- Как из роликовой цепи сделать сверлильную стойку для ручной дрели
- Токарка из сверлильного — Скумекай сам
- Простой сверлильный станок из обыкновенной дрели и подручного хлама
- Самодельный сверлильный станок: подробное описание изготовления
- Простой самодельный сверлильный станок сделанный из дрели своими руками (42 фото)
- Самодельный сверлильный станок | 3dx
- Краткое описание процесса бурения
- 7. Направленное бурение и проходка туннелей | Технологии бурения и земляных работ для будущего
- 411-10.
Как из роликовой цепи сделать сверлильную стойку для ручной дрели
Для быстрого комфортного сверления под прямым углом можно изготовить сверлильную стойку под дрель. Многие детали для этого легко найти на металлоприемке, поэтому себестоимость самоделки в разы ниже заводского аналога.
Основные материалы:
- профильная труба 20 мм;
- двухрядная роликовая цепь;
- звездочка двухрядная;
- уголок 30х30 мм;
- полоса 30 мм;
- прут 6-10 мм;
- болты, гайки;
- пружины растяжения – 2 шт.
Процесс изготовления сверлильной стойки
Из профильной трубы сваривается рамка для подошвы станка.
В нее вваривается 2 перекладины из квадратного прутка.
В качестве стойки станка используется отрезок профильной трубы 40-50 см. К ней приваривается двухрядная роликовая цепь.
Далее нужно сделать каретку с креплением для дрели. Для этого из уголка и полосы сваривается П-образный профиль на стойку.

Из полосы делается 2 проушины с отверстиями. В них вставляется болт со звездочкой. Для исключения проворачивания те свариваются. Если ширины звездочки недостаточно, нужно будет положить по бокам нее шайбы. Проушины привариваются к профилю каретки.
С лицевой стороны каретка заваривается отрезком полосы. По бокам П-профиля привариваются небольшие болты.
Из кольца, срезанного с трубы, делается зажимной хомут на корпус дрели в месте установки ручки. Он приваривается к каретке.
На шляпку болта, удерживающего звездочку, привариваются 3 прутка с оголовьем из шариков подшипника. В точке схождения на них наваривается мелкая звездочка или шайба для жесткости. Получается регулировочное колесо.
Стойка приваривается к подошве под прямым углом. На нее надевается каретка. Вверху стойки просвечивается сквозное отверстие, через которое пропускается шпилька.
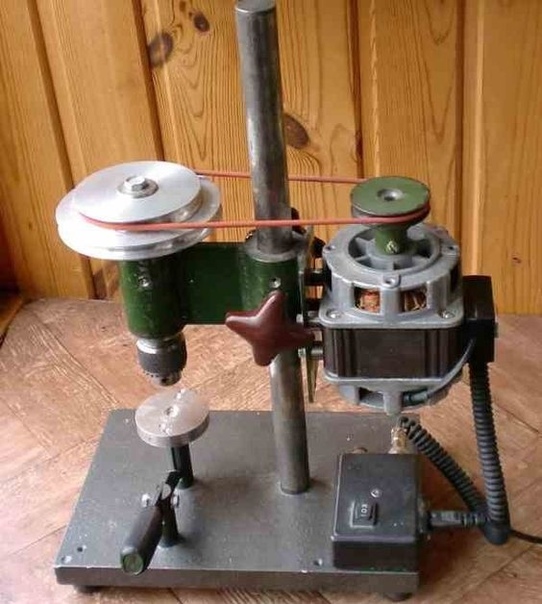
Станок окрашивается. К его подошве прикручивается большая звездочка или же пластина, чтобы получить опорный столик. В хомуте зажимается дрель. Все, сверлильный станок готов к использованию.
Смотрите видео
Токарка из сверлильного — Скумекай сам
Как сделать точеные деревянные детали на сверлильном станке. Для обработки небольших деталей из дерева, вполне подойдет стационарный сверлильный станок. Здесь речь не идет о мощных производственных инструментах, достаточно домашнего сверлильного в 400-800 вт. . Правда чем больше мощность, тем быстрее будет проходить процесс вытачивания изделий.
Для чего можно использовать такой станок.
При работе в домашних условиях, могут понадобиться оригинальные деревянные ручки для мебели, ручки для инструмента, декоративные точеные фрагменты.
Для начала надо провести некоторые подготовительные работы. Цель этих действий, сделать дополнительную точку фиксации детали в нижней части и подготовить захват для фиксации в патроне.
Все эти дополнения съемные и к конструкции самого сверлильного станка отношения не имеют.
В нижней части, на станине станка, необходимо установить площадку с вращающимся конусом.
Площадка — это кусок строганной доски, габаритами около 160/300 мм. и толщиной 35-40 мм. .
Вращающийся конус должен быть на подшипнике, иначе он будет греться и гореть.
Здесь конус сделан из ролика от раздвижной двери, но можно подобрать и другой подходящий вариант из деталей, которые есть под руками.
Под конус выбираем гнездо в площадке и крепим ролик саморезами. Кроме того на нижней площадке надо установить упор для резаков.
Верхний зубчатый захват так же делаем из шпильки. На нижнем конце пропиливаем и протачиваем напильником зубцы, для надежного удержания детали. Дополнительно на шпильку навернута гайка, она так же фиксирует деталь.
Как один из вариантов, можно взять старое сверло-коронку небольшого диаметра, зажать в патрон и им фиксировать деталь сверху. Правда эти сборные коронки часто раскручиваются, поэтому лучше позаботиться о надежности приспособления. Коронка пригодится для другой работы, сделать кольцо из дерева.
Перед работой необходимо точно выставить площадку на станине и зафиксировать струбцинами.
Для центровки зажимаем в патрон длинное сверло и подгоняем так, чтобы центры сверла и конуса совместились.
На деревянной заготовке сверлим в верхнем торце гнездо по диаметру шпильки, глубиной 12-15 мм. . Это надо сделать обязательно, чтобы деталь при работе не могла выскочить.
Деталь устанавливаем на шпиндель и опускаем суппорт станка, пока верхняя шпилька полностью не войдет в углубление на верхнем торце детали и не врежется зубцами в древесину.
Затем окончательно зажимаем навернутой сверху гайкой.
Токарка на сверлильном будет работать медленнее, чем специализированный инструмент, все таки оборотов на сверлильном меньше. Но спокойно, не торопясь можно выточить любую нужную по форме деталь. Сильно давить на резак не стоит, выдавите деталь и испортите свое приспособление.
Есть ещё один вариант такой работы, он может использоваться для обтачивания круглых плоских деталей.
