1.Калибровку диапазона, подходящую для контроля RSC с использованием продольных волн, можно выполнить с использованием ширины 4 дюйма и размера 8 дюймов от квадратного конца до шага 90 градусов. Калибровку чувствительности следует выполнять с использованием эталонных пазов EDM, вырезанных на RSC аналогичного типа и размера. Насечки должны быть размещены в последнем корне резьбы на всю глубину на RSC штифта и муфты.
В дополнение к растрескиванию, ультразвуковой контроль RSC потенциально способен обнаруживать водородные повреждения, включения и аномалии за пределами области резьбы, включая проблемы, вызванные работой или производством.Среди других преимуществ:
• Более быстрый процесс проверки, что сокращает время простоя буровых установок.
• Проверяет внутренний и внешний диаметр соединений штифта и коробки.
• Полная проверка многих скважинных инструментов, таких как утяжеленные бурильные трубы, стабилизаторы и переводники.
Другие процессы проверки, такие как влажные флуоресцентные магнитные частицы, представляют собой только проверку поверхности, обычно применяемую только в области резьбы. WFMT был стандартной практикой инспекции для RSC. Он очень чувствителен к аномалиям разрушения поверхности.Комбинация WFMT и UT — это окончательный тест для RSC.
Сопутствующие испытания: Ультразвуковые испытания могут применяться во многих других областях при бурении нефтяных скважин. К ним относятся осмотр валов, стопорных штифтов и подъемного оборудования, измерение толщины коррозии, обнаружение проникновения воды и проверка сварных швов сосудов под давлением и строительного оборудования.
BTA Станки для глубокого сверления отверстий
Сделать запросЧем мы можем вам помочь?
Буровые мощности БТА
- Цельное сверление до Ø 250 мм
- Расточка до Ø 400 мм
- Глубина сверления до 12000 мм *
Станки BTA для глубокого сверления от TIBO обеспечивают оптимальный метод для больших диаметров сверления от 18 до 250 мм сплошного сверления (до 400 мм зенковки) и глубины сверления до 12 000 мм.
TIBO BTA сверлильный станок для глубоких отверстий B250-8000
Посмотреть видео о сверлильном станке
При использовании метода BTA охлаждающая жидкость вводится и удаляется, а стружка отводится прямо противоположно методу gundrilling: благодаря большему диаметру сверла BTA здесь можно надежно и непрерывно удалять стружку через внутренность инструмента. Охлаждающая жидкость, с другой стороны, вводятся снаружи, так и под давлением через кольцевой зазор между отверстием и отверстием сверлом с помощью головки под давлением охлаждающей жидкости (Boza).
Система BTA | B80 | B125 | B160 | B250 |
---|---|---|---|---|
Ø сверления мм | 10 — 80 * / ** | 25–125 ** | 25–160 ** | 50–250 |
Контр-сверление Ø макс. Мм | 100 | 200 | 250 | 400 |
Глубина сверления макс.мм | 4500 | 12 000 | 12 000 | 12 000 |
Заготовка Ø макс. мм | 500 | 630 | 630 | 825 |
Момент Нм | 600 при n = 140 -1 | 2 000 при n = 180 -1 | 4000 при n = 90 -1 | 7500 при n = 90 -1 |
** Также доступен в конфигурации с двумя шпинделями, по запросу
Метод сверления с эжектором
Вариантом этого является метод эжекторного бурения, при котором масло для глубокого бурения подается через кольцевую камеру между бурильной трубой и внутренней трубой.Смазочно-охлаждающая жидкость выходит сбоку от сверлильной головки, обтекает ее и течет обратно вместе со стружкой во внутренней трубе. В то же время часть охлаждающей смазки подается во внутреннюю трубку через кольцевое сопло. Возникающий в результате разрежение на выходе из стружки обеспечивает возвратный поток (эффект эжектора).
TIBO BTA Станки для глубокого сверления также доступны в одно- или многошпиндельной версии. Выбирая разные редукторы и в зависимости от задачи сверления, можно реализовать разные варианты привода, что позволяет всегда обеспечивать оптимальную производительность резки.
Модульная конструкция и множество дополнительных принадлежностей позволяют использовать дополнительные методы обработки, такие как затачивание, вальцевание, растачивание и растачивание бутылок. Проверенные компоненты и современные инструменты гарантируют высокоточные результаты сверления.
* Возможна глубина сверления более 12000 мм в специальной конфигурации по запросу заказчика
Загрузить брошюру TIBO