В этом случае по центру деревянной заготовки сверлится отверстие, и деталь зажимается на шпильке гайками сверху и снизу. Сама шпилька зажимается в патроне сверлильного станка. Но и здесь понадобится вертикальный упор для резаков, который собирается так же, на плоской площадке фиксируется гайками болт или шпилька.
Идея с сайта instructables.com
(Visited 242 times, 1 visits today)
Похожие статьи
Простой сверлильный станок из обыкновенной дрели и подручного хлама
Доброго времени суток любители помастерить что-либо своими руками. В сегодняшней статье мы рассмотрим, как сделать крутой молдинг для обыкновенной дрели. Данная самоделка превращает обыкновенную дрель в сверлильный станок. Сама по себе самоделка отличается от других подобных таких же самоделок тем, что в ней осуществлена система подъёма и опускания за счет вращения рукоятки, самым простым способом. Подобные заводские вещи стоят довольно дорого, а данную самоделку при наличии необходимого количества инструмента можно вообще собрать практически за бесплатно. Как уже упоминалось, сама по себе конструкция очень и очень просто, и каких-либо проблем при сборке ни у кого возникнуть не должно. Ну, что ж, думаю не стоит тянуть с длинным предисловием, погнали.

Для данного аксессуара для обыкновенной дрели понадобится следующее, а именно:
— Квадратный металлический профиль
— Металлический уголок
— Лист толстого металла
— Болты
— Гайки
— Металлическая втулка
— Прямоугольный металлический профиль
— Металлический шарик (от подшипника)
— Металлический стержень
— Шпилька
— Металлический трос в силиконовой изоляции
— Зажимы для троса
— Эмалевая краска (для защиты самоделки от коррозии)
Из инструментов также понадобиться следующее:
— Дрель со всеми необходимыми сверлами
— Болгарка с отрезными и шлифовальными дисками
— Сварочный аппарат со всеми сварочными принадлежностями
— Гаечные ключи
— Пассатижи
— Строительный уголок
— Маркер
Изготовление насадки на дрель:
Изготовление нашей самоделки начинаем с изготовления основания данной самоделки. Для него понадобится квадратная металлическая профильная труба, примерно таким же диаметром как труба, взятая автором самоделки.

Разрезав профильную трубу на несколько отрезков, эти отрезки необходимо соединить между собой так, чтобы в итоге у нас получился прямоугольник. Для того чтобы у нас получился прямоугольник с одинаковыми прямыми углами необходимо использовать специальный строительный уголок. Свариваем заготовки между собой хорошо проворив все места соединения. Проварив все заготовки зашлифовываем сварные швы так, чтобы заготовка приняла вид монолитной детали.
Следующим шагом необходимо усилить нашу прямоугольную конструкцию, для того чтобы её не повело во время эксплуатации. Для этого необходимо из того же куска профильной металлической трубы отрезать пару отрезков такой длины, чтобы они плотно садились внутрь прямоугольной заготовке. Вставляем отрезки в заготовку так как это изображено на картинке ниже и привариваем их.
Далее изготовим движущуюся часть конструкции. Эта самая часть у нас будет двигаться вверх и вниз по направляющей. В качестве направляющей будем использовать ту же саму квадратную профильную трубу. Так вот, наша движущиеся часть должна быть такой чтобы она сидела на направляющей с минимальным зазором. Для изготовления такой движущей части возьмём металлический уголок, который распилим на две равные части.
Две одинаковые части металлического уголка необходимо соединить между собой так, чтобы образовалась квадратная профильная труба, для того чтобы не ошибиться с размерами прикладываем уголки к трубе так как это изображено на фото ниже, отмечаем маркером выступающую часть уголков и отпиливаем её болгаркой. После того как подготовили уголки их необходимо соединить между собой образовав квадратную трубу. Свариваем их между собой проваривая все места соединения.
Продолжаем работу над нашей движимой частью. Для следующего шага понадобится лист толстого металла. От этого металлического листа необходимо отпилить пару одинаковых прямоугольников, размером примерно 3*5см. С краю каждой заготовки необходимо проделать сквозные отверстия (так, чтобы эти отверстия располагались ровно параллельно относительно друг друга).
Только что изготовленные заготовки необходимо приварить к движущейся заготовке. Привираем перпендикулярно движущейся части к её бокам (по их центру), проделанные отверстия должны быть параллельны относительно друг друга, так как в этих отверстиях будет усыновлен болт.
Следующим шагом нужно собрать вращающуюся ось, благодаря которой будет осуществляться подъём и опускание движущейся части. В качестве самой оси будем использовать болт либо шпильку подходящего диаметра. На взятый болт или шпильку необходимо подобрать втулку, на саму втулку будем наматывать трос. Длина втулки должна быть такой, чтобы она помещалась между приваренными к движимой части деталям.
Берём болт просовываем его в первое отверстие, надеваем подобранную втулку на болт и затем просовываем болт через второе отверстие, закрепляем болт на своем посадочном месте закрутив на его конец гайку через шайбу. Для того чтобы втулка, надетая на болт, не проворачивалась её необходимо приварить к самому болту. Для этого автор самоделки проделал отверстие во втулке (не на сквозь болта), и в этом месте поставил сварную точку.
Переходим к изготовлению крепления дрели. Тут уже работа индивидуальна, так как дрели существуют разные и способ их крепления придётся выдумывать разные. Но все же, большинство средне бюджетных моделей имеют крепление под дополнительную рукоятку, устанавливаемую возле сверлильного патрона. Так вот для изготовления подобного крепления необходимо раздобыть небольшой кусок прямоугольной металлической профильной трубы.
Нам следует отрезать от имеющегося куска прямоугольной металлической трубы отрезок длиной около 10-15см. С краю этого отрезка проделываем отверстие, диаметр которого должен быть равен диаметру места крепления рукоятки на дрели. Проделав отверстие необходимо осуществить работу механизма крепления, для этого проделываем пропил в указанном на фото месте.
Затем привариваем крепление дрели к движимой части с обратной стороны от болта с втулкой. Для большей жесткости и надежности конструкции автор самоделки решил добавить дополнительный упор для крепления (см. фото).
Для работы нашего механизма необходимо изготовить рукоятку для вращения втулки. Автор самоделки в качестве рукоятки использовал металлический стержень (который заранее загнул), на конец этого стержня для того чтобы не обрезаться об острые грани, он приварил большой металлический шарик от шарикового подшипника. Рукоятку привариваем к болту установленному на движимой части.
Возьмём нашу направляющую, что подготовили ранее, эту самую направляющую необходимо закрепить на основание, которое мы также уже изготовили ранее. Но перед тем как это сделать, на один из концов этой направляющей необходимо приварить болт с гайкой. Они нужны для крепления троса. Для этого повторяем действия с изображения ниже. И уже только после этого привариваем направляющую к основанию.
Приварив направляющую к основанию, необходимо приварить ещё один болт для крепления троса, а именно в нижнюю часть, к основанию в указанное на фото место. Затем устанавливаем нашу движущееся часть на направляющую. И переходим к завершающему шагу.
На данном этапе автор самоделки решил покрасить самоделку дабы защитить её от воздействия коррозии, что делать совсем не обязательно, но конечно же желательно бы сделать это. Покрасив самоделку делаем следующее, а именно берём трос и зажимы для него. Заматываем трос на конструкцию так как это изображено ниже.
Все готово! В итоге у нас получилась полезная самоделка для любого гаража и любой мастерской. Что вам остается сделать так это вставить дрель в крепление и начинать сверлить.
Вот видео автора самоделки:
youtube.com/embed/Tfo-QQRuwK8?start=571&feature=oembed» frameborder=»0″ allow=»accelerometer; autoplay; encrypted-media; gyroscope; picture-in-picture» allowfullscreen=»»/>
Ну и всем спасибо за внимание и удачи в будущих проектах самодельщики!
Источник (Source) Становитесь автором сайта, публикуйте собственные статьи, описания самоделок с оплатой за текст. Подробнее здесь.
Самодельный сверлильный станок: подробное описание изготовления
Подробное описание изготовления сверлильного станка из дрели.
Приветствую всех самоделкиных! Думаю, все кто пользовался электродрелью сталкивался с трудностями, когда необходимо сделать кучу отверстий. Пол беды если отверстия в доске, а дырявить металл? Для этого промышленность придумала сверлильный станок. У кого он есть, тем крупно повезло, а у кого нет — готовь карман.
Карман, лично у меня маленький, поэтому позволить заводской сверлильный станок я не в силах. Ну китайский, из жести, я конечно могу позволить, но ведь оно фигня фигней. Советские, полу комплектные, стоят неоправданно дорого.
Магазинные стойки для дрелей не рассматривал в принципе, уж больно «детские» они. Блуждая по интернету находил много самоделок, но останавливало наличие токарных работ. Пару деталей заказать у токаря можно, но нормальными чертежами делится никто не хочет, а когда конструируешь деталь сам всегда вылезет косячок. Вылез косяк — беги опять к токарю и проси поправить. Но однажды я наткнулся на интересное видео про самодельную стойку для дрели. Простая конструкция, повторяемая и универсальная.
В конструкцию внес свои корректировки, они принципиально не меняют станок, но унифицируют материалы и сокращают время изготовления некоторых элементов. Я постарался использовать минимальное количество покупного материала, старался использовать тот мусор который у меня был. Но без покупок все равно не обошлось. Из основного я докупил трубу для направляющей, уголок и полосу, каждой позиции по 1 метру.
Теперь смотрим процесс изготовления. Собственно, направляющая для каретки у меня выполнена из квадратной трубы 40 х 40 х 3 мм. Железо я покупал в маленьком строительном магазинчике, металлопрокат там хранится практически под открытым небом и не особо блещет качеством. Но в этом есть одно преимущество, там можно все пощупать и выбрать получше. Так и произошло. С начала хотел взять трубу с толщиной стенки 2 мм, но ровный кусок нам с продавцом выбрать не удалось. Взял с толщиной стенки 3 мм, толстостенные трубы гораздо ровнее. Сталь есть сталь и следы коррозии неотъемлемая ее составляющая. Поэтому почти весь прокат мне пришлось чистить, в особенности направляющую. Доводить до состояния кошачьей гордости я не стал.
Уголок для каретки и кронштейна я взял 45 х 45 х 4 мм. В него прекрасно ложится труба 40 х 40 мм, ничего подрезать не надо и образуется отличный монтажный зазор (видно на фото ниже).
Подложил наждачку, обжал струбцинами на направляющей, заварил все от души. А снять потом фигушки, зажимает так, что «мама не горюй»! Кронштейн стойки я смог снять только сбивая его об остаток 45-го уголка. Далее я порезал весь уголок, сварил каретку, подложил в два раза больше наждачки и все…. Сколько было потрачено матерных слов, выкурено сигарет и проклято всего, что рядом шевелилось уже не вспомнить, а отделить одно от другого не получилось.
А технология по моему мнению должна быть такова: кладем в двойне сложенную наждачку —> обжимаем струбцинами —> прихватываем сваркой кромки по всем четырем углам —> полностью провариваем одну из кромок —> даем полностью остыть —> пытаемся снять с оправки. Если сошло с оправы, то провариваем вторую кромку. Если не идет, тогда срезаем прихватки на непроваренной кромке и легонечко извлекаем направляющую. На фото ниже лежат уже сваренные заготовки, самая маленькая использоваться не будет.
Станину сделал из того, что было. А было у меня почти метр швеллера 8. Длину станины подогнал под длину остатка квадратной трубы, который осталась после изготовления направляющей. Ниже картинка процесса установки кронштейна стойки. Если честно, то такая конструкция станины не сильно хорошая. Полки у швеллера все кривые, у одного куска вогнутость, у другого выпуклость. Жуть, а не прокат. Сделал вид, что выставил под прямым углом, правда непонятно к какой плоскости. С перпендикулярностью я буду бороться позже
В задней панели выполнено два отверстия с резьбой. Эти отверстия будут служить для закрепления станка в горизонтальном положении при обработке дерева.
И крепежные элементы для закрепления стойки в вертикальном положении. Одинокий болт приварен для организации заземления.
О регулировочных ножках. Стандартных ножек от холодильника или стиралки, по какой-то случайности не оказалось, прям диву даюсь. Пришлось делать из болта и увеличенной шайбы, цена вопроса — пару копеек. А вот те штуки в которую ножки закручиваются у меня были, но в место них отлично подойдут высокие гайки.
Барабан, тот, который будет прокручивать трос.
К изготовлению этой детали я подошел творчески. Работает он точно так же, но выполнен по другому. Стальные прутки диаметром больше 10 мм в домашнем сарае найти сложно и мой сарай не исключение. Плюс сразу решил вопрос съемной рукоятки. В качестве оси применил болт М10 с короткой ГОСТовской резьбой. Отрезав от него лишнее получил гладкую ось.
Шляпка болта будет служить неким элементом зацепления оси с рукояткой. Внешней частью барабана будет служить водопроводная труба. Если у Вас в металлическом мусоре нет такой трубы, то ее можно заменить сгоном, купленным в ближайшем сантехническом магазине. Для центровки оси пришлось изготовить втулки, так сказать, ручным методом, без токарного станка.
Для этого зажал две гайки М10 на оставшемся обрезке болта (обрезок не выбрасывайте, он потом пригодится), вставил в дрель и обточил всю конструкцию на электроточиле. Так как резьбы на обрезке болта уже нет, то и резьбу во втулках тоже надо высверлить. В головке болта выполнено отверстие с резьбой М5 для крепления рукоятки. Получилось довольно неплохо. На картинке ниже я уже приварил втулки к оси, главное не забыть сперва одеть одну из проушин. В наружной обойме барабана выполнены отверстия, через которые обойма будет привариваться ко втулкам. Все размеры и зазоры указаны в чертежах.
Каретка. Тут рассказывать особо нечего, собираем все по чертежам. Только одно дополнение. В оригинале каретка стопориться одним из регулировочных болтов. Они ведь на то и регулировочные, чтобы их не трогать, поэтому после приварки всех деталей я сделал дополнительное отверстие с резьбой именно для стопорного болта. Резьбу под регулировочные болты я выполнил только черновым метчиком, что бы избавится от самопроизвольного раскручивания.
Рукоятка, она же рычаг. Посмотрев на фотографию не бросайте помидорами. В моем исполнении рычаг выполнен из рожково- накидного ключа на 17. У него был лопнувший накидок, поэтому недоключу я дал вторую жизнь.
Данный упор крепится в верхней части направляющей стойки и используется при закреплении станка в горизонтальном положении. Отверстия для крепления к стойке выполнены не соосно для минимизации проворачивания упора.
Еще ода новая деталь. Я назвал ее «стол». Так как плоскость у моей станины отсутствует, пришлось изворачиваться. Сделан он из куска ламинированного ДСП, не лучший вариант, но пока так. С помощью винтов у меня есть возможность выставить рабочую плоскость перпендикулярно стойке.
Пришло время изготовить кронштейн для крепления дрели. И опять в ход пошли материалы которые у меня были. Хомут из полосы 25 х 4 мм, вынос из трубы 30 х 30 х 2 мм. Данная полоса отлично помещается внутрь трубы, что упрощает крепление одного с другим. А данный разворот хомута обеспечивает идеальную соосность. Хомут изготовлен обстукиванием полосы вокруг трубы диаметром 40 — 42 мм.
Дрель мне подарили как не рабочую. Внутри был просто передавлен провод и со временем в этом месте он сгорел. Провод поправил, но дрель, как видно, очень уставшая и полна люфтов. Первым делом под замену пошел патрон и подшипники качения. Втулка хвостовика тоже была разбитая.
Если честно, я бы руки оторвал этим конструкторам, которые в простую дрель добавили функцию трещотки. Толку ноль, подшипники разбивает и добавляет ко всем прелестям осевой ход патрона. Самое интересное, по крайней мере в этой дрельке, видно, что трещоточный узел по размерам совпадает с наружной обоймой подшипника №608.
Мои попытки выбить трещотку из силуминовой обоймы увенчались неудачей, пришлось зубцы срезать ножовкой и идти на рынок искать бронзовую втулку. А на рынке за эту втулочку заломили несуразную цену, на что я сильно обиделся и принципиально ушел не с чем. В место бронзовой золотой втулки по размерам отлично подходит внутренняя обойма от того же 608-го подшипника. Одно плохо — эта замена одноразовая, в следующий раз придется менять втулку вместе с валом патрона. Посмотрим сколько проживет.
Для ликвидации осевого хода вала вместо отталкивающей пружины установил втулку, изготовленную из сантехнического фитинга, а с другой стороны подложил обточенную шайбу. Подшипники заменены, люфты ликвидированы, механизмы смазаны.
Так как эта дрель специально была припасена для станка я постарался сделать так, чтобы она могла работать только в этом станке. Я обрезал рукоятку. От варвар… Кнопка пуска была извлечена, рычаг реверса остался на родном месте, срез прикрыл аккуратной крышечкой.
Кнопку я разместил в полости станины, в передней панели выполнил отверстие с резьбой и закрутил туда регулировочный винт. Таким образом получил вынесенный узел регулировки оборотов. Закручиваешь винт, он постепенно вжимает кнопку которая изменяет обороты дрели. Отдельно смонтировал тумблер включения станка.
Запечатлен процесс сборки кронштейна шпинделя. В патрон закрепил направляющую от принтера, что позволило относительно точно выставить ось инструмента перпендикулярно столу.
Вот и обваренный кронштейн. Сразу же сделал отверстие в столе и станине. В станине нарезал резьбу для вкручивания центра для удержания деревянной заготовки при токарных работах. Потом принялся заготавливать детали для изготовления подручника (Подручник — подставка для режущего инструмента на токарном станке).
И в принципе станок готов, для теста была выбрана практически максимальная нагрузка. Первое серьезное отверстие выполнено сверлом 13 мм в лицевой панели станка для установки тумблера, напомню, панель сделана из полосы толщиной 4 мм. Результат превзошел все ожидания, без предварительного засверливания и минимум усилий, даже не напрягся, просверлил отверстие за считанные секунды. Порадовался я, состояние эйфории прошло и в глаза начали бросаться благородные следы молодой ржавчины. Все спешил собрать и не удосужился покрасить подетально. Придется теперь все разбирать.
Получился вот такой самодельный сверлильный станок из дрели.
А вот самоделка в положении токарного станка:
Простой самодельный сверлильный станок сделанный из дрели своими руками (42 фото)
Простой и практичный самодельный сверлильный станок, сделанный из дрели своими руками: подробные пошаговые фото по изготовлению станка.
Приветствую всех самоделкиных! В этой статье, мы с вами подробно рассмотрим, как сделать насадку, на дрель, превращающую её в самый настоящий сверлильный станок.
Подобные «насадки» на дрели делали многие, но отличительной чертой данной самоделки является то что, дрель не просто подвешена на пружине, а ещё и опускается благодаря шестерёночному приводу, что создает редукцию и в разы упрощает её эксплуатацию.
Для изготовления самодельного сверлильного станка понадобятся материалы:
- — Электродрель.
- — Цепь (велосипедная или мотоциклетная).
- — Звёздочки для цепи.
- — Прямоугольный металлический профиль.
- — Металлические стержни.
- — Квадратный металлический профиль.
- — Металлический уголок.
- — Металлическая пластина.
- — Болты, гайки и шайбы.
- — Металлическая труба.
- — Шпильки или круглые стержни (для рукояток).
- — Пружины.
- — Эмаль краска.
Начинаем со сборки основания станка. Основание соберём из прямоугольного металлического профиля. Из профиля необходимо сварить прямоугольник с размерами примерно таким же, как на фото ниже. Для того чтобы все выглядело аккуратно прямоугольники необходимо отпиливать под углом 45 градусов.
Далее к нашему металлическому прямоугольному основанию необходимо приварить пару распорок. Эти распорки будут служить в роли опоры для стола или предметов, которые будут лежать на них при сверлении. Распорки вырезаем из металлических стержней их необходимо минимум 2 шт. Привариваем их так, чтобы они располагались ровно параллельно относительно друг дуга и были смещены к одной из грани, автор для этого подложил другие отрезки стержней
Для изготовления каретки, понадобится цепь и звёздочки к ней. В нашем конкретном случае не важен размер цепи, главное чтобы звёздочка к ней подходила. От количества зубцов на звёздочке, зависит степень редукции будущего инструмента, чем она больше, тем аккуратней и легче можно будет проделывать отверстие. Так как автор использовал старую цепь, перед её использованием он её хорошенько промыл, если же у вас тоже старая ржавая цепь, то желательно сделать также.
Из куска квадратной трубы, изготовим вертикальную колонну.
К трубе нужно приварить цепь. Стоит отметить то, что использование двух цепей в нашей конструкции будет более правильными решением, так как под нагрузкой движущийся механизм будет менее заламываться. Привариваем цепь и обязательно зашлифовываем сварные швы.
Приступаем к изготовлению передвижной каретки.
Изготавливаем крепление дрели. Дрель у нас будет крепиться за то место, где крепится дополнительная рукоятка. То есть необходимо изготовить, что-то подобное хомуту. Для этого возьмём трубу подходящего диаметра, отпилим от него колечко. Зачем это колечко распилим и на место спила параллельно приварим две гайки. В эти гайки будем вставлять болт и с его помощью затягивать хомут, тем самым закрепив дрель.
Далее привариваем только что изготовленный хомут к движущейся части, в место указанное на фото ниже.
В завершении остается изготовить удобную рукоятку для вращения шестерни. Рукоятку автор изготовил из металлических стержней, приварив их к шляпке болта.
Покраска и сборка.
Вот такой самодельный сверлильный станок с самой простой конструкцией, значительно облегчит процесс сверления заготовок.
Процесс изготовления сверлильного станка, также показан в этом видео:
Самодельный сверлильный станок | 3dx
Те, кто хоть раз пользовался электродрелью сталкивался с трудностями, когда необходимо сделать кучу отверстий. Пол беды если отверстия в доске, а дырявить металл? Для этого промышленность придумала сверлильный станок. У кого он есть, тем крупно повезло, а у кого нет — готовь карман.
Карман, лично у меня маленький, поэтому позволить заводской сверлильный станок я не в силах. Ну китайский, из жести, я конечно могу позволить, но ведь оно фигня фигней. Советские, полу комплектные, стоят неоправданно дорого. Магазинные стойки для дрелей не рассматривал в принципе, уж больно «детские» они. Блуждая по интернету находил много самоделок, но останавливало наличие токарных работ. Пару деталей заказать у токаря можно, но нормальными чертежами делится никто не хочет, а когда конструируешь деталь сам всегда вылезет косячок. Вылез косяк — беги опять к токарю и проси поправить. Но однажды я наткнулся на интересное видео от Zhelezjaka про самодельную стойку для дрели. Простая конструкция, повторяемая и универсальная. В момент просмотра видео от Zhelezjaka аналогов этой конструкции еще не было.
Собирался я сделать эту стойку целый год, а может и больше. Уйдя в отпуск я наконец приступил к работе. В конструкцию внес свои корректировки, они принципиально не меняют станок, но унифицируют материалы и сокращают время изготовления некоторых элементов. Я постарался использовать минимальное количество покупного материала, старался использовать тот мусор который у меня был. Но без покупок все равно не обошлось. Из основного я докупил трубу для направляющей, уголок и полосу, каждой позиции по 1 метру.
Теперь смотрим процесс изготовления. Собственно, направляющая для каретки у меня также выполнена из квадратной трубы 40х40х3 мм. Железо я покупал в маленьком строительном магазинчике, металлопрокат там хранится практически под открытым небом и не особо блещет качеством. Но в этом есть одно преимущество, там можно все пощупать и выбрать получше. Так и произошло. С начала хотел взять трубу с толщиной стенки 2 мм, но ровный кусок нам с продавцом выбрать не удалось. Взял с толщиной стенки 3 мм, толстостенные трубы гораздо ровнее. Сталь есть сталь и следы коррозии неотъемлемая ее составляющая. Поэтому почти весь прокат мне пришлось чистить, в особенности направляющую. Доводить до состояния кошачьей гордости я не стал.
Забыл сказать, заранее я заготовил комплект предварительных чертежей, по которым и делал базовые элементы. Комплект окончательных чертежей будет выложен в конце статьи. Режим заготовки в размер. Вот первое отступление от авторского проекта, уголок для каретки и кронштейна я взял 45х45х4 мм. В него прекрасно ложится труба 40х40, ничего подрезать не надо и образуется отличный монтажный зазор (видно на фото ниже). Технологию изготовления пытался повторить авторскую.
Подложил наждачку, обжал струбцинами на направляющей, заварил все от души. А снять потом фигушки, зажимает так, что «мама не горюй»! Кронштейн стойки я смог снять только сбивая его об остаток 45-го уголка. Далее я порезал весь уголок, сварил каретку, подложил в два раза больше наждачки и все…. Сколько было потрачено матерных слов, выкурено сигарет и проклято всего, что рядом шевелилось уже не вспомнить, а отделить одно от другого не получилось. Как у автора все так просто, я не знаю. А технология по моему мнению должна быть такова: кладем в двойне сложенную наждачку —> обжимаем струбцинами —> прихватываем сваркой кромки по всем четырем углам —> полностью провариваем одну из кромок —> даем полностью остыть —> пытаемся снять с оправки. Если сошло с оправы, то провариваем вторую кромку. Если не идет, тогда срезаем прихватки на непроваренной кромке и легонечко извлекаем направляющую. На фото ниже лежат уже сваренные заготовки, самая маленькая использоваться не будет.
Станину сделал из того, что было. А было у меня почти метр швеллера 8. Длину станины подогнал под длину остатка квадратной трубы, который осталась после изготовления направляющей. Ниже картинка процесса установки кронштейна стойки. Если честно, то такая конструкция станины не сильно хорошая. Полки у швеллера все кривые, у одного куска вогнутость, у другого выпуклость. Жуть, а не прокат. Сделал вид, что выставил под прямым углом, правда непонятно к какой плоскости. С перпендикулярностью я буду бороться позже.
Обварил и добавил еще пару деталюх: ножки, заготовку передней панели
и задней. В задней панели выполнено два отверстия с резьбой. Эти отверстия будут служить для закрепления станка в горизонтальном положении при обработке дерева.
И крепежные элементы для закрепления стойки в вертикальном положении. Одинокий болт приварен для организации заземления. Отверстий под провода здесь не видно, но в чертежах они есть.
О регулировочных ножках. Стандартных ножек от холодильника или стиралки, по какой-то случайности не оказалось, прям диву даюсь. Пришлось делать из болта и увеличенной шайбы, цена вопроса — пару копеек. А вот те штуки в которую ножки закручиваются у меня были, но в место них отлично подойдут высокие гайки.
Барабан, тот, который будет прокручивать трос. К изготовлению этой детали я подошел творчески. Работает он точно так же, но выполнен по другому. Стальные прутки диаметром больше 10 мм в домашнем сарае найти сложно и мой сарай не исключение. Плюс сразу решил вопрос съемной рукоятки. В качестве оси применил болт М10 с короткой ГОСТовской резьбой. Отрезав от него лишнее получил гладкую ось. Шляпка болта будет служить неким элементом зацепления оси с рукояткой. Внешней частью барабана будет служить водопроводная труба. Если у Вас в металлическом мусоре нет такой трубы, то ее можно заменить сгоном, купленным в ближайшем сантехническом магазине. Для центровки оси пришлось изготовить втулки, так сказать, ручным методом, без токарного станка. Для этого зажал две гайки М10 на оставшемся обрезке болта (обрезок не выбрасывайте, он потом пригодится), вставил в дрель и обточил всю конструкцию на электроточиле. Так как резьбы на обрезке болта уже нет, то и резьбу во втулках тоже надо высверлить. В головке болта выполнено отверстие с резьбой М5 для крепления рукоятки. Получилось довольно неплохо.
На картинке ниже я уже приварил втулки к оси, главное не забыть сперва одеть одну из проушин. В наружной обойме барабана выполнены отверстия, через которые обойма будет привариваться ко втулкам. Все размеры и зазоры указаны в чертежах.
Вот результат:
Каретка. Тут рассказывать особо нечего, собираем все по чертежам. Только одно дополнение. В оригинале каретка стопориться одним из регулировочных болтов. Они ведь на то и регулировочные, чтобы их не трогать, поэтому после приварки всех деталей я сделал дополнительное отверстие с резьбой именно для стопорного болта. Резьбу под регулировочные болты я выполнил только черновым метчиком, что бы избавится от самопроизвольного раскручивания.
Вид с другой стороны. Извиняйте за мои сварные швы, как умею, так и варю.
Рукоятка, она же рычаг. Посмотрев на фотографию не бросайте помидорами. В моем исполнении рычаг выполнен из рожково- накидного ключа на 17. У него был лопнувший накидок, поэтому недоключу я дал вторую жизнь.
С одной стороны, на накидную часть ключа наварил самодельную шайбу из полосы.
Далее элемент которого нет в оригинальной конструкции — это упор. Данный упор крепится в верхней части направляющей стойки и используется при закреплении станка в горизонтальном положении. Отверстия для крепления к стойке выполнены не соосно для минимизации проворачивания упора.
Еще ода новая деталь. Я назвал ее «стол». Так как плоскость у моей станины отсутствует, пришлось изворачиваться. Сделан он из куска ламинированного ДСП, не лучший вариант, но пока так. С помощью винтов у меня есть возможность выставить рабочую плоскость перпендикулярно стойке.
Вот так это выглядит. На фото так же попала вспомогательная каретка, на которой будет размещаться линейка и подручник для деревообработки.
А тут видно элемент регулировки стола.
Пришло время изготовить кронштейн для крепления дрели. И опять в ход пошли материалы которые у меня были. Хомут из полосы 25х4 мм, вынос из трубы 30х30х2. Данная полоса отлично помещается внутрь трубы, что упрощает крепление одного с другим. А данный разворот хомута обеспечивает идеальную соосность. Хомут изготовлен обстукиванием полосы вокруг трубы диаметром 40 — 42 мм.
Немного ближе.
И аккуратненько завариваем. Я переживал за качество этих швов, так как это место самое слабое во всей конструкции.
На время отложим сварочник и займемся дрелью. Как я уже говорил, станок я собирался сделать целый год. За это время обзавелся дрелью, которую не жалко. Мне ее подарили как не рабочую. Внутри был просто передавлен провод и со временем в этом месте он сгорел. Провод поправил, но дрель, как видно, очень уставшая и полна люфтов. Первым делом под замену пошел патрон и подшипники качения. Втулка хвостовика тоже была разбитая.
Если честно, я бы руки оторвал этим конструкторам, которые в простую дрель добавили функцию трещотки. Толку ноль, подшипники разбивает и добавляет ко всем прелестям осевой ход патрона. Самое интересное, по крайней мере в этой дрельке, видно, что трещоточный узел по размерам совпадает с наружной обоймой подшипника №608. Мои попытки выбить трещотку из силуминовой обоймы увенчались неудачей, пришлось зубцы срезать ножовкой и идти на рынок искать бронзовую втулку. А на рынке за эту втулочку заломили несуразную цену, на что я сильно обиделся и принципиально ушел не с чем. В место бронзовой золотой втулки по размерам отлично подходит внутренняя обойма от того же 608-го подшипника. Одно плохо — эта замена одноразовая, в следующий раз придется менять втулку вместе с валом патрона. Посмотрим сколько проживет. Для ликвидации осевого хода вала вместо отталкивающей пружины установил втулку, изготовленную из сантехнического фитинга, а с другой стороны подложил обточенную шайбу. Подшипники заменены, люфты ликвидированы, механизмы смазаны.
Внимание, слабонервным просьба не смотреть на следующую картинку! Так как эта дрель специально была припасена для станка я постарался сделать так, чтобы она могла работать только в этом станке. Я обрезал рукоятку. От варвар… Кнопка пуска была извлечена, рычаг реверса остался на родном месте, срез прикрыл аккуратной крышечкой.
И что я получил в итоге. Кнопку я разместил в полости станины, в передней панели выполнил отверстие с резьбой и закрутил туда регулировочный винт. Таким образом получил вынесенный узел регулировки оборотов. Закручиваешь винт, он постепенно вжимает кнопку которая изменяет обороты дрели. Отдельно смонтировал тумблер включения станка.
Ниже запечатлен процесс сборки кронштейна шпинделя. В патрон закрепил направляющую от принтера, что позволило относительно точно выставить ось инструмента перпендикулярно столу.
Вот и обваренный кронштейн. Сразу же сделал отверстие в столе и станине. В станине нарезал резьбу для вкручивания центра для удержания деревянной заготовки при токарных работах. Потом принялся заготавливать детали для изготовления подручника (Подручник — подставка для режущего инструмента на токарном станке).
А вот он и готовый. Он получился упрощенной функциональности, регулировки по высоте нет. Я никогда в жизни не работал на токарнике по дереву, и пометаллу тоже, буду учится и пробовать.
И в принципе станок готов, для теста была выбрана практически максимальная нагрузка. Первое серьезное отверстие выполнено сверлом 13 мм в лицевой панели станка для установки тумблера, напомню, панель сделана из полосы толщиной 4 мм. Результат превзошел все ожидания, без предварительного засверливания и минимум усилий, даже не напрягся, просверлил отверстие за считанные секунды. Порадовался я, состояние эйфории прошло и в глаза начали бросаться благородные следы молодой ржавчины. Все спешил собрать и не удосужился покрасить подетально. Придется теперь все разбирать.
Я как всегда дождался похолодания, чтоб начать покраску. Поэтому пришлось красить в сарае, удовольствие не из приятных, красьте на улице. Я выбрал зеленый цвет, эта ассоциация еще с детства — если станок, то зеленый.
Покраска станины. Лень было провод вынимать, колхоз так колхоз.
Краска высохла и вот результат работ:
С другой стороны:
И в положении токарного станка:
Вот и обещанные чертежи. Всех нормоконторолеров и сильно умных прошу чертежи не комментировать, и даже не смотреть :)) шутка. Пользуйтесь на здоровье! Я даже составил спецификацию по которой можно прикинуть объем необходимых материалов. Но должен предупредить, не верьте слепо чертежам, перепроверяйте, я не робот и могу иногда ошибаться.
В результате получился отличный инструмент. В полной мере оценить токарный вариант я пока не могу, так как в место резцов у меня есть только стамеска. Но в качестве сверлилки присутствует пару «но»:
- Старайтесь сделать станину как у автора Zhelezjaka, конструкция будет проще, легшие и ровнее.
- Одно плечевая рукоятка жутко неудобная, объяснить трудно в чем неудобность, но неудобно. Я буду переделывать в трех плечевую. В моем варианте это просто, открутил одну и прикрутил другую. Если будете делать по оригинальной версии, то обратите на это внимание.
- Рукоятка вынесена, как бы, за станок, что увеличивает требуемое свободное пространство. В дальнейшем я буду переносить ее ближе к шпинделю посредством цепной передачи.
- Передний центр (зубчатая штука, которая вращает деревянную заготовку) очень плохо удерживает заготовку. Конструкцию надо менять.
И не забывайте при работе пользоваться средствами индивидуальной защиты. Не нарушайте требования техники безопасности, какими бы они глупыми и смешными не казались.
Краткое описание процесса бурения
Нефтяная скважина создается путем бурения скважины диаметром от 5 до 36 дюймов (127,0–914,4 мм) в земле с помощью буровой установки, которая вращает бурильную колонну с присоединенным долотом.
Вот основные этапы бурения скважины:
— Буровая коронка с помощью веса бурильной колонны и утяжеленных бурильных труб над ней взламывает землю.
— Буровой раствор (раствор) закачивается внутрь бурильной трубы и выходит из бурового долота, помогая разрушать породу, поддерживая давление на вершине долота, а также очищая, охлаждая и смазывая долото.
— Образовавшаяся порода уносится буровым раствором, когда он циркулирует обратно на поверхность за пределами бурильной трубы.
— Шлам и возвращаемые жидкости контролируются на предмет отклонений от нормы для обнаружения возможных скачков давления.
— Труба или бурильная колонна, к которой крепится долото, постепенно удлиняется по мере того, как скважина становится глубже, путем ввинчивания нескольких 30-футовых (10 м) стыков труб на поверхности.
Этому процессу способствует буровая установка, которая содержит все необходимое оборудование для циркуляции бурового раствора, подъема и поворота трубы, контроля забойного давления, удаления шлама из бурового раствора и выработки электроэнергии на месте для этих операций.
Первые нефтяные скважины были пробурены в Китае в 4 веках или ранее. Они достигли глубины до 243 метров и были пробурены с помощью долот, прикрепленных к бамбуковым шестам.
Нефтяная промышленность Среднего Востока была основана в 8-990-1990-х годах, когда улицы недавно построенного Багдада были вымощены гудроном, полученным из нефти, которая стала доступной с природных полей в регионе.
Первая современная нефтяная скважина была пробурена в 1848 году русским инженером Ф.Н. Семёнов на полуострове Ашерон к северо-востоку от Баку. К 1861 году в Баку добывалось около 90% мировой нефти.
Слово «нефть» происходит от двух греческих слов, означающих каменное масло. Когда Эдвин Дрейк впервые обнаружил нефть в США в 1859 году, ему действительно было скучно на соль.
До 1970-х годов большинство нефтяных скважин были вертикальными. Благодаря наклонно-направленному и горизонтальному бурению появилась возможность достигать пластов на расстоянии нескольких километров от места бурения.
2.:
Задание 2. Заполните таблицу и задавайте вопросы, используя эти слова, как в примере:
Пример: Какова длина трубопровода? Какая длина трубопровода?
Прилагательное | Существительное |
длинный | |
Длина | |
широкий | |
Глубина | |
Высокая | |
Толстый | |
Тяжелый | Масса |
старые | |
цена |
3.. ‘Что …?’ ‘Как …?:
Задание 3. Ответьте на эти вопросы, используя слова из коробки. Каждый вопрос начинайте с «Что такое …?» или «Как …?»:
диаметр, длина, глубина, высота, толщина, стоимость, давление, ветер, нагрузка |
1. Q: _____ это колодец?
A: На этой установке несколько скважин.Самая глубокая — около 4500 метров.
2. Q: _____ на такой глубине?
A: Оно может достигать 15 000 фунтов на квадратный дюйм, поэтому у нас есть противовыбросовый превентор для предотвращения выбросов.
3. Q: _____ вышки?
A: От кронблока до рабочего этажа примерно 40 метров.
4. Q: _____ вышки?
A: Он может противостоять ветру со скоростью до 125 миль в час.
5. Q: _____ отверстия?
A: Отверстие сужается при спуске, но на поверхности оно составляет около 50 см.
6. Q: _____ бурильные трубы?
A: Эти трубы изготовлены из стали толщиной чуть менее 1 см.
7. Q: _____ бурильные трубы?
A: Длина каждого стыка составляет примерно 10 метров. Если они все одинаковые, это значительно упрощает хранение.
8. Q: _____ алмазной коронки?
A: Они очень дороги, от 12 000 до 15 000 долларов за штуку.
4.:
Задание 4. Изучите схему буровой установки и сопоставьте описания со словами на схеме:
Пример: Это поднимает и опускает буровое оборудование в скважину и из нее, подъемный трос.
1. К нему подвешены вертлюг и буровое оборудование.
2. Подъемный трос огибает это оборудование. Когда он поворачивается, линия идет вверх или вниз ..
3. Это стальная башня над колодцем. Внутри находится все подъемное и буровое оборудование. …..
4. Это соединяет два объекта. Он позволяет нижнему вращаться, а верхнему оставаться неподвижным. ..
5. Это небольшая площадка у вершины вышки, где стоит один из буровых бригад..
6. Это рама и колеса, которые перемещаются вверх и вниз по вышке на подъемном канате.
7. Это стальная рама и колеса, закрепленные на верхней части вышки.
5.:
Задание 5. Прочтите и переведите текст:
Бурильная колонна
Работы по бурению под землей выполняет бурильная колонна. Бурильная колонна состоит из ведущей трубы, секций бурильной трубы, утяжеленной бурильной трубы и долота для бурения породы.Келли — это прочная труба, которая всегда находится в верхней части бурильной колонны. Он имеет четыре или шесть сторон и проходит через поворотный стол, который вращается (вращается). Поворотный стол находится на буровой площадке. Между ведущей трубой и утяжеленной бурильной трубой проходит бурильная труба различной длины. Нефтяники добавляют секции бурильной трубы одну за другой к ведущей трубе. Каждый раз, когда они добавляют секцию, они поднимают келли из отверстия. Затем они добавляют кусок трубы наверху веревки и опускают ее обратно в землю.Внизу колонны мы можем найти утяжеленную бурильную трубу. Бита входит в воротник.
Биты обычно трехугольные, другими словами, они имеют три вращающихся конуса. Круглая коронка с отверстием посередине используется для отбора образцов керна. Сверла могут быть покрыты промышленными алмазами, чтобы продлить срок их службы. Буровой раствор перекачивается через форсунки в долоте — это смазывает и охлаждает его, а по мере циркуляции бурового раствора он также выносит на поверхность куски пробуренных обломков породы.
6.:
Задание 6. Закончите эти предложения:
1. Блок кроны — _____ вершина вышки.
2. Утяжеленная бурильная труба — это _____ долото и секции бурильных труб.
3. Член экипажа стоит _____ обезьяньей доской.
4. Келли движется _____ к поворотному столу.
5. Подъемный трос идет _____ лебедка.
6. Вертлюг является _____ крючком.
7.:
Задача 7. Сопоставьте задания с описанием:
1. Сотрудник компании а. отвечает за двигатели,
2. толкатель дрели b. общий помощник,
3. Человек с вышки. следит за поставкой грязи,
4. Грязевой человек d. руководит буровой бригадой,
5. Автолюбитель e. второй в команде,
6. roustabout f. представляет нефтяную компанию,
7.грубый воротник g. обрабатывает трубы.
7. Направленное бурение и проходка туннелей | Технологии бурения и земляных работ для будущего
с заканчиванием и производством, такими как цементирование хвостовиков, гравийная набивка и гидроразрыв.
Наклонно пробуренные скважины делятся на три основные категории. В первой категории задача состоит в том, чтобы добраться до мест, недоступных через прямые вертикальные отверстия.Например, может существовать неблагоприятный рельеф поверхности, такой как наличие зданий, холмов или воды над целевым местоположением. В качестве альтернативы, может быть пробурена наклонно-направленная скважина, чтобы избежать нежелательных участков в геологической среде, включая зоны разломов или области известных «трудных» горных пород (например, соли, набухающих сланцев и областей высокого давления). Может быть целесообразно пробурить наклонно-направленную скважину с безопасного расстояния, чтобы пересечь выбитую скважину. При разведочном бурении можно пробурить несколько наклонных испытательных стволов из одной и той же верхней части ствола, чтобы сэкономить на затратах на бурение и избежать перемещения установки.
Во второй категории целью является достижение значительного расстояния по горизонтали от места бурения. Этот метод, известный как бурение с «расширенным радиусом действия», используется для обеспечения доступа ко многим частям коллектора из одного места. Основное применение бурения с большим отходом от вертикали — это морские операции, где оно используется для уменьшения количества необходимых платформ. В последнее время бурение с увеличенным вылетом стало интересным для наземных операций, где экологические проблемы или ограничения городского пространства могут требовать землепользования.Сфера растущего интереса к бурению с большим отходом от вертикали — доступ к морским нефтяным месторождениям с берега, что приводит к снижению воздействия на окружающую среду и снижению затрат, связанных с наземным бурением.
При бурении с увеличенным вылетом максимальный вылет зависит от целевой глубины, а также от поддержания хороших условий в стволе скважины и достаточно крутого угла, чтобы буровая компоновка могла скользить вперед и оказывать нагрузку на долото. Технология быстро развивается.Текущая мировая рекордная скважина с увеличенным вылетом, пробуренная в Северном море, достигла цели на горизонтальном расстоянии 23 917 футов (4,53 мили) на глубине около 9 000 футов (Anon., 1993b). Длина отверстия составила 28 743 фута (5,44 мили).
Третью категорию составляют скважины, в которых часть скважины, лежащая в пласте, имеет определенную ориентацию для повышения продуктивности. Например, в вертикально тонком пласте горизонтальный ствол может контактировать с большей частью пласта, чем вертикальный, увеличивая площадь контакта с дренажем и задерживая образование конуса воды или газа.Геометрия коллектора помогает определить, использовать ли горизонтальную или вертикальную скважину; Горизонтальная скважина более продуктивна и, следовательно, более выгодна, чем вертикальная скважина, поскольку ширина коллектора увеличивается, а высота уменьшается.